SUS410材の加工における最適切削条件とは?
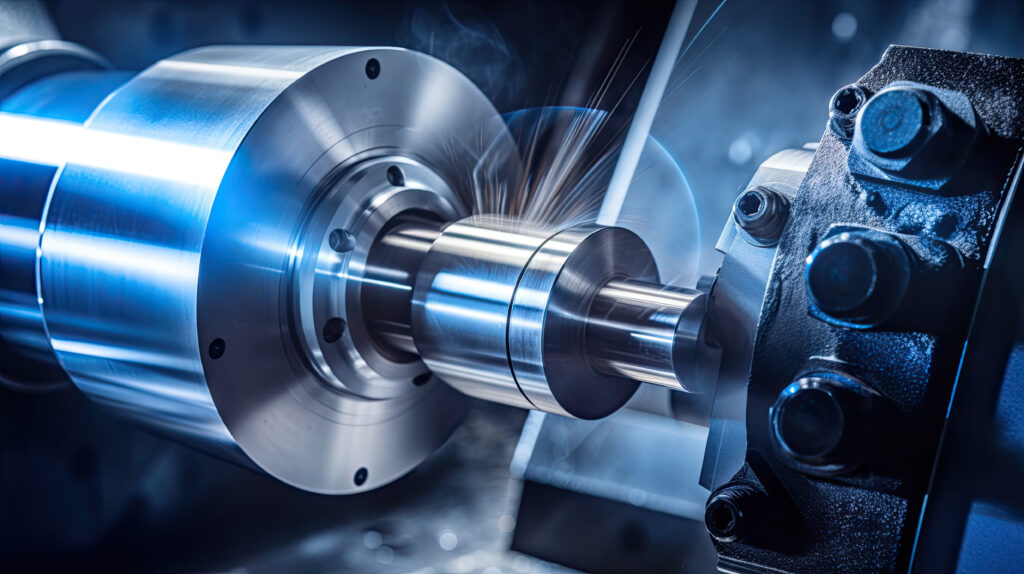
SUS410材という素材を使用する際、適切な切削条件を知ることは重要です。正しい切削条件を適用することで、作業効率が向上し、品質の向上にもつながります。今回の記事では、SUS410材の加工における最適な切削条件について探っていきましょう。素材特性や切削速度、刃先形状など、様々な要素が影響を与える中、どのように最適な条件を見つけるかを解説します。加工における成功の鍵となる切削条件について、詳しく知ることで、作業効率の向上を実現しましょう。
Contents
SUS410材の基礎知識
SUS410は、ステンレス鋼の一種で、主に耐摩耗性や耐腐食性が求められる用途に使用されます。SUS410は、フェライト系ステンレス鋼に分類され、特に熱処理を施すことで、その機械的特性を強化することができます。SUS410ステンレス鋼とは
SUS410は、炭素鋼にクロムを加えた合金であり、12%のクロムを含んでいます。これにより、腐食や摩耗に対する耐性が向上しますが、オーステナイト系ステンレス鋼に比べるとその耐腐食性は若干劣ります。SUS410は、硬度と強度を持つため、特に高温環境や耐摩耗性が要求される部品に使用されることが多いです。SUS410の特性と用途
SUS410の特性は以下の通りです:- 耐摩耗性: SUS410は耐摩耗性に優れており、摩擦を受ける部品や機械的負荷の高い部品に適しています。
- 耐熱性: 比較的高い温度での使用にも耐える特性を持ち、熱処理後には硬度が向上します。
- 耐腐食性: クロムを含んでいるため、耐腐食性がありますが、特に強酸や塩分が多い環境には適していません。耐食性を改善するためには表面処理やコーティングが必要です。
- 機械的強度: 高い引張強度を持ち、強度が必要な部品に適しています。熱処理によって、より高い硬度を実現できます。
- バルブ部品やポンプ部品: 高温・高圧環境において耐摩耗性が求められるため、SUS410はバルブやポンプ部品に多く使用されます。
- 自動車部品: エンジン部品やトランスミッション部品、歯車など、耐熱性や耐摩耗性を必要とする自動車部品に使用されます。
- 化学工業機器: 耐腐食性が要求される化学プラントの部品や設備に適しています。
- 医療機器: SUS410はその強度と耐腐食性から、医療機器や外科用器具にも使用されることがあります。
SUS410切削条件の理解
SUS410は、耐摩耗性や耐熱性に優れたステンレス鋼ですが、切削性が他の素材と比較してやや難しいことがあります。そのため、適切な切削条件を理解し、加工方法を選定することが重要です。切削性とは
切削性とは、材料が加工される際に、刃物と接触する部分で発生する摩擦、熱、圧力の影響を受けながら、どれだけ容易に切削できるかを示す指標です。切削性が良い材料は、加工がしやすく、切削工具の摩耗が少ないため、効率よく加工が進みます。逆に切削性が悪い材料は、工具の摩耗が早く、加工時間が長くなることがあります。切削加工の基本
切削加工の基本は、工具が材料に対して一定の圧力を加え、削り取ることによって形状を変えるプロセスです。加工条件には、主に以下の要素があります:- 切削速度: 切削工具が材料と接触している速度。適切な切削速度を選定することが重要で、速すぎると工具が過熱し、遅すぎると効率が低下します。
- 送り速度: 工具が材料に対して進む速度。これが速すぎると切削面が粗くなり、遅すぎると効率が悪くなります。
- 切削深さ: 切削する際に、工具が材料に進む深さ。切削深さが深いほど、一度に削る材料の量が増えますが、工具への負荷も大きくなります。
材質別の切削条件の違い
SUS410は他のステンレス鋼や炭素鋼と比較して、硬度が高く、切削性が劣るため、加工条件を慎重に設定する必要があります。以下は、SUS410と他の材質の切削条件の違いです:- 切削速度: SUS410は比較的硬い材料であるため、切削速度は他の材料に比べて遅めに設定することが推奨されます。高すぎる切削速度は、工具の摩耗を早め、加工精度が悪化する原因になります。
- 工具材料の選定: SUS410には、硬度が高く、耐摩耗性の優れた工具が必要です。超硬合金やCVD(化学蒸着)コーティングを施した工具が適しています。
- 冷却剤の使用: 高い温度が発生しやすいため、適切な冷却剤を使用することで工具の冷却と摩耗を抑え、加工精度を保つことができます。特に油性の冷却剤が効果的です。
- 送り速度と切削深さ: SUS410では送り速度や切削深さを適切に設定することが必要です。過度な送り速度は工具の摩耗を早め、切削面が粗くなります。
ステンレスの切削加工時の工具選定
ステンレス鋼はその硬度と耐摩耗性から、切削加工が他の金属より難しくなります。適切な工具選定を行うことで、加工効率を高め、工具の寿命を延ばし、精度の高い仕上がりを実現できます。工具材質の種類と特徴
ステンレス鋼の切削に使用される工具材質には、いくつかの種類があり、それぞれに特徴があります。以下は、主な工具材質とその特徴です。- 超硬合金: 非常に高い硬度と耐摩耗性を持つため、ステンレス鋼を含む硬い材料に最適です。耐熱性も優れ、切削中の温度上昇に強いです。しかし、脆いため衝撃には弱い点があります。
- コバルト合金: 強度が高く、耐摩耗性にも優れた合金です。特に、硬い材料の切削に向いており、切削時の発熱に強いです。
- セラミック: 高速切削に適しており、非常に高温でも優れた性能を発揮します。熱膨張が少ないため、精度を求める加工に適していますが、脆いため衝撃には不向きです。
- 高速度鋼 (HSS): 耐摩耗性と耐熱性に優れ、特に低速での加工に向いています。ただし、超硬合金ほどの耐久性はないため、ステンレス鋼の切削にはやや劣ります。
工具形状の選定ポイント
工具の形状は、切削時の負荷や加工する素材の特性に影響を与えます。ステンレス鋼を切削する際には、以下のポイントを考慮して工具形状を選定します。- 刃先の角度: ステンレス鋼は硬いため、切削時に発生する摩擦が大きいです。刃先角度を適切に設定することで、切削抵抗を軽減し、工具の寿命を延ばすことができます。一般的には、鋭角の刃先(小さな切削角度)は摩擦を減らし、切削性能を向上させます。
- 切り込み角: 切り込み角を調整することで、切削抵抗を下げ、加工がスムーズになります。ステンレス鋼では、切り込み角を小さめに設定することが多いです。
- 工具のリード角度: リード角度が大きいほど切削抵抗が減り、切削性能が向上します。リード角度は加工条件に応じて選定する必要があります。
刃先のコーティング
ステンレス鋼は高温環境下での加工になるため、切削中に摩耗や熱が発生しやすいです。これを防ぐために、工具の刃先にはコーティングを施すことが一般的です。代表的なコーティングには以下があります。- TiN (窒化チタン): 一般的に使用されるコーティングで、硬度が高く、耐摩耗性、耐熱性が優れています。ステンレス鋼の切削に非常に効果的です。
- TiAlN (窒化チタンアルミニウム): TiNよりも耐熱性が優れており、高温での加工に適しています。耐摩耗性がさらに高く、ステンレス鋼や高温合金の切削に適しています。
- TiCN (窒化チタンカルシウム): TiNよりも耐摩耗性が高く、切削時の摩擦を減らすことができます。硬いステンレス鋼の加工に適しています。
- ダイヤモンドコーティング: 高硬度を持ち、非常に硬い材料の切削に向いています。摩耗が少なく、長寿命を持ちますが、高コストなため特定の用途に限定されます。
ステンレス鋼の切削加工の難しさと課題
ステンレス鋼はその特性から切削加工が難しく、他の金属と比較して加工性においていくつかの問題点が発生します。これらの課題に対して適切な解決策を講じることが、効率的な加工を実現するためには不可欠です。ステンレス鋼の加工性の問題点
ステンレス鋼の切削加工において、以下のような問題が主に発生します。- 高い硬度と耐摩耗性: ステンレス鋼は比較的硬く、摩耗しにくいため、切削工具の摩耗が早く進行します。このため、工具寿命が短く、頻繁に交換が必要となり、コストが増加します。
- 高い切削温度: ステンレス鋼は熱伝導性が低いため、切削中に発生する熱が工具や材料に集中しやすいです。これにより、工具の温度が上昇し、耐久性が低下します。また、切削面が変色しやすく、品質に影響を与えることがあります。
- 切削抵抗の大きさ: ステンレス鋼の切削には高い切削抵抗が伴います。このため、切削力が大きくなり、加工機械に過度の負荷をかけることがあり、加工中の振動や切削音が大きくなることがあります。
- ギャップや表面品質の問題: 切削後に不均一な表面品質が現れやすく、光沢仕上げや精度が求められる場合には難易度が増します。切削中に微細なひび割れや表面欠陥が発生することもあります。
切削加工時の課題と解決策
ステンレス鋼の切削加工における課題に対する解決策としては、以下のアプローチが有効です。- 切削条件の最適化: 切削速度や送り速度、切削深さを最適化することで、切削中の摩耗や発熱を最小限に抑えることができます。低速で高い送り速度を選択し、熱の蓄積を防ぎます。
- 適切な冷却剤の使用: 冷却剤や切削油を適切に使用することで、工具や材料の温度を下げ、摩擦や発熱を抑えることができます。切削中の冷却が適切でないと、材料が焼き付きやすくなるため、冷却剤は重要な要素となります。
- 切削工具の選定: ステンレス鋼の加工には、硬度や耐熱性に優れた工具材質が必要です。超硬合金やコバルト合金、またはコーティングされた工具を使用することで、摩耗を抑制し、加工精度を高めます。また、刃先形状を工夫することで切削力を軽減できます。
- 振動の抑制: 加工中の振動を減らすために、加工機械の剛性を向上させたり、最適な切削パラメータを使用することが重要です。振動が大きいと、加工面が荒れる原因となります。
熱処理と切削加工の関係
ステンレス鋼の熱処理は、切削加工に大きな影響を与える要因となります。熱処理と切削加工の関係については以下の点が挙げられます。- 焼入れと硬度の上昇: ステンレス鋼は熱処理によって硬度が増し、切削加工がさらに難しくなります。焼入れ後の材料は非常に硬くなるため、切削工具に対する負荷が大きくなります。加工時には、硬度に対応した適切な工具の選定と切削条件が必要です。
- 焼鈍しによる加工性の改善: 焼鈍処理を施すことで、ステンレス鋼の硬度が低下し、加工性が改善されます。このため、切削加工がしやすくなり、工具寿命の延長や表面品質の向上が期待できます。焼鈍処理後のステンレス鋼は、柔らかくなるため切削負荷を減らすことが可能です。
- 熱処理による内部応力の解放: ステンレス鋼は熱処理により内部応力が解放され、加工中のひずみや歪みが抑えられます。これにより、より高精度で安定した切削加工が可能になります。
切削の最適条件の探求
切削加工において最適な条件を設定することは、効率的で高品質な加工を実現するために非常に重要です。切削速度や送り速度、切り込み深さ、冷却液の使用方法など、各要素を適切に調整することで、加工性を最大化し、工具の寿命を延ばすことができます。切削速度の設定
切削速度は、加工対象となる材料と使用する工具に応じて最適な設定を行う必要があります。切削速度が速すぎると、工具の摩耗が早く進行し、熱の発生も増加します。逆に遅すぎると、加工効率が低下するだけでなく、切りくずの処理が難しくなることがあります。最適な切削速度は、以下の要因に基づいて決定されます。- 材料の硬度: 硬い材料は低速で切削するのが一般的です。逆に柔らかい材料は高速での加工が可能です。
- 工具材質: 工具が耐熱性や耐摩耗性を持つほど、高速での切削が可能です。
- 加工目的: 高精度が求められる場合は、低めの切削速度が好まれます。粗加工では高速切削が可能です。
送り速度と切り込みの深さ
送り速度と切り込みの深さは、切削効率に大きな影響を与えます。送り速度が速すぎると、切削力が大きくなりすぎて工具に負担がかかりますが、遅すぎると生産効率が低下します。また、切り込みの深さは、材料の加工難易度に応じて設定する必要があります。- 送り速度の設定: 送り速度は、材料の形状や硬さに応じて最適化します。高い送り速度は、生産性を向上させますが、工具への負担が大きくなりやすいです。適切な速度設定で安定した加工を目指します。
- 切り込みの深さ: 切り込み深さは、材料の厚さや工具の性能に基づいて調整します。浅い切り込みであれば工具の負荷が少なくなり、精度が向上しますが、深い切り込みでは効率的な加工が可能になります。
冷却液の使用と管理
冷却液は切削中に発生する熱を効果的に抑えるために重要な役割を果たします。また、冷却液は工具の摩耗を減少させ、切りくずの排出を助け、加工面の品質向上にも寄与します。冷却液の適切な使用と管理は、切削条件の最適化に欠かせません。- 冷却液の選定: 加工する材料や工具に最適な冷却液を選ぶことが重要です。冷却液は油性、乳化タイプ、水溶性などさまざまな種類があり、用途に応じて使い分ける必要があります。
- 冷却液の供給量と方法: 冷却液は十分な量で供給し、加工中に継続的に冷却が行われるようにします。また、冷却液の流れを適切に管理することで、材料や工具の温度上昇を防ぐことができます。
- 冷却液の温度管理: 冷却液の温度が高すぎると冷却効果が低下し、加工効率が悪化するため、適切な温度管理が求められます。
ステンレス鋼の加工時の要因バランス
ステンレス鋼の加工は、他の金属材料に比べて難易度が高いとされています。そのため、加工精度、表面品質、工具耐久性、コストなど、複数の要因をバランス良く考慮する必要があります。これらの要因が適切に調整されることで、最適な加工結果が得られます。加工精度と表面品質
加工精度は、部品が規定の寸法や形状に従って正確に加工されることを意味します。ステンレス鋼は硬度が高く、切削時に摩擦が発生しやすいため、表面品質が低下することがあります。そのため、次の点を考慮することが重要です。- 工具の選定: 高精度の加工を求める場合、切れ味の良い工具を選定し、適切な切削条件を設定します。
- 切削条件の最適化: 切削速度や送り速度、切り込み深さを調整し、表面に傷がつかないように加工します。また、切削液を適切に使用することで、摩擦熱を抑え、表面品質を向上させます。
- 後加工の必要性: 表面が粗い場合は、研磨などの後加工を行うことがあります。表面粗さをコントロールし、最終製品の品質を確保します。
工具耐久性とコスト
工具耐久性は、加工中に工具が摩耗する速度に影響します。ステンレス鋼の加工では、硬さや靭性のために工具が急速に摩耗することが多く、工具交換頻度が高くなる可能性があります。これに関連するコストと労力を管理するためには以下の点が重要です。- 工具材質の選定: ステンレス鋼に対して高い耐摩耗性を持つ工具を選択します。例えば、コーティングツールを使用することで工具寿命が延びます。
- 切削条件の設定: 高速での切削は効率的ですが、過度な切削は工具に過負荷をかけ、摩耗が早く進行します。適切な条件での加工により、工具寿命を延ばし、コスト削減が可能です。
- 工具交換のタイミング: 工具の摩耗状態を定期的にチェックし、最適なタイミングで交換することで、無駄なコストや時間を避けます。
加工環境の整備
加工環境もステンレス鋼の加工品質に大きく影響します。加工中の熱管理、切削液の供給、振動管理など、様々な環境要因を適切に整備することが必要です。- 温度管理: ステンレス鋼は熱に敏感であり、加工時に発生する熱が部品や工具に悪影響を及ぼすことがあります。冷却システムや切削液を適切に使用して、加工中の温度を抑えることが重要です。
- 振動管理: 切削時の振動は加工精度に影響を与えるため、機械の安定性を確保し、振動を最小限に抑えることが必要です。加工中の安定性を保つために、工具や機械のメンテナンスを定期的に行います。
- 作業環境の整備: 作業環境の清潔さを保ち、加工中の汚れや切りくずが加工精度に影響を与えないようにすることも大切です。適切な換気や切りくずの排出システムの整備も有効です。
ステンレス鋼旋削加工のインサートシリーズ
ステンレス鋼の旋削加工では、適切なインサートの選定が非常に重要です。インサートは加工精度や工具寿命、コストに大きな影響を与えるため、選定基準に基づいて最適なものを選ぶことが求められます。インサートの種類と特性
インサートは、切削工具の先端に取り付ける交換可能な刃物部分で、材質や形状によって多様な種類があります。ステンレス鋼の旋削加工においては、以下のようなインサートが使われます。- セラミックインサート: セラミックは非常に硬く、耐摩耗性に優れていますが、脆いため、優れた冷却液管理が求められます。高切削速度での使用に適しています。
- CBN(立方晶窒化ボロン)インサート: CBNは非常に硬く、ステンレス鋼のような硬い材料に適しています。特に精密加工に向いています。
- コーティングインサート: インサート表面にコーティングを施すことで、耐摩耗性や耐熱性が向上し、長寿命を実現できます。TiNやTiAlNなどが代表的なコーティングです。
- 超硬インサート: 超硬合金で作られたインサートは、耐摩耗性と強度のバランスが良好で、ステンレス鋼の旋削加工において広く使用されています。
インサートの選択基準
インサートを選定する際には、加工する材料の特性、加工条件、加工目的に応じて最適なものを選ぶ必要があります。選定基準は以下の通りです。- 材料の硬度: ステンレス鋼の硬度に適したインサートを選ぶことで、長寿命と安定した加工を実現できます。硬い材料にはセラミックやCBNインサートが適しています。
- 切削条件: 高速での切削が求められる場合、耐摩耗性の高いインサートが必要です。逆に低速での加工では、コストパフォーマンスの良い超硬インサートが適しています。
- 表面品質: 精度や表面仕上げが重視される場合は、精密加工用のインサート(例えばCBNインサート)を選ぶことが重要です。
- 冷却液管理: 冷却液の使用状況にも注意が必要です。冷却性能が低い場合、インサートの摩耗が早く進むことがあります。
インサートの交換とメンテナンス
インサートの交換とメンテナンスは、工具寿命を延ばし、加工精度を維持するために重要です。- インサートの交換タイミング: インサートは摩耗や欠けが進行すると、加工精度や表面品質が低下します。適切なタイミングで交換することで、加工の安定性を保ちます。一般的には、目視や切削音で摩耗の兆候を確認し、交換のタイミングを決定します。
- インサートの取り扱い: インサートは硬いため、扱い方にも注意が必要です。インサートの表面を傷つけないように、適切なツールで取り扱います。
- 研磨と再利用: 一部のインサートは、摩耗が少ない場合には研磨して再利用することができます。しかし、過度に摩耗したインサートは性能が低下するため、再利用しない方が良い場合もあります。