SUS303の加工における最適な切削条件とは?
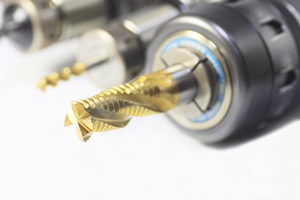
SUS303の加工における最適な切削条件をご存知ですか?金属加工に携わる方々にとって、切削条件は非常に重要です。SUS303という材料は、その特性から切削において特別な配慮が必要とされます。本記事では、SUS303の加工における最適な切削条件について詳しく解説していきます。加工精度や効率を向上させるために必要な情報がここにあります。さあ、最適な切削条件を見つけて、より効果的な加工を実現しましょう!
SUS303は、「高精度×高生産性×低コスト」を実現しやすい鋼種として、量産部品の旋削加工やフライス加工、NC加工を行う町工場や加工メーカーにとって理想的な選択肢です。用途や環境に応じて正しく選定し、最適な切削条件を設定することで、コスト効率と品質を両立できます。
SUS303の切削加工では、「加工条件 × 工具選定 × 冷却管理」の3点が成功の鍵となります。適切な条件を設定することで、高効率・高精度・長寿命の加工体制が構築可能となり、コスト削減にもつながります。
SUS303の切削加工では、加工方法ごとの特徴を理解し、工具・条件・潤滑を最適化することが最大の効率化策です。各加工の場面で「熱管理と切りくず処理」を念頭に置くことで、品質・加工速度・工具寿命のすべてを高水準で両立できます。
フライス加工におけるSUS303は、条件設定次第で高能率と高寿命の両立が可能な素材です。切削熱、切りくず、工具の摩耗—この3要素を適切に制御することで、加工トラブルの防止と生産性の最大化が実現できます。
SUS303の切削精度を高めるには、単に工具や条件を変えるだけでは不十分です。工程設計・環境管理・装置精度の総合的なバランスが重要となります。小さな工夫の積み重ねが、高精度・高品質な加工結果へと直結します。
Contents
SUS303の特性と一般的な切削加工の概要
SUS303とは:基本的な材料知識
SUS303は、オーステナイト系ステンレス鋼(JIS G4303に準拠)に分類される鋼種で、SUS304をベースに快削性(かいさくせい)を高めるために硫黄(S)やセレン(Se)を添加した特殊鋼です。JIS記号では「SUS303」、国際的には「AISI 303」「UNS S30300」とも呼ばれます。主な化学成分
- クロム(Cr)…17~19%
- ニッケル(Ni)…8~10%
- 硫黄(S)…0.15%程度(快削性のため)
特徴
- 高い耐食性(SUS304と比較するとやや劣る)
- 優れた切削性と加工効率
- 非磁性(冷間加工後に微弱な磁性を帯びることあり)
- 溶接には不向き(硫黄の影響によるホットクラックの懸念)
一般的なステンレス鋼の加工の課題
ステンレス鋼全般における切削加工では、以下のような課題が挙げられます。1. 低い熱伝導率
切削熱が工具先端に集中しやすく、バリの発生や工具摩耗が進行しやすい傾向があります。2. 加工硬化しやすい
オーステナイト系は加工硬化性が高く、切削点で硬化層が形成されると工具への負荷が急増します。3. 粘性が高く切りくず排出が困難
切削時に切りくずが工具に巻き付きやすく、切削面の粗れやビビリが発生するリスクがあります。 そのため、一般的なステンレス鋼(SUS304など)は、切削条件・工具選定・切削油の使用が極めて重要となります。SUS303切削加工の重要ポイント
SUS303はこれらの課題に対して、加工性を高めるための工夫が施された鋼材です。以下のような点が、SUS303を使う上でのポイントになります。1. 優れた快削性
硫黄添加により切りくずが細かく砕けやすく、高送り・高速切削でも良好な仕上がりが得られます。2. 工具寿命の延長
被削材としての摩擦が減少するため、工具摩耗が抑えられ、工具コストを低減できます。3. 精度と量産性の両立
高精度が求められる精密部品加工においても、SUS303は高い寸法安定性と良好な表面粗さが得られ、量産にも適します。4. 切削条件の最適化
- 工具材質:超硬工具やコーティング工具(TiAlN等)が推奨されます
- 切削油:不活性タイプまたは極圧添加剤入りの切削油を使用
- 切削条件:高速回転と高送りで効率的な加工が可能(工具メーカー推奨条件を参照)
5. 注意点
- 耐食性はSUS304よりやや劣るため、水分・薬品がかかる環境では材質選定に注意が必要です。
- 硫黄添加によって溶接性が低下しているため、溶接工程が含まれる場合はSUS304等との使い分けが重要です。
SUS303は、「高精度×高生産性×低コスト」を実現しやすい鋼種として、量産部品の旋削加工やフライス加工、NC加工を行う町工場や加工メーカーにとって理想的な選択肢です。用途や環境に応じて正しく選定し、最適な切削条件を設定することで、コスト効率と品質を両立できます。
SUS303切削加工の基本
SUS303は、快削性に優れたオーステナイト系ステンレス鋼であり、旋削加工・フライス加工・タップ加工など、幅広い切削工程で安定した仕上がりが得られる材料です。ただし、加工品質や工具寿命を最大化するには、適切な切削条件・工具の選定・冷却潤滑管理が不可欠です。切削条件の基礎
SUS303は一般的なステンレス鋼(例:SUS304)より加工性が高いとはいえ、加工硬化・熱集中・切りくず処理の課題は依然として存在します。下記の要素をバランスよく設定することが重要です。主な切削条件の要素
- 切削速度(Vc):高すぎると工具摩耗、低すぎると切りくず詰まりが発生
- 送り速度(f):加工目的に応じた調整が必要(仕上げ加工なら低め、荒加工は高め)
- 切込み量(ap):工具負荷を考慮しながら安定切削を優先
- 加工深さ・多段階加工の調整:硬化層の影響を避けるための工夫が必要
推奨例(旋削加工時)
- 切削速度:80〜160 m/min
- 送り:0.1〜0.3 mm/rev
- 切込み:1.0〜3.0 mm
切削工具の選定
SUS303は快削鋼であり、高い加工効率を発揮できる反面、工具選定を誤ると摩耗・チッピングの原因になります。以下に選定のポイントを示します。工具材質の選び方
- 超硬工具(Cemented Carbide):耐摩耗性・耐熱性に優れ、量産加工に適する
- コーティング工具(TiN、TiAlN、AlCrNなど):切削熱を抑え、工具寿命を延長
- 高速鋼(HSS):低コストだが、寿命・熱への強さはやや劣る(小径穴加工に有効)
工具形状の工夫
- 逃げ角とすくい角の調整:被削材への食い込みを安定化
- 切りくず処理性の良いチップブレーカ:切りくず巻きつきを防ぐ
- タップ加工の場合:スパイラルタップやポイントタップが適切
潤滑と冷却の役割
SUS303加工における切削油(潤滑・冷却)の適切な管理は、加工面の品質と工具寿命に直結します。特に、熱のこもりやすいSUS材では冷却性能が不可欠です。潤滑の役割
- 摩擦を低減し、工具と材料の密着による焼き付きやビビリを抑制
- 表面粗さの改善(滑らかな仕上がり)
冷却の役割
- 切削熱の除去による工具温度の低下・延命
- ワークの熱変形抑制、寸法安定性の確保
使用される切削油の種類
- 不活性型切削油:冷却重視、加工面をきれいに保つ
- 極圧添加剤入り油剤:難削材・高荷重時に有効(摩耗を抑制)
- 水溶性クーラント:大量冷却が必要な高回転加工に適する
クーラント供給方法
- フラッディング(多量供給)
- ミスト供給(工具の局所冷却)
- 高圧クーラント(深穴・高精度加工向け)
SUS303の切削加工では、「加工条件 × 工具選定 × 冷却管理」の3点が成功の鍵となります。適切な条件を設定することで、高効率・高精度・長寿命の加工体制が構築可能となり、コスト削減にもつながります。
SUS303の効率的な切削加工方法
SUS303は、快削添加元素(硫黄やセレン)を含むことで一般的なステンレス鋼より切削性に優れた素材です。しかし、加工硬化しやすく、切りくず処理や熱集中に注意が必要な点は他のステンレス材と同様です。以下に、加工方式別に最適な条件と効率化のコツを解説します。フライス加工における最適条件
フライス加工では、切削熱の分散と切りくず排出性が効率性のカギとなります。以下の点を重視しましょう。推奨切削条件(一般目安)
- 切削速度(Vc):80〜160 m/min
- 送り速度(fz):0.05〜0.15 mm/tooth
- 切込み(ap):0.5〜3.0 mm(仕上げ or 荒加工で調整)
工具選定と形状
- エンドミル:4枚刃以上の超硬エンドミルが最適(コーティング付き)
- 刃先形状:先端にマイクロチップブレーカを持つものが、切りくず処理に有利
- コーティング:TiAlNやAlCrNなど高硬度タイプで耐熱性を確保
効率化のコツ
- 切削熱が集中しないよう高圧クーラントやミスト冷却を併用
- クライミングカット(同方向切削)によりビビリ低減と工具寿命延長
- 深切削は多段階に分けて加工し、加工硬化層の影響を回避
ドリル加工時の留意点
SUS303のドリル加工では、食い付き・切りくず詰まり・熱の蓄積に注意が必要です。ドリル工具の選び方
- 超硬ドリル or 高速鋼(HSS)ドリル(コーティング付き)
- 先端角度:118〜135°、芯ブレの少ないセンタリングが重要
- スパイラル溝:深穴加工には大きめのねじれ角で切りくず排出を改善
推奨条件(φ10mm前後の場合)
- 切削速度:20〜40 m/min
- 送り速度:0.05〜0.2 mm/rev(工具と穴径による)
加工上の注意点
- 中間逃がし(チップブレーク)を行い、切りくず詰まり・焼付き防止
- パイロット穴を使ってセンター精度を確保
- クーラント供給は必須。内部給油式が望ましい
旋削加工でのコツ
旋削加工はSUS303に最も適した加工法の一つで、工具・条件の最適化で高効率かつ美しい仕上げが可能です。推奨切削条件
- 切削速度:80〜150 m/min
- 送り速度:0.1〜0.3 mm/rev
- 切込み深さ:1〜3 mm
工具とチップ選定
- 超硬チップ(CVDまたはPVDコーティング)
- すくい角が大きく、逃げ角が適切な設計
- チップブレーカ付きで切りくず排出をスムーズに
効率化のポイント
- 荒加工と仕上げ加工で送り・切込みを明確に分ける
- 加工温度が上がると硬化しやすいため連続加工を避ける
- 切りくず巻き付き防止に工具寿命や安全性への影響あり → クーラント必須
SUS303の切削加工では、加工方法ごとの特徴を理解し、工具・条件・潤滑を最適化することが最大の効率化策です。各加工の場面で「熱管理と切りくず処理」を念頭に置くことで、品質・加工速度・工具寿命のすべてを高水準で両立できます。
フライス加工におけるSUS303の具体的な切削条件
SUS303は、快削性に優れたオーステナイト系ステンレス鋼で、硫黄添加により一般的なSUS304より切削抵抗が低く、加工が比較的容易です。ただし、熱の蓄積や切りくず詰まり、工具摩耗には十分な対策が必要です。ここでは、実務に役立つ具体的なフライス加工条件とその管理方法について詳しく解説します。推奨される切削速度と送り速度
基本条件(超硬エンドミル使用時の目安)
- 切削速度(Vc): ・80〜160 m/min(仕上げ) ・50〜100 m/min(荒加工)
- 送り速度(fz): ・0.05〜0.15 mm/tooth(仕上げ) ・0.10〜0.25 mm/tooth(荒加工)
加工例(φ10エンドミル、2枚刃)
- 主軸回転数(n):約2,500〜5,000 rpm
- 送り速度(Vf):約250〜1,000 mm/min(条件により調整)
注意点
- 高送り時の熱集中に注意 → クーラント併用またはエアブローで冷却効率を向上
- 加工硬化層の形成を避けるため連続切削を推奨
切削深さと切りくずの管理
切削深さの目安(ap:切込み深さ)
- 仕上げ加工:0.2〜0.5 mm
- 荒加工:1.0〜3.0 mm(工具剛性と機械能力による)
切りくず管理の重要性
- SUS303は長く巻き付きやすい切りくずを生じやすい
- チップブレーカ付きエンドミルを使用することで分断性を向上
- 高圧クーラントまたはミスト式冷却で切りくず排出を補助
効果的な方法
- 溝加工や深堀加工では多段階加工に分ける
- 切りくずの滞留による焼付き防止に定期的な切削停止→排出が有効
工具の寿命とメンテナンス
工具寿命に影響する要因
- 刃先の摩耗進行(特に逃げ面)
- 溶着(ビルトアップエッジ)の発生
- 熱膨張による精度低下
工具寿命を延ばすコツ
- コーティング付き超硬エンドミル(TiAlNやAlCrN)を使用
- 送り速度を過度に上げすぎない
- 工具交換タイミングを回転数・切削負荷モニタで可視化
メンテナンスのポイント
- 刃先のチッピングや摩耗痕を定期確認
- 刃先研磨による再利用(再研磨可能工具の選定)
- 工具管理表や寿命ログの活用で交換サイクルを最適化
フライス加工におけるSUS303は、条件設定次第で高能率と高寿命の両立が可能な素材です。切削熱、切りくず、工具の摩耗—この3要素を適切に制御することで、加工トラブルの防止と生産性の最大化が実現できます。
SUS303切削加工の精度を高めるポイント
SUS303は快削性に優れる一方で、寸法精度や表面粗さにシビアな製品では注意が必要な素材です。特に熱膨張・加工変形・加工硬化などの影響を受けやすく、精度維持には高度な工程設計と管理が求められます。以下では、SUS303における加工精度向上のための要点を体系的に解説します。精度向上のための加工工程
多段階加工の採用
- 荒加工→中仕上げ→仕上げという工程分割が有効
- 各段階で工具負荷と熱変形を分散し、仕上げ時の寸法安定性を確保
中間冷却と安定化
- 荒加工後に素材を常温に戻す時間(数時間〜半日)を確保 → 内部応力と熱膨張の影響を軽減
クランプ方法の工夫
- 過剰な締め付けによる歪み防止
- 接触面積を広く保ち、均一な保持力で振動と変形を抑制
表面仕上げの技術
仕上げ工具の選定
- 高精度仕上げ用エンドミル(超硬、鏡面コーティング)
- 刃数が多い(4〜6刃)エンドミルで低振動・微細切削
加工条件の最適化
- 低送り・高回転が基本(例:Vc=120〜160 m/min, fz=0.03〜0.07 mm/tooth)
- 切り込み量を浅く(ap=0.1〜0.2 mm)して表面粗さRa 0.8μm以下を目指す
冷却・潤滑の最適化
- ミストや水溶性クーラントを使い、切削熱を抑えて表面酸化や硬化を防止
加工誤差の最小化
工具摩耗の管理
- 微細加工では0.01mm以下の刃先摩耗が寸法誤差に直結 → 加工前後に工具状態のチェックと交換基準の設定が重要
加工順序とバランス
- 対称加工(左右・上下)を取り入れることで加工応力を均等化
- 形状変形の原因となる偏った取り代や片側仕上げを避ける
加工機の安定性
- 加工精度の限界は機械剛性・真直度・温度制御に依存
- 加工開始前に主軸暖機運転(約20〜30分)を行うことで寸法安定化
SUS303の切削精度を高めるには、単に工具や条件を変えるだけでは不十分です。工程設計・環境管理・装置精度の総合的なバランスが重要となります。小さな工夫の積み重ねが、高精度・高品質な加工結果へと直結します。
SUS303とSUS304の違いと使い分け
ステンレス鋼の中でも、SUS303とSUS304は汎用性と入手性に優れた代表的なオーステナイト系ステンレスです。しかし、それぞれに異なる特性と適用分野があり、目的や加工条件に応じた適切な使い分けが重要です。
材料特性の比較
特性項目 | SUS303 | SUS304 |
---|---|---|
化学成分 | 硫黄(S)やセレン(Se)を添加 | S含有量が少なく純度が高い |
耐食性 | SUS304よりやや劣る | 高い耐食性を有する |
機械的性質 | やや脆い傾向あり(延性・靭性低め) | 靱性・延性が高く、成形性良好 |
快削性 | 非常に優れる(快削鋼) | やや劣る |
加工硬化性 | 少なめ | 高め |
溶接性 | 不向き(硫黄による割れの懸念) | 非常に良好 |
コスト | やや高い | 標準的 |
適用分野と選定基準
SUS303の主な用途
- ネジ・ボルト・シャフト類
- 小物部品・機械加工部品
- 旋削・フライス・ドリル加工向け製品
→ 大量切削・短納期対応・機械加工性重視の場面で選定
SUS304の主な用途
- 厨房機器・医療機器・建材・配管
- 溶接・プレス・曲げ加工品
- 屋外・水回りの部材
→ 耐食性・溶接性・外観仕上げ性重視の場面で選定
加工性の違いに基づく使い分けのポイント
SUS303の加工性の特徴
- 快削添加元素(S, Se)により切りくず分断性が高く、刃持ちが良く仕上げ精度も安定
- 高速加工・NC旋盤・量産ラインとの相性が良い
- ただし、バリが出やすく、靱性に欠けるため強度部品には注意が必要
SUS304の加工性の特徴
- 加工硬化を起こしやすく、切削抵抗が大きい
- 工具摩耗が早く、切りくずが伸びて絡まりやすい
- 曲げ・深絞りなどの塑性加工には非常に適する(冷間圧延性に優れる)
選定の実務ポイント
- 旋盤・フライスなどで加工効率を重視する場合 → SUS303
- 溶接・曲げ加工や外装用部品で美観・耐食性重視 → SUS304
- コストと性能のバランスを考慮し、部品単位で混在使用することも一般的