工具寿命を延ばす!SUS440Cの効率的な切削条件設定術
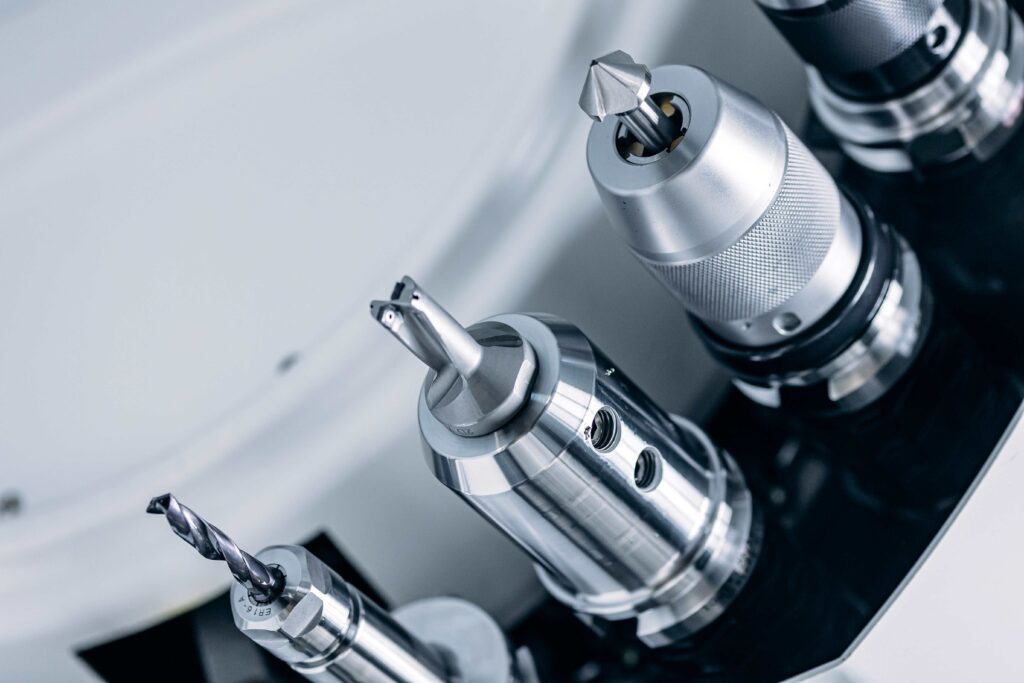
工具寿命を延ばすためには、素材の特性や切削条件を正しく理解することが欠かせません。特に、高耐食性を持つSUS440Cという材料に対して効率的な切削条件を設定することは重要です。切削条件の最適化によって、工具の寿命を延ばし、作業効率を向上させることが可能となります。本記事ではSUS440Cの特性や効率的な切削条件設定術について詳しく解説します。工具寿命を延ばし、作業効率をアップさせるためのヒントが満載ですので、ぜひご覧ください。
Contents
SUS440Cの基本と切削特性
SUS440Cは、高炭素で高クロム含有のステンレス鋼で、耐摩耗性や耐食性に優れ、主に高強度が求められる部品に使用されます。このセクションでは、SUS440Cステンレス鋼の基本的な特徴と、その切削加工における特性について詳しく解説します。SUS440Cステンレス鋼の特徴
SUS440Cは、炭素(C)含有量が約0.95~1.20%、クロム(Cr)含有量が16~18%の高炭素ステンレス鋼です。この合金は、耐食性と耐摩耗性に優れ、特に高強度が要求される部品に適しています。熱処理を施すことで硬度が大幅に向上し、耐摩耗性が高くなるため、主に軸受け、バルブ、ギアなどに利用されます。 この合金は、硬度が非常に高くなるため、切削性には制限があり、加工時に特別な配慮が必要です。高い硬度と耐摩耗性を持ちながらも、腐食への耐性も一定程度確保されています。したがって、SUS440Cは過酷な環境や高負荷がかかる機械部品に最適です。切削加工におけるSUS440Cの挑戦
SUS440Cの切削加工は、その高い硬度と耐摩耗性が原因で難易度が高いとされています。特に、硬度がHRC56~58に達することが多く、そのため、通常の切削工具では摩耗が早く、加工精度を維持することが難しくなります。 SUS440Cの切削性を向上させるためには、以下のような工夫が必要です:- 高性能な工具の使用: 超硬合金やコバルト系の切削工具を使用することで、加工時の摩耗を減少させ、工具の寿命を延ばすことができます。
- 適切な冷却剤の使用: 高温が発生することで、工具の摩耗が加速します。したがって、切削中に適切な冷却剤を使用することで、温度の上昇を抑え、加工精度を維持することが可能です。
- 低速回転での切削: 高速回転による熱の発生を避けるため、低速回転で切削することが望ましいです。これにより、切削時の温度を制御し、切削工具の耐久性を高めることができます。
旋盤加工におけるSUS440Cの速度と送りの最適設定
SUS440Cは高硬度のステンレス鋼であり、旋盤加工においては適切な速度と送りの設定が重要です。適切な加工条件を選択することで、工具の摩耗を抑え、加工精度を確保しつつ、効率的に加工することができます。旋盤加工の基礎
旋盤加工は、回転する素材に対して切削工具を送り込み、素材の表面を削り取る加工方法です。旋盤加工では、主に切削速度(回転数)、送り速度(工具の進行速度)、切削深さが加工効率と品質に大きな影響を与えます。特にSUS440Cのような高硬度の材料では、これらの設定が加工精度や工具寿命に直結するため、非常に慎重に設定する必要があります。速度と送りのバランスの重要性
切削速度(回転数)と送り速度(工具進行速度)のバランスは、SUS440Cの旋盤加工において非常に重要です。速度が速すぎると熱が過剰に発生し、工具の摩耗や素材の品質低下を引き起こします。一方で、速度が遅すぎると加工時間が長くなり、効率が低下します。 送り速度については、適切な設定を行うことで、加工中の切削力や振動をコントロールし、仕上がりの精度を保つことができます。過度な送り速度は切削抵抗が増加し、工具の摩耗を早める原因となります。SUS440C加工時の推奨速度と送りの設定
SUS440Cの旋盤加工時には、以下の条件を考慮して最適な速度と送りを設定することが推奨されます:- 切削速度(回転数): SUS440Cは硬度が高いため、低速での切削が推奨されます。回転数はおおよそ20~50 m/min程度を目安に設定します。これにより過剰な摩擦と熱を抑え、工具の寿命を延ばすことができます。
- 送り速度: 送り速度は0.05~0.2 mm/revの範囲で設定するのが一般的です。あまり速い送りで加工すると、切削力が増加し、加工精度が落ちる可能性があるため、適度な送り速度で加工することが重要です。
- 切削深さ: 初めに比較的浅い切削深さから始め、徐々に深くしていくのが理想的です。深すぎる切削は、工具の摩耗を加速させる原因となるため注意が必要です。
ステンレス鋼切削加工のポイント
ステンレス鋼はその耐食性や強度に優れている一方で、加工が難しい材料でもあります。切削加工においては、適切な切削条件、工具選定、切削液の使用が非常に重要です。これらの要素を適切に調整することで、効率的かつ高精度な加工を実現できます。切削条件の基本原則
ステンレス鋼の切削条件として重要なのは、切削速度、送り速度、切削深さの設定です。まず、切削速度に関しては、ステンレス鋼の硬度の高さを考慮し、過剰な速度を避ける必要があります。推奨される切削速度は、一般的に20~50 m/min程度で、これにより工具の摩耗を抑え、加工精度を維持することができます。また、送り速度については、送りが高すぎると切削力が増加し、加工精度が低下する可能性があるため、0.05~0.2 mm/revの範囲が適切です。切削深さについては、初期段階で浅い深さから始め、加工を進めながら深さを増加させる方法が望ましいです。ステンレス鋼加工のための工具選定
工具選定は、ステンレス鋼の加工において重要な役割を果たします。ステンレス鋼を加工するためには、耐摩耗性や耐熱性に優れた工具を選ぶことが不可欠です。具体的には、コーティングされた超硬工具やセラミック工具が一般的に使用されます。これらの工具は高い硬度を持ち、長寿命で精度の高い加工が可能です。また、工具の形状も重要です。鋭角な工具先端角度を持つ工具は、切削抵抗を低減し、良好な表面仕上げを得やすくなります。さらに、工具の冷却特性も重要で、冷却効果の高い工具を選択することで、加工中の温度上昇を抑え、工具の耐久性を向上させることができます。切削液の選択と使用方法
切削液の役割は、加工中の温度上昇を抑え、工具や材料の寿命を延ばすために重要です。ステンレス鋼の加工では、水溶性切削液や油性切削液がよく使用されます。水溶性切削液は冷却性能に優れ、油性切削液は潤滑性が高いため、使用する条件や加工内容に応じて選ぶことが大切です。切削液は、切削中に適切に供給することで、温度の上昇を抑制し、切削面の品質を向上させます。特に、高圧噴霧冷却を使用することで冷却効率が大幅に向上し、加工精度が維持されます。また、切削液の管理も重要です。長時間使用していると切削液は汚れていくため、定期的に切削液を交換し、清掃を行うことで、最適な切削条件を維持することができます。旋削加工の切削条件と加工結果への影響
旋削加工における切削条件は、加工結果に直接的な影響を与える重要な要素です。適切な切削条件を選択することで、加工精度や表面品質の向上、工具寿命の延長が期待できます。逆に、条件を誤ると加工不良や工具の早期磨耗を引き起こす可能性があります。ここでは、切削条件の調整方法とその影響について詳しく見ていきます。切削条件の調整方法
旋削加工における切削条件は、主に切削速度、送り速度、切削深さの3つで構成されます。これらの条件を調整することで、加工の効率や仕上がり具合をコントロールすることができます。まず、切削速度は適切な範囲に設定することが重要です。高すぎる切削速度は工具の摩耗を早める原因となり、低すぎると加工効率が低下します。通常、鋼材の加工には150〜250 m/min程度の切削速度が推奨されます。 次に、送り速度については、送りを速く設定すると加工時間が短縮されますが、仕上がり品質が低下する可能性があります。逆に、送りを遅くすることで表面品質が向上する一方で、加工時間が長くなります。最適な送り速度を選定することが、効率的で高品質な加工を実現します。 切削深さは一度に削る層の厚さを指し、浅い切削深さで加工する場合、摩擦が少なくなるため、工具への負担を減らすことができます。深い切削は、より多くの材料を削ることができるものの、工具へのストレスが増すため、段階的に切削深さを調整しながら加工することが推奨されます。加工精度と表面品質
切削条件は加工精度と表面品質に大きく影響します。切削速度が適切でない場合、加工面に加工硬化や焼きつきが生じ、表面品質が悪化することがあります。また、送り速度が速すぎると、表面に引きずり痕やツルツルな仕上がりが出ることがあり、反対に遅すぎると表面の荒れが目立つことがあります。切削深さも精度に影響を与えます。浅い切削を繰り返すことで、仕上げ面の品質が向上することが期待できます。 加工精度を高めるためには、安定した切削力と適切な切削液の使用が重要です。特に、精密加工を行う際には、過度な振動を避けることが求められます。振動は表面仕上げに悪影響を及ぼし、最終製品の精度を低下させる原因となります。工具寿命への影響
切削条件の設定が適切でない場合、工具の寿命にも大きな影響を及ぼします。高すぎる切削速度や過剰な切削深さは工具を急速に摩耗させ、交換の頻度が増えることになります。工具寿命を延ばすためには、適切な切削条件を選定することが必要です。 また、切削液の選択も工具寿命に影響を与えます。適切な冷却効果を持つ切削液を使用することで、工具の熱膨張や摩耗を防ぎ、長期間にわたって安定した加工を維持することができます。工具の摩耗を最小限に抑えるためには、高圧冷却や微細切削液供給の技術を取り入れることが効果的です。 総じて、切削条件の調整は加工精度や表面品質、そして工具寿命を最適化するための重要なステップです。各条件を最適に設定することで、品質の高い製品を効率よく生産することが可能になります。SUS440Cの量産フライス加工におけるコスト削減と品質維持
SUS440Cステンレス鋼は、硬度と耐摩耗性が高いため、量産フライス加工では非常に難易度が高く、コストや品質管理が重要な課題となります。ここでは、量産加工における効率化戦略、コストと品質のトレードオフ、そして持続可能な生産体制の構築について詳しく説明します。量産加工の効率化戦略
量産フライス加工においては、加工速度の最適化、切削工具の寿命延長、機械稼働率の最大化が効率化の鍵となります。まず、最適切削条件の選定が非常に重要です。SUS440Cは硬い素材であるため、切削速度を過度に速くすると工具の摩耗が早まり、逆に遅すぎると生産性が低下します。適切な速度と送り速度を選定することで、最適な生産性を実現できます。 さらに、工具の選定も効率化のポイントです。耐摩耗性の高いコーティング工具や、高精度の工具を使用することで、工具交換の頻度を減らし、無駄なコストを削減できます。また、自動化された工具交換システムや切削液の冷却効果を高める技術を活用することにより、稼働時間を最大化し、無駄なダウンタイムを最小限に抑えることができます。コストと品質のトレードオフ
量産においては、コスト削減と品質維持のバランスを取ることが重要です。SUS440Cの加工では、切削速度や送り速度を高めることで生産性を向上させることができますが、過度なスピードアップは表面仕上げの品質を損なう可能性があります。したがって、コスト削減と品質維持のトレードオフを適切に管理するためには、加工精度を確保する範囲内での速度調整が求められます。 品質を保ちながらコストを削減するためには、効率的な切削条件と加工時間の最適化が欠かせません。例えば、加工精度が重要な部分では少し遅い切削速度を設定し、その他の部分では最適化された高速加工を行うことが有効です。また、切削液の適切な使用も品質を保ちつつ、コストを削減する手段となります。持続可能な生産体制の構築
持続可能な生産体制を構築するためには、長期的な視点で設備投資や運用方法を見直す必要があります。例えば、エネルギー効率の高い機械や高性能切削液の使用、リサイクル可能な工具の採用などが挙げられます。これにより、生産コストを抑えると同時に、環境負荷を低減し、持続可能な製造を実現することができます。 また、予防保守の導入も重要です。設備や工具の状態を常に監視し、故障や不具合が発生する前に修理や交換を行うことで、ダウンタイムを最小限に抑え、効率的な生産を継続的に維持することができます。 加えて、作業員の技術研修や作業環境の改善も生産性向上に寄与します。高い技能を持つオペレーターが、正確で効率的に加工を行うことで、無駄な作業や失敗を減らし、品質の維持にも繋がります。 総じて、SUS440Cの量産フライス加工におけるコスト削減と品質維持は、切削条件の最適化、効率的な設備運用、そして適切な品質管理の3つの要素がバランスよく機能することで達成されます。これにより、安定した生産体制を構築し、長期的なコスト削減を実現することが可能になります。難削材SUS440Cの効率的な切削加工
SUS440Cは高い硬度と耐摩耗性を持つステンレス鋼であり、切削加工において非常に難易度が高い素材です。そのため、効率的な加工を行うためには適切な工具の選定と最適な切削条件の設定が不可欠です。以下では、コーテッド超硬エンドミルの選択方法と、高効率加工のための切削条件について説明します。コーテッド超硬エンドミルの選択
SUS440Cのような難削材を加工する際に最も重要なのは、使用する切削工具の選定です。コーテッド超硬エンドミルは、その耐摩耗性と高温耐性によって、SUS440Cのような硬い素材の加工に適しています。コーティングされた超硬材は、摩擦熱や加工時の荷重を軽減し、工具の寿命を延ばす効果があります。 特に有効なのは、TiAlN(チタンアルミナイト)コーティングやAlTiN(アルミニウムチタンナイトライド)コーティングです。これらのコーティングは高温でも耐久性を維持し、工具の摩耗を大幅に抑えるため、SUS440Cの加工においては非常に効果的です。さらに、多層コーティングのエンドミルは、摩擦を減らし、切削効率を高めることができます。高効率加工のための切削条件
SUS440Cの効率的な切削加工を実現するためには、適切な切削条件の設定が必要です。これには以下の要素が含まれます。- 切削速度: 切削速度は、工具の寿命と切削品質に大きな影響を与えます。SUS440Cのような硬い素材の場合、切削速度を過度に高くしないことが重要です。推奨される切削速度は、約20〜40m/minの範囲で設定します。具体的な値は、使用する工具の材質やコーティング、機械の性能に応じて調整する必要があります。
- 送り速度: 送り速度は、加工の効率を決定します。高い送り速度を選択することで、加工時間の短縮が可能になりますが、送りが速すぎると切削熱が増加し、工具の摩耗が進行します。送り速度は0.05〜0.1mm/回程度を目安に設定することが一般的です。
- 切削深さ(アプローチ): 高効率加工のためには、切削深さ(アプローチ)を適切に設定することが大切です。薄く広く削ることで切削負荷を分散させ、工具の温度上昇を抑えます。加工部位によって、切削深さを2〜4mm程度に設定することが推奨されます。
- 切削液の使用: SUS440Cの切削時には、適切な切削液を使用することが非常に重要です。高圧の切削液を使用することで、加工中の温度上昇を抑え、工具と素材間の摩擦を減らし、加工精度を向上させることができます。特に水溶性切削液やエマルジョンタイプの切削液が効果的です。
- 工具の冷却: 切削中に工具が高温になると、工具の摩耗や変形を引き起こす原因となります。クーラントの供給量を増加させたり、冷却機能が強化された工具を使用することで、温度を制御し、加工精度を保つことができます。