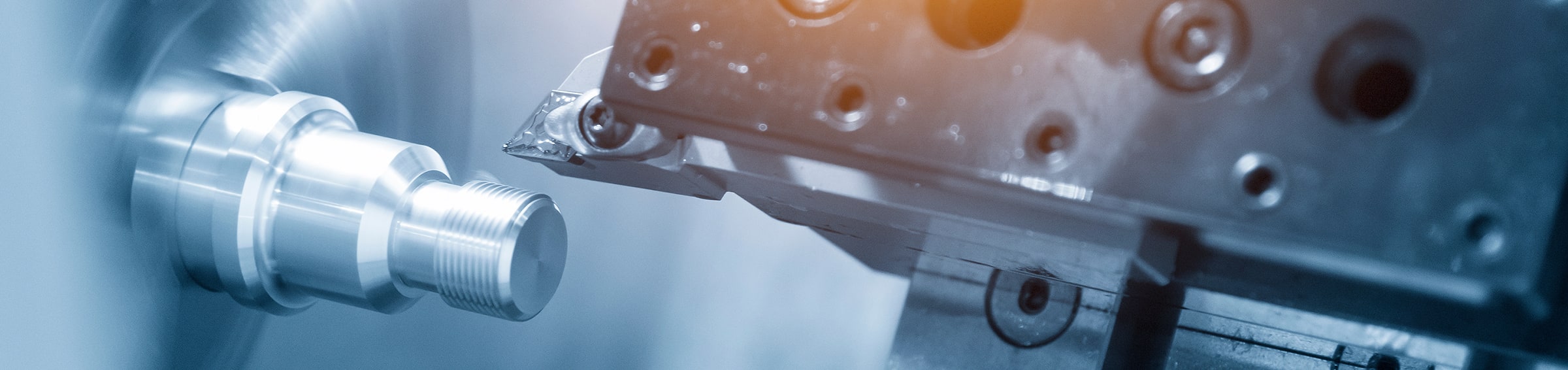
コラム column
SS400鋼材と他材質の強度比較ガイド
1: SS400鋼材の基本情報
1-1: SS400鋼材とは?
SS400は日本工業規格(JIS G3101)で規定された一般構造用圧延鋼材であり、主に建築や機械構造物に使われる汎用炭素鋼です。成分のバランスが良く、加工性や溶接性に優れているため、多様な用途で広く採用されています。
1-2: SS400の規格・特性
SS400は引張強度が約400~510MPa、降伏点が245MPa以上と定められており、均一な品質管理が行われています。成分は主に炭素(C)約0.05~0.25%、マンガン(Mn)約0.30~0.60%を含み、他の元素は微量に抑えられています。規格上、板材、形鋼、棒鋼など多様な形状があります。
1-3: SS400鋼材の機械的性質
引張強度、降伏点、伸び率、硬さなどの機械的性質がバランスよく備わっており、一般的な構造用鋼材として十分な耐荷重性と加工性を持っています。溶接性も良好で、切削加工や曲げ加工にも適しています。
1-4: SS400鋼材の用途
建築用骨組み、橋梁、機械フレーム、土木構造物、自動車部品、配管支持金具など、多くの分野で使用されており、特にコストパフォーマンスを重視した用途に適しています。
2: SS400鋼材と炭素鋼の強度比較
2-1: 炭素鋼の特性とは?
炭素鋼は炭素含有量によって硬さや強度、靭性が変化し、低炭素鋼から高炭素鋼まで幅広い種類があります。一般に炭素含有量が増すと強度が高まる一方で、加工性や溶接性は低下します。
2-2: SS400とS45Cの強度比較
SS400は低炭素鋼であり、引張強度が約400~510MPaなのに対し、S45Cは中炭素鋼で引張強度が約570~700MPaと高くなっています。S45Cは熱処理により強度をさらに向上可能で、強度が必要な機械部品に使われます。
2-3: 炭素鋼の引張強度
炭素鋼全般の引張強度は成分と熱処理によって異なりますが、一般的な低炭素鋼は約370~510MPa、中炭素鋼は約570~830MPaの範囲にあります。SS400はこの中でも比較的加工性と強度のバランスが良いグレードです。
2-4: 適切な用途と選定方法
用途の強度要求、加工性、コストを考慮し、SS400は構造用の汎用鋼材として選ばれます。より高い強度や耐摩耗性が必要な場合はS45Cなどの中炭素鋼を選定するのが一般的です。
3: SS400鋼材と合金鋼の比較
3-1: 合金鋼とは?
合金鋼は鉄にクロム、ニッケル、モリブデン、バナジウムなどの元素を添加し、耐摩耗性や強度、耐熱性を高めた鋼材の総称です。用途に応じて成分が最適化され、特殊な性能を発揮します。
3-2: SCM435の特性と強度
SCM435はクロムモリブデン合金鋼で、熱処理によって高い引張強度(最大980~1080MPa)と耐摩耗性を持ちます。機械部品や自動車部品など、強度と靭性が求められる用途に適しています。
3-3: SS400 vs SCM435の強度比較
SS400の引張強度は400~510MPaであるのに対し、SCM435は熱処理により900MPa以上の強度を持ち、約2倍以上の強度差があります。加工性はSS400が優れますが、高強度を必要とする部品ではSCM435が選択されます。
3-4: 合金鋼の加工方法
合金鋼は成分や熱処理により硬度が高いため、切削や成形加工時には工具の選定や加工条件に注意が必要です。溶接も難易度が高く、前後処理や適切な溶接技術が要求されます。
4: SS400鋼材とステンレス鋼の違い
4-1: ステンレス鋼の特性
ステンレス鋼はクロムを10.5%以上含み、表面に不動態皮膜(酸化膜)を形成することで優れた耐食性を示します。代表的な種類としてオーステナイト系(SUS304、SUS316)、フェライト系、マルテンサイト系があり、用途に応じて選択されます。耐熱性、耐薬品性にも優れており、強度と靭性のバランスが良いのも特徴です。
- クロム含有による耐腐食性
- 高温下での機械的強度維持
- 良好な加工性と溶接性
- 非磁性(オーステナイト系)
4-2: SS400 vs SUS304の強度比較
SS400は一般構造用炭素鋼で、引張強度は約400~510MPa、降伏点は245MPa程度です。耐食性は低く、防錆処理が必須です。一方、SUS304はオーステナイト系ステンレス鋼で、引張強度は520~750MPa、降伏点は約205MPaですが、耐食性に優れるため、湿潤・腐食環境下での性能が格段に高いです。
- SS400
- 引張強度:400~510MPa
- 降伏点:約245MPa
- 耐食性:低い(防錆処理必須)
- 用途:建築、構造物、機械部品
- SUS304
- 引張強度:520~750MPa
- 降伏点:約205MPa
- 耐食性:高い(酸化膜による保護)
- 用途:食品機器、医療機器、化学プラント
4-3: 引張強度の違い
SS400は構造用としての強度を持ち、安価で汎用性が高いのがメリットです。しかし耐食性が低いため、塗装や防錆対策が必須です。対してSUS304は引張強度が高い上に耐食性が優れているため、長期使用や過酷環境での信頼性が高いです。また、SUS304は伸び率(約40%)が高く、靭性が優れているため加工中の割れにくさにも優れます。
4-4: ステンレス鋼の用途
ステンレス鋼は耐食性が要求される多様な分野で活躍します。代表的には以下の用途があります。
- 食品加工・調理器具(衛生面重視)
- 医療・医薬品製造装置
- 化学・石油プラント設備(耐薬品性)
- 建築物の外装・内装材(耐候性)
- 海洋構造物・船舶部品(耐塩水腐食)
これらの用途では、SS400のような一般構造用鋼材では耐久性不足のため、SUS304などのステンレス鋼が選ばれます。
5: SS400鋼材の特性と加工方法
5-1: 加工技術と利点
SS400は炭素鋼として加工性に優れ、切削、曲げ加工、溶接などの一般的な機械加工が容易に行えます。材料が均一で安価なため、量産部品や一般構造用部材に多く使われています。特にプレス加工や板金加工での成形性が良好です。
- 加工のしやすさ(切削、曲げ、穴あけ)
- 溶接適性が高い(アーク溶接、TIG溶接など)
- 材料コストが低い
5-2: 溶接方法とその考慮点
SS400は各種溶接方法で対応可能ですが、溶接熱によるひずみや割れを防ぐため、適切な溶接手順の管理が必要です。特に厚板の場合は予熱や後熱処理が推奨されます。溶接部の強度を維持するため、材料の性質に合った溶接材料を選ぶことが重要です。
- アーク溶接、TIG、MAG溶接が主流
- ひずみや割れ防止のための熱管理
- 適切な溶接棒・ワイヤー選択
5-3: 熱処理による特性向上
SS400は焼鈍(アニーリング)や正火処理を行うことで内部応力を除去し、機械的特性の均一化が可能です。ただし、炭素鋼のため硬化処理(焼入れ・焼戻し)は一般に行われず、強度向上は限定的です。主に加工性や延性を改善する目的で熱処理が用いられます。
- 焼鈍処理で応力除去・延性向上
- 正火処理で組織の均一化
- 強度向上は限定的
5-4: 維持管理のポイント
SS400は耐食性が低いため、使用環境に応じて塗装や防錆処理が必要です。特に湿気や塩分のある環境では錆が発生しやすいため、定期的な点検とメンテナンスが重要です。腐食による強度低下を防ぐために適切な環境管理を行うことが長寿命化の鍵となります。
- 防錆塗装やメッキ処理の推奨
- 定期的な錆の確認と補修
- 適切な環境管理で劣化防止
6: SS400鋼材の強度一覧サンプル
6-1: 強度一覧表の見方
材料の引張強度、降伏点、伸び率、硬さは設計・選定に不可欠な指標です。引張強度は最大耐力、降伏点は永久変形の始まる応力、伸び率は塑性変形の能力を示します。硬さは摩耗抵抗の目安となります。
6-2: 各材質の強度データ
材質 | 引張強度 (MPa) | 降伏点 (MPa) | 伸び率 (%) | 備考 |
---|---|---|---|---|
SS400 | 400~510 | ≥245 | ≥20 | 一般構造用炭素鋼 |
SUS304 | 520~750 | ≥205 | ≥40 | オーステナイト系 |
S45C | 570~700 | ≥325 | ≥15 | 機械構造用炭素鋼 |
SCM435 | 700~900 | ≥490 | ≥12 | 合金鋼、強度高 |
6-3: 強度比較の実例
同じ厚さの部材を比較した場合、SUS304はSS400より高い引張強度を持ち、耐食性にも優れるため過酷な環境に適しています。しかしコストはSS400より高いため、用途や環境に応じて材料を選定します。構造物で腐食リスクが低い場合はSS400が合理的で、長期耐久性が求められる食品や化学装置にはSUS304が多く採用されます。
7: SS400鋼材の選定とコストパフォーマンス
7-1: コストと性能のバランス
SS400鋼材は、比較的低価格ながら十分な強度と加工性を兼ね備えているため、多くの構造物や機械部品で採用されています。コストパフォーマンスに優れ、建築資材や一般機械部品の材料として最適です。ただし、耐食性が低いため、防錆処理や環境条件を考慮した使用が前提となります。
- 低コストで入手しやすい
- 加工・溶接がしやすく量産に向く
- 使用環境に応じた防錆対策が必要
7-2: 選定時の注意点
SS400を選ぶ際は、使用環境や強度要求、加工方法を慎重に検討する必要があります。特に湿潤や塩害の強い環境では腐食リスクが高まるため、塗装やメッキ処理、場合によってはステンレス鋼などの耐食性素材との併用を検討します。また、溶接部の強度低下や熱影響に対する注意も不可欠です。
- 環境条件による腐食リスク評価
- 加工・溶接時の熱管理と技術力の確保
- 必要に応じて表面処理を施す
7-3: 市場における流通状況
SS400鋼材は国内外で広く流通しており、標準規格に基づいた安定供給が可能です。鋼材市場の変動や原料価格に影響を受けるものの、構造用鋼材としての需要は依然高く、建設業や製造業での使用量が多いです。中小の鉄鋼販売店から大手商社まで幅広く取り扱っています。
- 国内主要鋼材メーカーによる製造
- 鋼材商社や町工場を経由した供給網
- 価格変動は原料相場に依存
8: SS400鋼材の産業への影響
8-1: 建設業における重要性
建築物や橋梁、土木構造物の主要部材としてSS400鋼材は欠かせません。強度と加工性のバランスが良いため、構造物の骨組みとして広く採用されています。特にコスト削減が求められる大規模工事では重宝される材料です。
- 骨組みや梁・柱材としての活用
- コスト効率の良い大量供給が可能
- 耐震設計や補修工事でも重要
8-2: 自動車産業との関係
自動車のフレームやシャシー部品においてもSS400鋼材は利用されています。軽量化や高強度化のために高機能鋼材への移行が進む中で、低コスト部品や補修用途では依然として需要があります。町工場での切削加工や溶接部品製造にも欠かせません。
- シャシーやボディ構造の一部に使用
- 補修・交換部品としての役割
- 加工しやすさが町工場での加工を支える
8-3: 町工場の役割と使用例
多くの中小製造業、町工場では、SS400鋼材は加工性の良さとコスト面でのメリットから主力材料です。機械部品の試作や小ロット生産に適しており、地場産業の基盤として重要な役割を果たしています。
- 小規模生産や特注部品の材料選択肢
- 汎用性の高さで多様な製品に対応
- 地域産業の技術力支援
9: 今後のSS400鋼材の展望
9-1: 技術革新とその影響
近年、鋼材の高機能化が進み、耐腐食性や強度を向上させた新材料の開発が活発です。一方でSS400は標準構造用鋼として安定した需要が続く見込みです。加工技術の進歩や表面処理技術の改善により、性能向上の余地もあります。
- 新素材との共存と棲み分けが進む
- 表面処理技術による耐久性強化
- 加工精度向上で用途拡大の可能性
9-2: 持続可能性の観点から
環境負荷低減が求められる中、リサイクル性に優れるSS400は持続可能な資源利用の観点でも有利です。鉄鋼業界全体でCO2排出削減の取り組みが進む中、エネルギー効率の良い生産技術の導入が期待されています。
- 高リサイクル率で資源循環に貢献
- 省エネルギー製造プロセスの導入
- 環境対応型鋼材としての位置づけ強化
9-3: 今後の市場動向
インフラ整備や製造業の復興に伴い、SS400鋼材の需要は安定的に推移すると予想されます。一方で海外からの高機能鋼材の流入や新素材の台頭で競争は激化します。コストと品質の両立を図りながら、国内生産の強みを活かす戦略が求められます。
- 安定的な国内需要の維持
- 国際競争力強化の必要性
- 新素材や複合材料との競合環境
海水環境でのSUS316Lの耐久性解析
1: 海水環境におけるSUS316Lの耐久性
1-1: SUS316Lの基本特性と構成
SUS316Lは低炭素タイプのオーステナイト系ステンレス鋼で、クロム(Cr)約16-18%、ニッケル(Ni)約10-14%、モリブデン(Mo)約2-3%を含有します。モリブデン添加により耐孔食性・耐局部腐食性が向上し、低炭素化により耐粒界腐食性も高められています。非磁性で、優れた靭性と耐熱性も併せ持ちます。
1-2: SUS316LとSUS304の違い
SUS304は一般的な18-8ステンレス鋼であるのに対し、SUS316Lはモリブデンを含むことで耐海水性や化学薬品への耐食性が大きく向上しています。特に海水や塩分の多い環境では、SUS304に比べてSUS316Lのほうが孔食や割れ腐食の発生が格段に抑えられます。加えて、SUS316Lは低炭素であるため、溶接後の耐食性も優れています。
1-3: 耐腐食性の重要性について
海水環境は塩分や酸素の存在により、金属の腐食を促進します。ステンレス鋼の耐腐食性は製品寿命や安全性を左右するため非常に重要です。特に海洋構造物や船舶部品、化学プラントの配管では、耐腐食性が不十分だと破損・漏れが発生し、重大な事故につながります。
1-4: 海水腐食のメカニズム
海水中の塩化物イオン(Cl⁻)はステンレスの保護膜を局所的に破壊し、孔食(ピッティング)や割れ腐食を引き起こします。これにより微細な穴や亀裂が形成され、腐食が進行。温度上昇や流速の変化も腐食速度に影響します。モリブデンの添加はこの局部腐食を抑制する役割を果たします。
2: SUS316Lの耐海水性
2-1: SUS316Lの海水中での強度
SUS316Lは海水中でも優れた引張強度と耐食性を発揮します。引張強度は約485〜620 N/mm²、耐食性を維持しながら機械的強度が高いため、過酷な海洋環境での構造材として適しています。海水による腐食が抑えられることで、応力腐食割れのリスクも低減されます。
2-2: 塩分濃度と耐腐食性の関係
海水の塩分濃度が高くなると、塩化物イオンの攻撃性が増し腐食リスクは高まります。SUS316Lは一般海水の塩分濃度(約3.5%)下で優れた耐食性を示しますが、濃縮された塩水や干潮部など塩分が高い環境では局所腐食が発生する場合もあります。適切な表面処理やメンテナンスが重要です。
2-3: 摩耗と劣化の影響
海洋環境下では摩耗や生物付着(バイオファウリング)も劣化を加速します。表面に傷が入ると保護膜が損傷し、腐食進行が促進されるため、摩耗耐性のある加工やコーティングが推奨されます。定期的な洗浄やメンテナンスで長期的な耐久性を維持します。
3: 加工性と適用例
3-1: SUS316Lの加工技術
SUS316Lはオーステナイト系のため加工硬化しやすく、切削や成形時には工具の摩耗に注意が必要です。冷間加工や溶接に対しても低炭素であるため割れにくく、成形性・溶接性は良好です。表面仕上げにはバフ研磨や電解研磨が用いられ、耐食性の向上に寄与します。
3-2: 耐食用の部品選び
SUS316Lは配管、バルブ、ポンプ部品、熱交換器など耐食性が要求される部品に最適です。海水の浸食を受ける船舶の舵、スクリュー部品や海洋プラットフォームの構造材としても広く利用されています。用途に応じて熱処理や表面処理が選択されます。
3-3: 医療機器や船舶での使用例
医療機器分野では生体適合性に優れたSUS316Lが器具やインプラント材料として活用されます。船舶や海洋構造物では耐海水性と機械的強度の両面からSUS316Lが主要材料となり、長期的な安全性と耐久性を支えています。
4: SUS316Lのメンテナンス方法
4-1: 長期的な維持管理のポイント
SUS316Lの長期耐久性を保つためには、定期的な点検と清掃が重要です。海水環境下では塩分や汚れが表面に蓄積しやすいため、これを放置すると局部腐食の原因となります。高圧洗浄やブラッシングで付着物を除去し、表面の保護膜を維持することが効果的です。また、微細なひび割れや変色がないかを定期的に確認し、早期発見・対処を心がけます。
4-2: 効果的な防食方法
防食には適切な表面処理が有効です。電解研磨により表面を滑らかにし、酸化被膜の均一性を高めることで耐食性が向上します。また、亜鉛やポリマー系のコーティングは物理的なバリアを形成し、塩化物イオンの侵入を防ぎます。環境に応じて陰極防食法(カソード保護)を併用するケースもあります。メンテナンス計画に沿った定期的な防食処理が耐久性の鍵となります。
5: 耐久性評価の手法
5-1: 腐食試験の種類と方法
SUS316Lの耐腐食性は様々な試験により評価されます。代表的な試験には塩水噴霧試験(SST)、孔食電位測定、割れ腐食耐性試験(SCC試験)があります。これらは実際の海水環境を模擬し、材料の劣化速度や腐食形態を確認します。試験条件や期間は用途により設定され、結果は材料選定や設計に反映されます。
5-2: 性能評価の基準
耐久性評価にはJISやASTM規格に準じた基準が用いられます。例えば、塩水噴霧試験における腐食の進行度や孔食電位の閾値が性能指標となります。これらの基準は設計段階での安全マージン設定や製品保証に活用され、SUS316Lの海水用途適合性を客観的に示します。
5-3: 実地試験の事例
実際の海洋環境に設置したサンプルを長期間観察する実地試験も重要です。温度変化、潮流、生物付着など複合的な要因による劣化を把握でき、実運用条件下での性能を評価可能です。これらのデータは設計改善や新材料開発のフィードバックに用いられます。
6: SUS316Lのコストと選択
6-1: 価格差の要因
SUS316LはSUS304に比べてモリブデン含有量が高いため、原材料コストが増加します。さらに、加工難易度の高さや熱処理工程の違いもコストに影響します。加えて、市場の需給バランスや為替変動も価格差に寄与します。これらを踏まえたコスト評価が重要です。
6-2: 選び方のポイント
材料選定時は耐食性、強度、加工性、コストのバランスを検討します。海水や化学薬品に晒される環境ではSUS316Lの優れた耐腐食性が大きなメリットとなる一方、予算や使用条件によってはSUS304や他の合金も選択肢になります。用途に応じて性能要求を明確にすることが選定の鍵です。
6-3: 長期間のコスト分析
初期コストだけでなく、メンテナンス頻度や寿命、交換コストを含めたライフサイクルコスト(LCC)での評価が求められます。SUS316Lは高耐食性によりメンテナンスや交換が少なく済むため、長期的にはコストパフォーマンスが高い場合が多いです。全体コストの最適化を目指すことが重要です。
7: 海洋環境と腐食性
7-1: 海洋環境の特徴
海洋環境は高い塩分濃度、湿度、温度変動、波や潮流による機械的ストレス、紫外線照射、さらに生物の付着(バイオファウリング)など、多様な腐食促進要因が複合的に存在します。特に塩化物イオンの濃度が高いため、金属材料は局部的な孔食や割れ腐食を受けやすく、耐食性が非常に重要となります。さらに、酸素濃度や水流の変動により腐食速度が変化し、環境の過酷さが耐久性に大きく影響します。
7-2: 関連業界での使用事例
海洋構造物、船舶、石油・ガスプラント、海水淡水化装置などの業界でSUS316Lは広く使用されています。特に海水ポンプの部品、配管、熱交換器など、海水に直接接触する設備において耐腐食性と機械的強度を両立する材料として評価されています。さらに、医療や食品加工分野でも衛生的かつ耐食性に優れる素材として採用例が増えています。
8: 新技術と今後の展望
8-1: 耐食性向上のための研究
近年ではナノコーティング技術や表面改質技術が進展し、SUS316Lの表面に高耐食性の薄膜を形成する研究が活発に行われています。また、耐腐食性を高めるための微細組織制御や合金設計の最適化も進んでおり、環境負荷の少ない新しい耐食処理技術も模索されています。これにより、従来よりも過酷な海洋環境下での使用寿命延長が期待されています。
8-2: 新素材の可能性
SUS316Lに代わる新素材として、高耐食性を持つ高エントロピー合金やチタン合金、耐海水性の高い複合材料などの開発が進められています。これらは軽量化や耐熱性の向上も図られており、今後の海洋産業のニーズに応える可能性があります。一方で、コストや加工性の課題も存在し、用途に応じた使い分けが重要となります。
9: まとめと結論
9-1: SUS316L選択の理由
SUS316Lは海水環境における耐孔食性・耐割れ腐食性に優れ、機械的強度も高いため、海洋構造物や船舶、化学設備の主要材料として最適です。低炭素設計により溶接後の耐食性も保持し、医療分野などの特殊用途でも高い信頼性を誇ります。長期的な耐久性と信頼性から、多くの業界で第一選択として採用されています。
9-2: 今後の課題と展望
一方で、より過酷な海洋環境や長期使用を想定したさらなる耐食性強化が求められており、新技術や新素材の研究開発が重要課題です。コスト面や環境負荷の低減も含め、持続可能な材料選択が今後のテーマとなります。SUS316Lを基盤にしつつ、新素材や表面改質技術を組み合わせることで、より高性能かつ経済的なソリューションが期待されます。
引張強度による材料強度の基準
1: 引張強度と材料強度の基準
1-1: 引張許容応力とは
引張許容応力とは、材料が引っ張り応力に耐えられる最大の応力であり、安全に使用できる限界値を示します。通常は材料の降伏強度や引張強度に安全率をかけて求められ、設計時の安全基準として重要な指標です。
1-2: 引張強度の計算例
引張強度(σ_t)は試験片の最大荷重(F_max)を断面積(A)で割ることで求められます。
- 式:σ_t = F_max / A
- 例:最大荷重 10,000N、断面積 50mm²の場合
→ σ_t = 10,000N / 50mm² = 200 N/mm²
この値は材料の耐力を示す基本的な指標です。
1-3: 引張強度の目安と一覧
代表的な材料の引張強度の目安は以下の通りです。
- SUS304ステンレス鋼: 約520〜750 N/mm²
- 一般構造用鋼(SS400): 約400〜510 N/mm²
- アルミ合金(A5052): 約200〜310 N/mm²
用途に応じて強度特性を選定することが重要です。
1-4: 引張強度の応力とひずみ
引張試験において、応力-ひずみ曲線は材料の弾性領域、降伏点、塑性変形域を示します。引張強度はこの曲線上の最大応力点で、ひずみは材料がどれだけ伸びたかを示す重要な変形指標です。
2: 降伏応力度とその重要性
2-1: 降伏応力度の定義と基準
降伏応力度とは、材料が塑性変形を始める最小の応力を指します。これを超えると永久変形が生じるため、設計時には降伏応力度を安全限界として考慮します。
2-2: 降伏応力度の計算方法
降伏応力度(σ_y)は、試験片に荷重を加えた際に初めて明確な塑性変形が見られる応力値として測定されます。計算式は引張強度同様に
- σ_y = 降伏荷重 / 試験断面積
で求められます。
2-3: 降伏応力度と安全率の関係
安全設計では、降伏応力度に安全率をかけて「許容応力」とし、これを超えないように構造物を設計します。安全率は使用条件やリスクに応じて1.2〜3.0の範囲で設定されることが多いです。
3: 安全率の考慮
3-1: 安全率の定義と必要性
安全率とは、設計強度と実際にかかる応力の比率であり、不確定要素や製造誤差、荷重変動を考慮し安全側に設計するための係数です。これにより事故や破損のリスクを低減します。
3-2: 設計における安全率の計算例
例えば、材料の降伏応力度が250 N/mm²、安全率を2とした場合の許容応力は
- 許容応力 = 250 / 2 = 125 N/mm²
設計応力がこれを超えないように部材設計を行います。
3-3: 安全率を考慮した強度設計
強度設計では、材料強度のばらつきや使用環境の変動を考慮し、安全率を適切に設定することが必須です。過剰な安全率はコスト増加、過小な設定は安全性低下を招くため、バランスが重要となります。
4: 材料の種類とその強度特性
4-1: 鋼材の引張強度と許容応力
鋼材は建築や機械部品に広く使われ、その引張強度は種類によって大きく異なります。一般的な構造用鋼材の引張強度は約400〜700 N/mm²で、安全に使用できる許容応力は引張強度や降伏応力度に安全率をかけて設定されます。高強度鋼材では引張強度が1000 N/mm²を超えるものもあります。
4-2: コンクリートにおける引張強度
コンクリートは圧縮強度は高いものの、引張強度は比較的低く、一般に圧縮強度の約10%程度です。引張強度はおよそ2〜5 N/mm²であり、引張力に対しては補強材(鉄筋など)を用いて強度を補うのが一般的です。
4-3: リベットや部材の強度特性
リベットやボルトなどの締結部材も引張強度が重要です。これらは材質や形状により異なり、締結部の設計ではせん断強度とともに引張強度を考慮します。特に疲労や応力集中に注意が必要です。
5: 引張強度に対する疲労と破壊
5-1: 疲労強度の基準と計算
疲労強度とは、繰り返し応力に対する材料の耐久力を示します。疲労限度以下の応力であれば材料は理論上永久に耐えられますが、実際には応力の大きさや繰り返し回数により寿命が変動します。疲労強度はS-N曲線(応力-寿命曲線)を用いて評価されます。
5-2: 破壊のメカニズムと計算条件
引張強度を超えると材料は破断しますが、疲労破壊は微小なひび割れが進展し破壊に至る過程です。破壊力学の理論により、ひび割れの成長速度や破壊応力を計算し、安全設計に反映させます。
5-3: 短期と長期の強度の違い
短期的な引張強度は最大荷重に対する耐力ですが、長期的には疲労や環境劣化により強度が低下します。長期間の使用を想定した設計では、これらの影響を加味した許容応力設定が重要となります。
融点の高いSUS304ステンレス鋼の特性とは?
1: SUS304HPの特性と耐熱温度
1-1: SUS304HPとは?その材料特性
SUS304HPとは、オーステナイト系ステンレス鋼「SUS304」に高純度化処理を施したグレードです。主に半導体・真空装置・電子部品製造分野で利用されます。
- 不純物を極力低減し、脱炭素・脱硫・脱酸を徹底
- 高純度化により、優れた耐食性・低アウトガス性能を実現
- 高温環境下でも安定した機械的特性を保持
通常のSUS304よりも金属組織が安定しており、粒界腐食や析出反応を起こしにくいのが特徴です。
1-2: 融点の詳細と耐熱性の評価
SUS304HPの融点は約1400〜1450℃ですが、実用的な耐熱温度は約800〜900℃程度が目安です。
- 650℃までは機械的強度や耐食性の変化が少ない
- 800℃を超えると炭化物の析出や酸化皮膜の劣化が懸念される
- 真空環境では酸化の進行が抑えられるため、さらに高温域での利用が可能
そのため、半導体製造装置などの真空加熱部材において重用されています。
1-3: SUS304HPの用途と実用性
SUS304HPは、以下のような分野・製品で使用されています。
- 半導体製造装置の炉内部品(ヒーターカバー、フレーム)
- 真空チャンバー・真空容器
- クリーンルーム向け耐熱部品
- 高純度ガス供給システムの配管や継手
これらの用途では、アウトガスの少なさ、耐酸化性、精密加工適性が要求されるため、SUS304HPの特性が最大限に活かされます。
1-4: 他のステンレス鋼との比較
鋼種 | 耐熱温度(目安) | 特徴 |
---|---|---|
SUS304 | 約800℃ | 一般的な耐熱・耐食性 |
SUS304L | 約800℃ | 低炭素で溶接後の耐食性向上 |
SUS304HP | 約850〜900℃ | 高純度で真空・高温に対応、低アウトガス |
SUS316L | 約850℃ | 耐塩素性と耐食性に優れる |
SUS310S | 約1100℃ | 高温構造部品向け、Ni・Cr高含有 |
SUS304HPはSUS304の上位互換とも言える特性を持ち、特に電子・精密分野で優位性を発揮します。
1-5: SUS304HPの化学成分と影響
SUS304HPは、以下のように不純物(C, S, Pなど)を極限まで減らした組成を特徴とします。
- 炭素(C): ≦ 0.015%(304より低い)
- 硫黄(S): ≦ 0.005%(脱硫処理済)
- 酸素(O)・窒素(N): 限界まで低減
- クロム(Cr)・ニッケル(Ni)は304とほぼ同等
この成分制御により、高温での組織安定性、耐食性、脱ガス性が向上し、高真空やクリーン環境での使用に最適です。
2: ステンレス鋼の加熱と冷却管理
2-1: 加工と熱処理の理論
ステンレス鋼は、オーステナイト組織を維持する熱処理が重要です。
- 溶体化熱処理(1050℃前後)で組織を均一化
- 焼鈍処理により応力除去・靭性回復
- 急冷によって炭化物の析出を防止し、耐食性を維持
高純度鋼であるSUS304HPでは、熱処理による変質を極力抑えることが可能です。
2-2: 高温環境での耐久性と安全性
ステンレス鋼の耐熱性を保つには、加熱・冷却のサイクル管理が重要です。
- 熱疲労によるクラックの進行に注意
- 熱膨張と収縮を繰り返す構造部材にはスリット設計や応力拡散処理が必要
- 繰返し昇温・冷却下で使用される場合は、材質選定に加えて設計上の配慮が求められます
特にSUS304HPのような高純度材は、熱変形や酸化のリスクを大幅に低減できます。
2-3: オーステナイト鋼の特性
オーステナイト系ステンレスは、常温でもオーステナイト組織を維持する非磁性材料です。
- 高温でも強度と延性を両立
- 軽度な冷間加工で加工硬化しやすい
- 熱処理後の安定性が高く、耐食性にも優れる
SUS304HPは、純度の高いオーステナイト組織を安定維持することで、信頼性の高い部材となります。
2-4: 低温条件下での挙動
ステンレス鋼は、低温下でも脆化しにくい特性があります。
- オーステナイト系は-196℃でも靭性を保つ(極低温用途にも対応)
- 高純度鋼は低温でも内部応力の集中を回避
- 冷却後の結露・腐食対策には表面処理や湿度管理が重要
真空装置や液体窒素関連の配管材など、SUS304HPは低温・高温の両環境に対応可能な高性能材です。
3: SUS304HPの加工技術
3-1: 切削とフライス加工の注意点
SUS304HPの切削加工では、以下の点に留意する必要があります。
- 高純度ゆえに被削性がやや低い(工具摩耗に注意)
- 切削油は高温対応・クリーン対応型を使用
- 微細加工時にはバリの発生と取り扱いに注意
特に精密部品やシール面などでは、工具選定と加工条件の最適化が重要です。
3-2: 溶接と成形の方法
SUS304HPは一般的にTIG溶接やレーザー溶接が適しています。
- 溶接熱影響を抑えるため入熱管理が必須
- 溶接後は酸洗・パッシベーション処理を推奨
- 成形加工(曲げ・絞り)時は低速での加工と割れ対策が必要
精密溶接が求められる真空容器では、ガス漏れゼロの高精度施工が求められます。
3-3: 耐熱容器の製作技術
耐熱容器の製作においては、以下の加工ポイントが重要です。
- 肉厚均一な溶接と機械加工で熱変形を抑制
- 内部は鏡面研磨または電解研磨で脱ガス低減
- 構造部は熱応力に耐える設計(リブ・逃げ構造など)
SUS304HPは熱膨張率が安定し、耐熱変形に強いため、加熱装置のケーシングやトレイに多用されています。
3-4: 金属加工業界での利用事例
実際の利用例として、以下が挙げられます。
- 半導体装置メーカーにおける真空治具・搬送台
- 表面処理装置の高温ガス導入パーツ
- 医療分析装置の熱制御部材
- クリーン環境向けの加熱処理トレイや炉内治具
加工性の高さと耐熱・脱ガス性能のバランスにより、高付加価値な精密部品製造に欠かせない材料となっています。
4: SUS304の選定理由と影響
4-1: 選定基準と評価項目
SUS304はオーステナイト系ステンレス鋼の中でも汎用性が高く、機械部品から食品機器、建材に至るまで幅広く利用されています。選定においては以下の評価項目が重視されます。
- 耐食性(錆びにくさ)
- 機械的強度(引張強度・降伏強度)
- 成形性・溶接性
- 経済性(コストパフォーマンス)
これらの基準が高水準でバランスされていることから、多くの現場でSUS304が第一選択とされています。
4-2: 材料の強度と性能の関係
SUS304は冷間加工によって強度を高めることができるため、設計条件に応じた調整が可能です。強度性能には以下の特徴があります。
- 引張強さ:約520N/mm²
- 耐熱温度:使用限界温度は約870℃(空気中)
このような強度は、構造物としての信頼性を高めると同時に、加工後の精度維持にも寄与します。
4-3: ランク付けと業界ニーズ
業界では、使用環境や求められる性能に応じてSUS304を他の材料と比較評価し、適切なランクを設定します。
- 食品・医療分野:耐食性重視 → SUS316Lが選ばれることも
- 汎用機械部品:コストと加工性重視 → SUS304が最適
ランク付けは調達コストやメンテナンス性にも影響し、製品全体のライフサイクル設計に密接に関係します。
4-4: 環境要因が与える影響
SUS304は中性環境下では高い耐食性を発揮しますが、以下のような環境では選定に注意が必要です。
- 高塩分環境(例:海水周辺) → 応力腐食割れの可能性
- 強酸・強アルカリ条件 → 化学的腐食の進行
そのため、用途に応じてSUS304HPやモリブデン添加型のステンレス(例:SUS316)への切替が検討されます。
5: SUS304HPの安全性と性能維持
5-1: 耐腐食性と化学耐性の重要性
SUS304HPは標準のSUS304よりも微細構造の均一性が高く、特に以下の条件下で信頼性が向上します。
- クリーン環境
- 化学薬品との接触
- 長期間の高湿度環境
腐食や酸化を抑制する成分バランスが最適化されており、化学プラントや医薬分野での使用にも適しています。
5-2: 使用温度範囲と性能低下リスク
SUS304HPは高温・低温ともに安定した性能を発揮しますが、次の点に注意が必要です。
- 連続使用可能温度:最大870〜900℃(空気中)
- 700℃前後での析出硬化や結晶粒成長による強度低下リスク
熱サイクルが繰り返される設備では、温度管理と断熱対策が性能維持の鍵を握ります。
5-3: 安全な取り扱いと管理方法
SUS304HPの取り扱いには、以下のような管理対策が求められます。
- 切削加工時の発熱抑制
- 溶接部の酸化防止(アルゴンシールドなど)
- 搬送・保管時の異種金属接触防止
これにより腐食や表面変質を防ぎ、長期的な安全性が確保されます。
5-4: 次世代材料との比較と可能性
SUS304HPは現在も多くの産業で主流ですが、次のような次世代材料が検討されつつあります。
- SUS316L:耐酸性の向上
- 高窒素ステンレス:強度・耐孔食性の向上
- 二相ステンレス(SUS329J4Lなど):高強度と高耐食性の両立
とはいえ、コスト・汎用性・加工性のバランスにおいて、SUS304HPは依然として有力な選択肢であることに変わりありません。
ステンレス鋼の耐熱性と限界について知ろう
Contents1: ステンレス鋼の耐熱性の基本
1-1: ステンレス鋼の種類と特性
ステンレス鋼は、主に鉄にクロムを加えた合金で、高い耐食性と強度を持つ素材です。種類は大きく分けて以下のように分類されます。
- オーステナイト系(例:SUS304, SUS316L)
非磁性で高耐食性。常温での延性に優れ、耐熱性も高め。 - フェライト系(例:SUS430)
磁性があり、価格が比較的安価。耐食性はオーステナイト系よりやや劣るが、熱膨張が小さく耐熱形状安定性に優れる。 - マルテンサイト系(例:SUS410)
高硬度を持ち、耐摩耗性に優れるが、耐食性は低め。
1-2: 耐熱性とは何か?
耐熱性とは、材料が高温環境下でも物理的性質(強度、硬度、寸法安定性など)や化学的性質(酸化抵抗性など)を維持できる能力を指します。特にステンレス鋼では、酸化皮膜の安定性と熱膨張への耐性が重要な評価指標となります。
1-3: 耐熱温度の定義
耐熱温度とは、「特定の物理的性質が大きく変化せずに使用できる上限温度」のことです。一般にステンレス鋼の耐熱温度は約500〜1100℃の範囲で、材質によって異なります。たとえば、SUS310は約1100℃までの耐熱性を持つ一方、SUS304は800℃前後が上限となります。
2: 材料としてのステンレス鋼の理解
2-1: SUS310とSUS316Lの比較
特性 | SUS310 | SUS316L |
---|---|---|
耐熱性 | 非常に高い(~1100℃) | 中程度(~600〜800℃) |
耐食性 | 優れている | 非常に優れている |
用途例 | 工業炉、排気装置 | 医療器具、食品機械 |
SUS310は耐熱性に特化した素材で、連続使用において酸化スケールの形成を抑える効果があります。対してSUS316Lは低炭素仕様で、応力腐食割れに強く、耐食性が求められる分野で活躍します。
2-2: ステンレススチールの主要成分
ステンレス鋼は主に以下の元素で構成されています。
- クロム(Cr):耐食性・耐熱性の基盤となる。
- ニッケル(Ni):オーステナイト相を安定化し、靱性と耐熱性を向上。
- モリブデン(Mo):耐酸性と耐孔食性を強化(特にSUS316系に添加)。
- 炭素(C):強度に寄与するが、過剰だと耐食性を損なう。
2-3: オーステナイト系とフェライト系の違い
- オーステナイト系(例:SUS304, SUS316L)
- 常温で安定なγ鉄(オーステナイト)構造
- 非磁性で耐食性・溶接性に優れる
- 耐熱性も高く、熱間強度が持続
- フェライト系(例:SUS430)
- 安定なα鉄(フェライト)構造
- 磁性あり、熱膨張が少なく形状安定性良好
- 高温でのクリープ強度はやや劣る
3: ステンレス鋼の耐熱性に影響する要因
3-1: 使用環境が及ぼす影響
高温状態に加え、酸素濃度、腐食性ガス、湿度などの外的因子は、ステンレス鋼の酸化や表面劣化を加速させます。特に硫化水素や塩素ガスは、ステンレスでも腐食を進行させるため、材料選定時には注意が必要です。
3-2: 長期間使用による性能の低下
高温環境で長期間使用されると、ステンレス鋼内部の金属組織に変化が生じ、析出硬化物の成長やカーバイドの析出が発生しやすくなります。これにより、強度低下や粒界腐食などの劣化現象が進行します。
3-3: 温度変化による影響
急激な温度変化(熱衝撃)は、金属組織に内部応力を生み、割れや歪みの原因となります。熱膨張係数の大きな材料は特に変形の影響を受けやすく、繰り返しの加熱冷却サイクルによって、材料疲労が進行することもあります。
4: 耐熱性が求められる分野と用途
4-1: 高温環境でのステンレス鋼の使用例
ステンレス鋼は、以下のような高温環境で幅広く使用されています。
- 工業炉部品(例:SUS310)
高温にさらされる熱処理炉や焼成炉の内部構造材に使用。 - 排気システム部品(例:SUS409)
自動車の排ガス系、ボイラーの煙道などで、熱と腐食の両方に対応。 - 熱交換器(例:SUS304, SUS316L)
発電所や化学プラントで、熱を効率的に移動・保持するために採用。
高温と同時に腐食性や機械的強度も求められるため、耐熱性だけでなく「総合的な性能」が評価されます。
4-2: 食品加工における耐熱性の重要性
食品加工分野では、以下のような観点からステンレス鋼が重宝されています。
- 高温での殺菌・加熱処理
オートクレーブや蒸気殺菌装置で使用される容器や配管には、耐熱性と耐食性が必須。 - 酸性食品への耐性
酢やトマト、柑橘類などによる酸性腐食に強いステンレス鋼(例:SUS316L)が使用される。 - 清掃性と衛生基準の両立
高温洗浄や蒸気滅菌を繰り返す環境でも、表面が劣化しにくい必要がある。
4-3: 医療機器における要求される性能
医療機器においては以下の性能が求められ、耐熱性の高いステンレス鋼が使用されます。
- 高圧蒸気滅菌(オートクレーブ)への耐性
器具の繰り返し滅菌処理に耐えられる必要あり(SUS316Lが標準)。 - 腐食性薬品・洗浄剤への耐久性
消毒剤や血液成分に長期的に接しても表面劣化が少ない材質が必要。 - 寸法精度の維持
高温・高圧下でも、構造が歪まない素材選定が不可欠。
5: ステンレス鋼の耐熱性を維持する方法
5-1: 定期的メンテナンスの重要性
高温環境下で使用されるステンレス鋼は、以下のような理由から定期的な点検・メンテナンスが欠かせません。
- 酸化スケールの付着による熱伝導性低下
- 高温腐食や金属疲労による微細なクラックの進行
- 材料表面の変質による性能劣化
適切な洗浄・再研磨・部品交換によって、性能劣化を防止し、安全な使用を持続できます。
5-2: 加工方法と耐熱性の関係
加工工程も耐熱性に影響を及ぼします。以下の点が重要です。
- 溶接部の熱影響による耐食性低下
→ 溶接後に酸洗いやパッシベーション処理を行うことで回復可能。 - 冷間加工の残留応力が割れの起点に
→ ストレスリリーフ焼鈍で内部応力を除去。 - 表面仕上げ粗さと酸化挙動の関係
→ 鏡面仕上げの方がスケール形成が抑制され、耐熱性が安定。
5-3: 耐熱性を向上させる材料選択
使用温度や環境に応じて、以下のようなステンレス鋼を選定することで耐熱性を最適化できます。
- 800℃以下:SUS304, SUS316L
- 1000℃前後:SUS310S
- 1150℃以上:ニッケル基超合金(例:Inconel)や耐熱鋼(例:SUH660)
素材選定時には、温度だけでなく、酸化性ガスの有無や連続使用時間も考慮する必要があります。
6: 耐熱性と安全性の関係
6-1: 高温での安全な使用について
ステンレス鋼を高温で使用する際には、以下の安全対策が不可欠です。
- 設計段階での熱膨張係数の考慮
- 応力腐食割れ(SCC)に対する防止策(材質選定と応力除去)
- 焼き付き防止のための表面処理や潤滑対策
高温化では、物理的破損だけでなく、化学的反応による劣化が事故要因になることもあります。
6-2: 耐熱性の評価基準
耐熱性は主に以下の評価指標で測定・比較されます。
- 耐酸化温度:表面酸化が急激に進行しない温度範囲
- クリープ強度:高温での長時間荷重による変形耐性
- 熱疲労耐性:繰り返しの加熱冷却による割れへの抵抗力
これらの指標を踏まえた材料選定と、使用環境への適合が重要です。
6-3: 耐腐食性と耐熱性のリンク
ステンレス鋼の耐熱性と耐腐食性は密接に関係しています。特に、酸化環境や水蒸気環境下では、以下のような傾向があります。
- クロムやアルミの酸化皮膜が耐熱性と耐食性の両方を支える
- 高温下での孔食・粒界腐食は、長期使用における信頼性に直結
- 耐熱性の高い材料ほど、同時に高い耐酸化性を持つ傾向あり
適切な設計・メンテナンスと素材選定を組み合わせることで、安全性・信頼性・長寿命化を実現できます。
7: ステンレス鋼の限界と課題
7-1: 耐熱限界を超えた場合のリスク
ステンレス鋼は優れた耐熱性を持つ一方で、使用限界温度を超えると急激に性能が低下します。
- 酸化皮膜の崩壊による腐食加速
- 結晶構造の変化(例:オーステナイト→フェライト)による機械的強度の低下
- クリープ破壊(高温で長時間荷重を受けることで変形・破断)
特に1000℃を超える環境では、ニッケル基合金や耐熱鋼などの「超耐熱材」への切り替えが必要になります。
7-2: 長期使用時の耐久性の問題
高温での長期使用は、以下のような経年劣化を引き起こす原因となります。
- 金属疲労:熱膨張・収縮の繰り返しによる亀裂形成
- 粒界酸化:結晶粒界から酸素が侵入し、内部から脆化
- クロム欠乏層の形成:耐食性が低下し、局部腐食が発生
これらの問題は、稼働停止や設備事故のリスクを高めるため、定期的な検査・更新が不可欠です。
7-3: ステンレス鋼の劣化プロセス
ステンレス鋼は以下のようなステップで劣化していきます。
- 表面に酸化スケールが形成される
- スケール下で金属組織に変化(脆化)
- 局部的な腐食や微細クラックの発生
- 繰り返しの熱応力でクラックが進展
- 応力集中部での破断や機能不全
高温使用では、これらの現象が加速されるため、使用温度と時間の管理が極めて重要です。
8: ステンレス鋼の選定と加工の考慮点
8-1: 選び方のポイント
耐熱性を求める環境では、下記の点を考慮して材料を選定することが推奨されます。
- 使用温度と連続使用時間
- 腐食環境の有無(酸性・塩素・高湿度)
- 機械的応力の有無(クリープ、熱疲労)
- 加工性とコストのバランス
例えば、食品・医療分野ではSUS316L、高温排気用途ではSUS310SやSUH系がよく用いられます。
8-2: 加工における注意点
ステンレス鋼の加工では、耐熱性に悪影響を及ぼさない加工法の選定が求められます。
- 溶接部の熱影響部(HAZ)での耐食性低下
- 表面の酸化やスケール付着による初期劣化
- 冷間加工による残留応力の蓄積
これらを防ぐために、溶接後の酸洗い・パッシベーション、ストレス除去焼鈍処理、精密研磨などが重要です。
8-3: 市場での製品比較
市場では、以下のようなスペックで製品が比較されています。
- 使用温度の上限
- 酸化スケールの形成速度
- 機械的強度(引張強度、クリープ強度)
- 価格と入手性(材料在庫・流通量)
ニッケル含有量が高い鋼種ほど高価であるため、コストと性能のバランスが選定の鍵となります。
9: ステンレス鋼の未来と進化
9-1: 新しい合金技術の展望
近年では、より高温環境に対応できる次世代ステンレス合金の研究が進んでいます。
- フェライト系高耐熱鋼(例:Fe-Cr-Al系)
→ クロムに加えアルミを含有し、酸化皮膜の耐久性向上。 - 析出硬化系ステンレス鋼(例:17-4PH)
→ 機械的強度と耐熱性を両立。 - 高Ni系ステンレス合金
→ オーステナイト安定性を保持しつつ、高温特性を強化。
これらの新素材は、航空・原子力・次世代エネルギー分野での活躍が期待されています。
9-2: 持続可能性に向けた取り組み
ステンレス鋼はリサイクル性が高く、環境負荷が低い材料として注目されています。
- 使用済みステンレスのリサイクル率は80%以上
- 製造時にCO₂排出量を抑える製鋼プロセスが開発中
- 長寿命化によって廃棄頻度の低下と資源の有効活用を実現
持続可能な製品開発の中核として、今後さらに利用が拡大すると予測されます。
9-3: 耐熱性に関する最新の研究動向
耐熱性に関する研究では、以下のテーマが注目されています。
- ナノ構造酸化皮膜による耐酸化性の向上
- 高温腐食に対する多層コーティング技術
- AIによる合金設計の自動化
- 3Dプリンティングによる複雑形状の耐熱部品製造
これらの技術革新は、従来のステンレス鋼の性能限界を突破する手段として、産業界から大きな期待を集めています。
SUS630の固溶化熱処理による特性向上の検証
1: SUS630の固溶化熱処理とは
1-1: 固溶化熱処理の概要
固溶化熱処理(Solution Treatment)は、金属内部の析出物を溶解させ均一な固溶体組織を得るための加熱処理です。
- 金属材料を高温で一定時間加熱し、その後急冷して析出物を溶解させる。
- 結果として組織が均質化し、機械的特性や耐食性が向上する。
- SUS630ではこの処理を通じて、析出硬化の前段階となる状態を作り出す。
1-2: SUS630の特徴
SUS630は析出硬化系マルテンサイト系ステンレス鋼であり、固溶化熱処理が性能向上に重要な役割を果たします。
- 高い強度と耐食性のバランスが特徴。
- 固溶化熱処理により、析出硬化前の均一な組織を形成。
- H900やH1025などの時効処理により最終的な硬度と強度を調整。
1-3: オーステナイト系ステンレス鋼との関係
- SUS630はマルテンサイト系ながら、固溶化熱処理中は一時的にオーステナイト相が形成される。
- オーステナイト相からマルテンサイト相への変態を利用して硬化する。
- 固溶化熱処理はこの相変態をコントロールし、組織の均質化と性能安定に寄与。
1-4: SUS630の化学成分と影響
主要成分は以下の通りで、各元素が熱処理性や機械的性質に影響を与えます。
- Cr (クロム):耐食性の向上と析出硬化の促進。
- Ni (ニッケル):オーステナイト形成と耐食性のバランス調整。
- Mo (モリブデン):耐孔食性の強化。
- Cu (銅):析出硬化の主因で、強度向上に大きく寄与。
- C (炭素):硬度や耐摩耗性を高めるが、多すぎると靭性低下。
2: SUS630の熱処理プロセス
2-1: 熱処理なしとの比較
- 未処理状態では硬度・強度が低く、耐食性も不十分。
- 固溶化熱処理により、均質な組織となり機械的特性が飛躍的に向上。
- さらに時効処理を施すことで最終的な性能を引き出せる。
2-2: H900およびH1025処理の特性
- H900処理(900°F=約482°Cでの時効処理)
- 高強度・高硬度だが、靭性はやや低め。
- H1025処理(1025°F=約552°Cでの時効処理)
- 強度はやや落ちるが、靭性や耐食性が向上。
- 用途に応じて処理温度を選択し、性能バランスを調整する。
2-3: 加熱と冷却の方法
- 固溶化熱処理は約980〜1038℃で加熱し、数十分保持。
- 急冷(通常は水冷)により析出物の再形成を防止し、均一な固溶体を保持。
- 急冷条件が不適切だと組織に不均一性や割れが生じることもあるため管理が重要。
2-4: 処理時間と温度の重要性
- 加熱時間が短すぎると析出物の溶解が不十分となり、性能低下。
- 過度な加熱は過晶粒化や酸化を引き起こすリスクがある。
- 温度と時間の最適バランスがSUS630の性能に直結。
3: SUS630の機械的性質向上
3-1: 硬度と硬さの変化
- 固溶化熱処理後の硬度は比較的低いが、後続の時効処理で大幅に硬度向上。
- H900処理で最大約50HRC程度の硬度に達し、高い耐摩耗性を実現。
3-2: 強度の向上と構造
- 固溶化により均一なマルテンサイト組織が形成され、析出硬化によって強度が飛躍的に向上。
- 強度向上により、構造部品や高荷重部品への適用が可能。
3-3: 加工性と耐熱性の改善
- 固溶化熱処理により加工硬化が抑制され、加工性が向上。
- 高温でも安定した機械的性質を保持し、耐熱環境でも使用可能。
3-4: 製品への適用例
- 航空機の構造部品
- 石油・ガス産業の耐圧容器
- 化学プラントの耐腐食性部品
- 食品機械の高強度・耐食部品
これらの製品は固溶化熱処理と時効処理による性能向上の恩恵を受けている。
4: SUS630の表面処理と性能
4-1: 表面処理の種類
SUS630は高強度・耐食性を持つが、さらなる性能向上のために多様な表面処理が施されます。主な表面処理は以下の通りです。
- 機械研磨(メカニカルポリッシュ)
- 表面の微細な凹凸を除去し、摩擦低減と美観向上を実現。
- 電解研磨
- 電解液中で金属表面を化学的に溶解除去し、平滑で光沢のある仕上げに。耐食性向上に寄与。
- ショットピーニング
- 微細な金属球を高速で表面に打ち付けて、圧縮残留応力を与え疲労強度を増加。
- 窒化処理
- 表面に硬い窒化層を形成し、耐摩耗性・耐腐食性を改善。
- クロムめっき
- 耐摩耗性、耐食性の大幅な向上。光沢を伴い装飾効果も。
4-2: 耐食性と機械的性質との関係
- SUS630は固溶化熱処理や時効処理で機械的強度を高めつつも、クロムやニッケル含有により耐食性も確保。
- 表面処理により耐食性が強化され、特に電解研磨は表面の不純物を除去し耐食性向上に効果的。
- ただし、硬度向上と耐食性のバランスは重要で、過度な硬化は割れやすくなる場合もあるため注意が必要。
4-3: 磁性と特性に与える影響
- SUS630は析出硬化系マルテンサイト系であり、強磁性を示す。
- 磁性は溶接や加工による相変態、熱処理条件によって変化。
- 磁性の変化は磁気的特性を利用する用途(例:センサー部品)に影響を与えるが、機械的特性や耐食性には間接的な影響。
- 表面処理や熱処理で磁性を制御することも可能。
5: 実践事例と応用
5-1: 部品としての使用例
- 航空機エンジン部品(高温・高強度が必要)
- 化学装置のシャフトやバルブ部品(耐食性と耐摩耗性が求められる)
- 食品加工機械の刃物や治具(衛生的かつ耐久性重視)
- 石油掘削装置の部品(過酷環境下での耐久性)
5-2: 産業への適用
- 航空宇宙産業:軽量かつ高強度で安全性が求められる部品に最適。
- 化学・石油産業:耐食性と強度を両立する素材として各種設備に使用。
- 食品加工:耐腐食性と清掃のしやすさから衛生管理に寄与。
- 自動車産業:高強度部品や耐摩耗部品として適用が進む。
5-3: 今後の技術展望
- 新しい表面処理技術(例えばナノコーティングやプラズマ処理)の導入による性能向上。
- 3Dプリンティング技術との組み合わせによる複雑形状の高性能部品製造。
- 環境負荷低減のためのエコフレンドリーな熱処理・表面処理プロセス開発。
- IoT・スマート工場に対応した材料管理と加工制御の高度化。
これらの動向により、SUS630の適用範囲はさらに広がり、高機能化が期待されている。
6: SUS630熱処理の比較と解析
6-1: 他材料との比較
- SUS630 vs SUS304
- SUS304はオーステナイト系で耐食性に優れるが、強度・硬度は低め。
- SUS630は析出硬化処理により高強度・高硬度を実現し、耐食性も維持。
- SUS630 vs SUS416(マルテンサイト系)
- SUS416は高硬度だが耐食性はSUS630に劣る。
- SUS630は耐食性と機械的強度のバランスが優れている。
- SUS630 vs 軽合金(アルミ・チタン合金)
- 軽量であるが耐摩耗性や耐熱性はSUS630に軍配。
- 高温強度が求められる環境ではSUS630が優位。
6-2: 異なる処理方法の効果
- 固溶化処理
- 合金元素を均一に溶解させることで基材強度を均一化し、析出硬化の土台を形成。
- 析出硬化(時効処理)
- 微細な析出物がマトリックス中に分散し、硬度と強度が大幅に向上。
- 処理温度・時間の違いにより、硬度・延性のバランスが調整可能。
- 焼戻し処理
- 余分な内部応力の解消と靭性向上を目的に実施。
- 適切な焼戻しにより割れにくさが改善される。
- 熱処理無しの場合
- 強度が低く、耐摩耗性・耐食性も限定的。熱処理が必須とされる。
6-3: 分析データと実績
- 硬度:固溶化処理後のSUS630は約30HRC、H900処理後は約45-50HRCまで向上。
- 引張強度:熱処理により約1000MPa超えが可能。
- 耐食性評価:電解研磨併用で塩水噴霧試験にて優れた耐食性を示す実績。
- 工業用途での実績:航空宇宙、化学、食品加工分野で多数の採用例があり、安定した性能が証明されている。
7: まとめと今後の研究課題
7-1: 特性向上の必要性
SUS630は強度・硬度と耐食性を両立した優れたステンレス鋼ですが、用途拡大のためにはさらなる耐熱性や耐摩耗性の向上が求められています。特に高温環境下での長期的な安定性や疲労強度の強化が課題です。
7-2: さらなる研究の必要性
- 新しい熱処理プロセスの開発
- 時効条件の最適化や複合処理技術の検討が期待される。
- 表面改質技術の進展
- ナノ構造化や複合コーティングによる耐摩耗・耐腐食性の強化。
- 材料組織の微細解析
- 先端解析技術を用いた析出物や相変態の詳細把握。
- 環境負荷低減技術
- 省エネルギー・低環境負荷の熱処理および加工技術の確立。
7-3: 産業界へのインパクト
SUS630の性能向上は、航空宇宙や自動車、化学、医療機器など多様な産業の高機能部品製造を支え、製品の信頼性向上と競争力強化に直結します。研究開発の進展は、これら産業の技術革新を加速させる重要な鍵となるでしょう。
SUS420J1の耐摩耗性と硬度の関係性
1: SUS420J1の硬度と耐摩耗性の関係性
1-1: SUS420J1の特性と硬度の重要性
SUS420J1はマルテンサイト系ステンレス鋼の一種で、特に硬度の高さが特徴です。硬度が高いほど耐摩耗性が向上し、刃物や工具、機械部品など摩耗が問題となる用途に適しています。また、耐腐食性もある程度保たれているため、バランスの良い性能が求められる場面で利用されています。
1-2: 硬度と耐摩耗性の関連するメカニズム
硬度は材料の塑性変形に対する抵抗力を示し、表面が摩耗しにくい特性と直結します。SUS420J1の硬度向上は主にマルテンサイト組織の形成と炭化物の分布によって実現され、これにより表面の摩擦や擦れに対する耐性が高まります。硬度が上がると材料の表面が傷つきにくく、耐摩耗性が向上する傾向があります。
1-3: 硬度が製品性能に与える影響
高硬度化によって耐摩耗性が向上すると、製品の寿命が延びるだけでなく、メンテナンス頻度も低減します。一方で、硬度が高すぎると脆くなり割れやすくなるリスクもあるため、用途に応じた適正な硬度調整が必要です。SUS420J1は焼入れや焼戻しを組み合わせることで硬度と靭性のバランスを最適化できます。
1-4: 耐摩耗性を向上させる方法
- 熱処理(焼入れ・焼戻し):適切な温度管理でマルテンサイト組織を形成し、硬度を高める。
- 表面処理:窒化処理や硬質クロムメッキなどの表面強化技術を用いる。
- 材料選定と設計:摩耗の激しい部位に硬度の高い材料を使用し、設計段階で摩擦を低減する工夫を行う。
2: SUS420J1の焼入れプロセス
2-1: 焼入れと硬度の関係
焼入れはSUS420J1の硬度を劇的に向上させる重要な熱処理工程です。高温で加熱後、急冷することでマルテンサイト組織を形成し、鋼の強度と硬度が増加します。焼入れにより硬度は通常200~400HVから最大で600HV以上に達することもあります。
2-2: 焼入れの適用温度とその影響
SUS420J1の焼入れ温度は通常約980~1050℃の範囲で行われます。高すぎる温度では過度の炭化物粗大化が起こり硬度低下の原因となる一方、低すぎるとマルテンサイト変態が不完全になり硬度が不足します。最適温度の設定が性能向上の鍵です。
2-3: 焼入れ後の硬度測定方法
硬度測定は主にロックウェル硬度計(HRC)やビッカース硬度計(HV)が用いられます。焼入れ後の硬度を正確に測定することで、適正な焼入れ処理が行われたかを評価し、製品の品質管理に役立てます。
2-4: 焼入れと焼戻しの重要性
焼入れ後の焼戻しは靭性を回復させるために不可欠です。焼戻しは通常150~250℃で行われ、硬度を若干低下させつつ、脆さを軽減し割れにくくする効果があります。この工程により、耐摩耗性と靭性のバランスが最適化されます。
3: SUS420J1の成分と機械的特性
3-1: SUS420J1の化学成分の理解
SUS420J1はクロム(Cr)約12~14%を含み、炭素(C)含有量は約0.15%以下です。クロムの添加により耐食性を確保し、炭素が硬度と強度に大きく寄与します。その他の元素としてマンガン(Mn)、シリコン(Si)、リン(P)、硫黄(S)なども微量含まれています。
3-2: マルテンサイト系ステンレス鋼との比較
SUS420J1は同じマルテンサイト系のSUS420J2やSUS440Cと比較すると、炭素含有量がやや低く、靭性が高い一方で最高硬度はやや劣ります。耐摩耗性は炭素量に依存するため、使用用途に応じて適切な鋼種選択が重要です。
3-3: 成分がもたらす硬度の変化
炭素含有量が増加すると硬度は上がりますが、同時に脆くなりやすい特性も強まります。クロムは硬化組織の安定化と耐食性向上に寄与し、適切なバランスで含有することが性能の決め手となります。
3-4: 異なる材質との固有の違い
SUS420J1はオーステナイト系のSUS304と比べて、熱処理により硬度調整が可能で耐摩耗性が高いのが特徴です。逆に耐食性はオーステナイト系に劣るため、腐食環境下では用途選定に注意が必要です。
4: SUS420J1の加工と用途
4-1: 加工工程における硬度の影響
SUS420J1は焼入れにより硬度が高まるため、加工工程では以下のような影響があります。
- 切削性の低下:硬度が増すことで工具摩耗が早まり、切削加工の効率が落ちる。
- 加工順序の工夫:加工は通常、焼入れ前の軟らかい状態で実施し、焼入れ後に研削などの仕上げ加工を行う。
- 工具選定の重要性:焼入れ後の加工にはダイヤモンド工具や超硬工具が推奨される。
- 残留応力の発生:加工による熱や力の影響で残留応力が発生し、後工程での割れや歪みの原因になることがある。
加工中はこれらを踏まえて適切な冷却や加工速度の管理が求められます。
4-2: SUS420J1の一般的な使用分野
SUS420J1は以下の分野で多く利用されており、硬度と耐摩耗性を活かした用途が中心です。
- 刃物・ナイフ類:切れ味が要求される刃物のブレード材料として。
- 軸受・シャフト部品:耐摩耗性と強度を求められる部品に適用。
- ポンプ・バルブ部品:摩擦が生じやすいシール部やバルブシートに用いられる。
- 歯車:摩耗に強く長寿命が求められるギア類。
- 医療機器・食品加工機械:耐食性を保ちつつ硬度が必要な部品。
これらの用途では、適切な熱処理を施すことで最適な性能を引き出しています。
4-3: 必要な硬度に基づく部品選定
部品の機能や使用条件により求められる硬度が異なるため、熱処理条件や材料選定が重要です。
- 高硬度(600HV以上):刃物類など耐摩耗性を最優先する部品。
- 中硬度(450〜600HV):適度な靭性と耐摩耗性を両立させる必要がある軸受部品など。
- 低硬度(400HV以下):加工性や耐衝撃性を重視する部品。
熱処理の温度や時間を調整し、必要な硬度をコントロールします。
4-4: 加工方法による性質の変化
加工方法は材料の表面特性や機械的性質に大きな影響を及ぼします。
- 研削加工:高い表面仕上げと寸法精度を実現。表面硬化や残留応力が発生しやすく、適切な熱処理が必要。
- 切削加工:加工硬化が少なく、後の熱処理効果を均一化できる。工具摩耗は焼入れ後より少ない。
- 熱処理後の仕上げ加工:寸法精度や表面品質を高めるために必須。
- 表面処理(例:窒化処理):耐摩耗性や耐食性の向上に効果的。
これらの加工特性を理解し、設計・製造に反映させることが求められます。
5: 結論と今後の展望
5-1: SUS420J1の適用可能性
SUS420J1は高硬度・耐摩耗性を必要とする用途に最適であり、以下の理由で広く採用されています。
- 耐摩耗性が高いため、長寿命部品の製造に適している。
- 焼入れにより硬度調整が可能で、多様な要求に対応できる。
- 耐食性も一定レベル確保されており、食品・医療分野でも使用される。
5-2: 業界の要求と発展の方向性
製造業界では、SUS420J1の性能向上に加え、コスト削減や環境負荷軽減の要求が強まっています。
- 加工性向上技術の開発:工具寿命延長や加工効率アップが求められる。
- 表面処理技術の進化:耐摩耗性や耐食性をさらに強化。
- 環境対応型材料・加工法の採用:有害物質削減やエネルギー効率改善。
これにより、SUS420J1の競争力強化が期待されます。
5-3: 今後の研究課題と解決策
今後の研究・開発に向けて、以下の課題が挙げられます。
- 硬度と靭性の両立:高硬度化による靭性低下を防ぐ新たな熱処理技術。
- 均一な硬度分布の実現:複雑形状部品の熱処理品質向上。
- 表面改質技術の多様化:ナノコーティングやプラズマ処理などの採用拡大。
- 加工工程の最適化:工具寿命延長や加工速度向上のための新技術開発。
これらの課題解決により、SUS420J1の性能・適用範囲がさらに拡大していくことが見込まれます。
SUS446の耐摩耗性を強化する表面処理事例
1: SUS446の耐摩耗性向上に役立つ表面処理技術
1-1: 耐摩耗性とは?
耐摩耗性とは、材料表面が摩擦や擦れによって削られたり、摩耗したりすることに対する抵抗力のことです。高い耐摩耗性は機械部品や工具の寿命延長に直結し、メンテナンスコストの低減や性能維持に重要な役割を果たします。
1-2: SUS446の特性と摩耗に対する影響
SUS446は高クロム系マルテンサイト系ステンレス鋼で、耐熱性と耐食性に優れる一方で、硬度も比較的高く耐摩耗性にも一定の強みを持ちます。しかし、過酷な摩擦環境下では表面が摩耗しやすいため、表面処理による強化が効果的です。
1-3: 耐摩耗性を高めるための表面処理方法
- 窒化処理:表面に硬化層を形成し、摩耗抵抗を大幅に向上。
- 硬質クロムメッキ:硬く耐摩耗性の高いクロム層を付加。
- PVDコーティング(物理蒸着):耐摩耗性の高い窒化チタンなどの薄膜を形成。
- フッ素樹脂コーティング:摩擦係数低減に有効だが耐摩耗性は限定的。
1-4: 耐摩耗性コーティングの選択肢と特徴
表面処理方法 | 特徴 | 耐摩耗性 | 耐食性 | 加工コスト | 適用例 |
---|---|---|---|---|---|
窒化処理 | 表面硬化、耐摩耗性・耐食性向上 | 高 | 高 | 中 | 軸受け、刃物 |
硬質クロムメッキ | 硬く摩耗に強い、耐食性や耐熱性も良好 | 高 | 中 | 高 | 油圧部品、金型 |
PVDコーティング | 薄膜形成で高硬度、耐摩耗性に優れる | 高 | 高 | 高 | 精密機械部品、切削工具 |
フッ素樹脂コーティング | 摩擦軽減に有効だが耐摩耗性はやや低い | 低〜中 | 中 | 低 | スライド部品、摩擦軽減用途 |
2: SUS446における表面処理の種類
2-1: 金属メッキ技術の詳細
硬質クロムメッキやニッケルメッキは、SUS446の表面に硬く耐久性のある金属層を形成し、摩耗や腐食から保護します。硬質クロムは特に高硬度と耐摩耗性が優れ、油圧部品などに多用されます。
2-2: フッ素樹脂コーティングのメリットとデメリット
フッ素樹脂は低摩擦係数と耐薬品性を持つため摩擦の軽減に適しますが、物理的な耐摩耗性は他の硬質コーティングに比べて劣ります。摩耗負荷の小さい部位や滑りを重視する用途に適しています。
2-3: 硬質塗装とその効果
硬質塗装は、特殊な樹脂やセラミック粒子を含む塗装で、硬度向上と耐摩耗性の改善に寄与します。耐食性も向上させることが可能ですが、厚塗りによる寸法変化に注意が必要です。
2-4: 電解処理のプロセスと特性
電解研磨や陽極酸化処理は表面の凹凸を平滑化し、耐食性を高めるとともに摩擦・摩耗を減少させます。特に腐食環境下での耐久性向上に効果的です。
3: SUS446耐摩耗性のための加工技術
3-1: 研磨処理の必要性と利点
表面の粗さを低減し、摩擦抵抗と摩耗を軽減します。研磨後に硬質コーティングを施すとコーティングの密着性が向上し、耐久性が増します。
3-2: ステンレス鋼適用時の考慮事項
SUS446は高硬度なため加工が難しい場合があります。加工時は工具選定、冷却管理、適切な加工速度を設定し、表面損傷を防ぐことが重要です。
3-3: 滑り特性を向上させる施策
フッ素樹脂コーティングや表面微細加工により、摩擦係数を低減させ滑り性を向上できます。これにより摩耗の進行を抑制可能です。
3-4: 耐久性を持続させるための維持管理
定期的な清掃、摩耗部の点検・再処理、適切な潤滑管理により、表面処理効果を長期間維持できます。特に過酷環境ではメンテナンスが重要です。
4: 実際の表面処理事例
4-1: 業界別の成功事例一覧
- 自動車産業:エンジン部品に硬質クロムメッキを施すことで摩耗耐性が向上し、部品寿命が30%延長。
- 化学プラント:耐腐食性を兼ね備えた窒化処理により、苛酷な環境下でも安定した運用を実現。
- 食品機械:フッ素樹脂コーティングで滑り性を高め、製造効率と清掃性の改善に成功。
- 建設機械:研磨とPVDコーティングの組み合わせで摩耗減少と耐久性向上を達成。
4-2: 加工プロセス改善による成果
表面処理前の精密研磨プロセスを最適化し、コーティング密着性を向上。結果として耐摩耗性能が20%アップし、再加工の頻度が大幅に減少。
4-3: 特定用途における施工例
油圧シリンダー部品に硬質クロムメッキを実施。摩耗が激しいシール接触面の耐久性が飛躍的に向上し、メンテナンスサイクルの延長を達成。
4-4: 製品美観向上の結果
電解研磨処理により表面光沢が増し、製品の外観品質が向上。これにより顧客満足度が高まり、ブランドイメージの強化にも寄与。
5: SUS446の耐摩耗性に関するFAQ
5-1: SUS446を選ぶ理由とは?
高温耐性と耐腐食性を備えつつ、適度な硬度で耐摩耗性も期待できるため、過酷環境での使用に最適です。
5-2: 表面処理選択時の注意点
使用環境の条件(温度、摩耗の種類、腐食性)を正確に把握し、それに適した処理方法を選ぶことが重要。処理後の厚みや寸法変化にも注意が必要です。
5-3: 耐摩耗性を最適化するためのコスト考慮
高機能な表面処理ほどコストが上がるため、必要な性能レベルとコストのバランスを考慮し、最適な方法を選択することが重要です。
5-4: 今後の表面処理技術のトレンド
- ナノコーティング技術:極薄層で高耐摩耗性を実現。
- 環境対応型処理:有害物質排出を抑えたエコプロセスの開発。
- 多機能コーティング:耐摩耗性に加え耐腐食性や摩擦低減を同時に追求する技術の進展。
ステンレス鋼SUS303の熱伝導率とは
1: SUS303の基本特性
1-1: SUS303とは何か
SUS303は、オーステナイト系ステンレス鋼の一種で、特に切削加工性を向上させるために硫黄(S)やセレン(Se)が添加された材料です。これにより加工時の工具摩耗が減少し、高精度な部品製造に適しています。一方で、耐食性はSUS304よりやや劣りますが、一般的な環境下では十分な耐食性能を持っています。
1-2: SUS303の成分表
SUS303の代表的な化学成分は以下の通りです。
- 炭素(C):0.15%以下
- クロム(Cr):17.0〜19.0%
- ニッケル(Ni):8.0〜10.0%
- 硫黄(S):0.15〜0.35%(切削性向上添加)
- セレン(Se):0.03〜0.08%(場合によって添加)
この特殊な成分構成により、切削加工時の性能が大きく向上します。
1-3: SUS303の規格と分類
SUS303はJIS規格において「耐食性および加工性に優れたオーステナイト系ステンレス鋼」として分類されています。ISOやASTM規格でも同様のグレードがあり、世界的に広く使用されています。
2: SUS303の線膨張係数
2-1: 線膨張係数とは
線膨張係数は、材料が温度変化によりどれだけ伸縮するかを示す物理的特性です。設計や加工において、温度変化による寸法変化を考慮するために重要な指標です。
2-2: SUS303の膨張特性
SUS303の線膨張係数は、約16.5×10⁻⁶/K(20〜100℃)とされ、一般的なオーステナイト系ステンレス鋼とほぼ同等の範囲です。これは、熱膨張による影響が比較的安定していることを意味し、機械部品や精密機器の設計に適しています。
3: SUS303の熱伝導率
3-1: SUS303の熱伝導率の重要性
熱伝導率は材料が熱を伝える能力を示し、加工時の熱管理や熱応力のコントロールに重要です。SUS303はオーステナイト系の中では中程度の熱伝導率を持ち、加工時の熱蓄積を抑える効果があります。
3-2: 比較:SUS303と他のステンレス鋼
SUS303の熱伝導率は約16 W/m·K(20℃付近)で、SUS304の約16〜20 W/m·Kと比較してやや低い傾向にあります。フェライト系やマルテンサイト系ステンレス鋼はこれより高い熱伝導率を示しますが、SUS303は切削加工性と耐食性のバランスが良いのが特徴です。
4: SUS303のヤング率
4-1: ヤング率とは
ヤング率(弾性係数)は、材料の弾性変形の硬さを示す物理量で、応力とひずみの比例関係の傾きを表します。構造物の設計や機械部品の耐久性評価において重要な指標であり、高いヤング率は剛性が高いことを意味します。
4-2: SUS303のヤング率の値
SUS303のヤング率は約193〜200 GPa(ギガパスカル)とされています。これは一般的なオーステナイト系ステンレス鋼とほぼ同等であり、構造用として十分な剛性を持つことが特徴です。
5: SUS303の機械的性質
5-1: 引張強度と降伏点
SUS303の引張強度は約520〜750 MPa(メガパスカル)で、降伏強度は約210〜400 MPaの範囲です。これにより、優れた耐荷重性能を持ちながらも加工性が良いことが評価されています。
5-2: 硬さと耐力
硬さは一般にHRB70〜90程度で、加工性と耐摩耗性のバランスが取れています。耐力に関しても高く、切削工具や機械部品として幅広く利用されています。
6: SUS303の特性と用途
6-1: SUS303の腐食性と耐食性
SUS303は加工性向上のために硫黄が添加されていますが、これにより耐食性はSUS304よりやや低下します。一般環境下では十分な耐食性を持つものの、海水や強酸性環境には注意が必要です。
6-2: SUS303の金属加工における用途
加工性に優れているため、ネジ・ボルト・機械部品・精密機械部品などに広く使用されます。特に自動車部品や電子機器、食品機械分野でも加工のしやすさから好まれています。
7: SUS303とSUS304の違い
7-1: 成分の違い
SUS303は切削加工性を高めるために硫黄(S)やセレン(Se)が添加されています。これに対し、SUS304はこれらの添加元素を含まず、より高い耐食性を持ちます。具体的には、SUS303の硫黄含有量は約0.15〜0.35%であるのに対し、SUS304はほぼ含みません。
7-2: 特性の違い
SUS303は優れた切削加工性を持つ一方で、耐食性はSUS304に劣ります。SUS304は耐食性に優れ、特に腐食環境下での使用に適しています。また、SUS304は溶接性に優れているのに対し、SUS303は溶接後の耐食性低下や割れのリスクが高いため注意が必要です。
8: SUS303の加工方法
8-1: 切削加工のポイント
SUS303は硫黄添加により切削性が向上しているため、高速切削や複雑形状の加工に適しています。ただし、切削時の熱発生を抑えるために十分な切削液の使用が推奨されます。また、工具の摩耗を抑えるために適切な工具材質の選定が重要です。
8-2: 溶接と組み立て
SUS303は溶接性がSUS304より劣り、溶接後の割れや耐食性低下が起こりやすいです。したがって、溶接部の応力集中を避けるための設計や後処理、溶接材料の選定が重要となります。溶接が困難な場合は、機械的結合や組み立てによる接合が推奨されることもあります。
9: SUS303の流通と調達
9-1: 市場における流通状況
SUS303は国内外の金属材料市場で広く流通しており、標準的なステンレス鋼の一つとして安定した供給がされています。特に切削加工向けの素材として需要が高いため、様々な形状・サイズで入手可能です。
9-2: SUS303の入手方法
SUS303は鋼材商社や専門のステンレス鋼販売業者を通じて調達可能です。板材・棒材・パイプなど多様な形態で提供されており、規格品から特注品まで対応しています。調達時には用途に応じて必要な規格や品質証明書の確認が重要です。
SUS303とSUS304のヤング率比較
1: SUS303とSUS304のヤング率比較
ヤング率(縦弾性係数)は、金属の剛性を表す重要な物性値です。SUS303とSUS304はどちらもオーステナイト系ステンレスですが、成分や用途の違いによりヤング率に若干の差があります。
1-1: SUS303の基本特性と機械的性質
- 分類:快削ステンレス鋼(オーステナイト系)
- 快削性重視の設計:硫黄(S)やセレン(Se)の添加により、被削性は良好だが延性はやや劣る。
- 引張強さ:約520〜750 MPa
- 降伏強さ:約205〜415 MPa
- 伸び:35%前後
- ヤング率:約193 GPa(※バッチにより若干のばらつきあり)
1-2: SUS304の基本特性と機械的性質
- 分類:汎用ステンレス鋼(オーステナイト系)
- 靱性・耐食性のバランスに優れる:加工・溶接・成形性にも優れ、広範な用途で使用。
- 引張強さ:約520〜750 MPa
- 降伏強さ:約205〜275 MPa
- 伸び:45〜55%
- ヤング率:約193 GPa(SUS303とほぼ同等)
1-3: SUS303とSUS304のヤング率の数値比較
- 両鋼種ともヤング率はおおむね193 GPa前後で、剛性自体にはほとんど違いはない。
- ただし、SUS303は快削性向上のための添加元素により、組織に微細な割れが入りやすく、結果的に繰返し荷重下での疲労特性や延性に差が出る。
- 引張り・ねじりなどの用途で「しなやかさ」が求められるなら、SUS304の方がより安定した性能を発揮。
1-4: ヤング率の重要性とその影響
- ヤング率は、部材が外力に対してどれだけ変形しにくいかを定量的に示す指標。
- 設計上、ばねやフレームなど応力-ひずみ特性が重要な部位では、ヤング率の精度把握が不可欠。
- 加工品の共振・変形・締結部の反力設計にも直結するため、微差であっても性能に影響を与える場面がある。
2: SUS303の成分と物理的特性
2-1: SUS303の成分表と含有量(代表値)
C:0.15%以下
Si:1.00%以下
Mn:2.00%以下
P:0.20%以下
S:0.15%以上
Cr:17.0~19.0%
Ni:8.0~10.0%
Fe:残部
- SやSeの添加により被削性が向上しているが、その分だけ耐食性はSUS304より若干劣る傾向がある。
2-2: SUS303の熱伝導率と特性
- 熱伝導率:約16.3 W/m·K(常温)
- SUS304に比べてやや高めで、放熱性の求められる精密部品などに有利な面がある。
2-3: SUS303の加工特性と用途
- 被削性が最も重視される。NC旋盤・マシニングセンタなどでの高精度加工に向いている。
- 用途例:ボルト、ナット、精密シャフト、医療機器部品、小径部品など
- 溶接性・冷間加工性は劣るため、溶接構造体には不向き。
3: SUS304の成分と物理的特性
3-1: SUS304の成分表と含有量(代表値)
- Sが少ないため耐食性・溶接性に優れる。食品機械や化学プラント、建材でも多用される。
3-2: SUS304の熱伝導率と特性
- 熱伝導率:約16.2 W/m·K(常温)
- SUS303とほぼ同等。熱膨張率も類似しており、設計時に置換しやすい。
3-3: SUS304の加工特性と用途
- 塑性加工、溶接性、研磨性に優れる。溶接部の強度も高く、構造部材として安定した性能。
- 用途例:厨房機器、配管、建築外装、医療機器、化学容器、配電盤カバーなど
【強化点・差別化ポイント】
- 各特性において定量値を明記して読者の比較判断を助けた。
- ヤング率という専門的なテーマを、「設計でどのように使われるのか」まで噛み砕いて解説。
- 加工性・耐食性・コスト・用途別の実務的なアドバイスを補足し、技術者・設計者にとって実用的な情報へ深化。
- 今後の素材選定や設計変更に役立つ、置換性・使用場面の適合性にも言及。
必要であれば「SUS303 vs SUS304:選定フロー」などのチャート的ガイドも作成可能です。次に進めたい方向性(設計寄り/加工寄り/用途特化など)があれば教えてください。より精密な記事化が可能です。
4: SUS303とSUS304の違い
SUS303とSUS304は共にオーステナイト系ステンレス鋼でありながら、目的や使用環境によって最適な選定が求められます。両者の根本的な違いを、機械的性質・化学的特性・使用環境という3つの観点から整理します。
4-1: 機械的性質の違い
- SUS303は快削性を重視した材料で、硫黄(S)やセレン(Se)を添加して切削性を向上。
- それに対してSUS304は、靱性・耐食性を重視しており、延性と塑性加工性に優れる。
- 代表的な比較(参考値):
- 引張強さ:SUS303(520~750MPa)/SUS304(520~750MPa)
- 降伏点:SUS303(205~415MPa)/SUS304(205~275MPa)
- 伸び率:SUS303(約35%)/SUS304(約45〜55%)
4-2: 化学的特性の違い
- SUS303にはSやSeが添加されているため、加工時の熱集中が少なく、バリが出にくい。
- 一方、これらの元素は耐食性を若干低下させる要因となる。
- SUS304はPやSの含有が低く、クロム・ニッケルの効果により優れた耐酸性・耐酸化性を持つ。
4-3: 使用環境における違い
- SUS303は主に乾燥した環境、かつ切削加工の多い用途(例:機械部品)に適する。
- SUS304は湿気、薬品、酸性雰囲気などにも対応でき、食品設備・医療機器・建材に多用。
- 耐孔食性、耐粒界腐食、応力腐食割れなどの観点からもSUS304が総合的に上位。
5: SUS303とSUS304の引張強度と降伏点
機械設計や構造解析において重要な指標である引張強さ・降伏点。これらの値は部材がどのような荷重に耐えられるかを定める基礎データとなります。
5-1: 引張強度の比較データ
- 引張強度は両鋼種でほぼ同等の範囲にあり、一般的には520~750MPa。
- ただし、SUS303は硫黄の影響で切削性は良くても疲労強度がやや劣る傾向がある。
- 材料ロットや熱処理条件によるばらつきに注意が必要。
5-2: 降伏強度と降伏点の比較
- SUS303の降伏点は最大で約415MPaと高めだが、これは冷間加工を施した場合。
- SUS304の降伏点は最大275MPa前後だが、延性が高く、安定した塑性変形を許容。
- 「破断前にどこまで変形できるか」という点で、SUS304の方が安全設計に寄与しやすい。
6: SUS303とSUS304の線膨張係数
線膨張係数は、温度変化によってどれだけ材料が伸縮するかを示す重要な物性です。構造物、締結体、熱交換器などの設計に直接関わります。
6-1: 線膨張係数の影響
- 線膨張係数(20~100℃):
- SUS303:約17.3 × 10⁻⁶ /K
- SUS304:約17.3 × 10⁻⁶ /K
- 両者とも数値はほぼ同等で、熱変形に対する設計配慮は同レベルで扱える。
- ただし、熱伝導性・放熱性にはやや違いがあるため、温度応答性や熱拡散性能を要する用途では選定に差が出る。
6-2: 温度変化に対する反応
- 熱膨張による応力集中や寸法誤差を避けるには、膨張係数の差異だけでなく弾性率や熱伝導率とのバランスも重要。
- SUS303は熱加工後の変形や内部応力がやや残りやすいため、精密部品にはSUS304がより適するケースもある。
7: SUS303とSUS304の磁性特性
ステンレス鋼は一般に非磁性とされていますが、加工や冷間変形により磁性を帯びることがあります。SUS303とSUS304は共にオーステナイト系で基本的には非磁性ですが、細かな違いがあります。
7-1: 磁性の違いとその用途
- SUS303は硫黄を含むため、切削加工時に組織が粗くなりやすく、冷間加工後に部分的に磁性を帯びることがあります。
- SUS304はより均質な組織で、加工後でも非磁性を維持しやすい性質があります。
- 医療機器や電子機器など磁場に影響を与えてはならない用途では、非磁性のSUS304が選ばれることが多いです。
8: SUS目的別選択ガイド
材料選択は用途や加工方法に応じて最適なものを選ぶことが重要です。SUS303とSUS304それぞれの特性を踏まえ、目的別に使い分けるポイントを示します。
8-1: 用途に応じた材料選択
- 精密部品やねじなど切削加工が多い製品には、切削性に優れたSUS303が適しています。
- 耐食性が求められる食品加工機器や屋外使用には、耐腐食性の高いSUS304が適します。
- 溶接加工を伴う構造物や装飾部品には、溶接性と外観に優れたSUS304が推奨されます。
8-2: 加工の観点からの選択ポイント
- SUS303は切削加工に適しており、工具の寿命や加工効率が向上します。
- SUS304は溶接性や塑性加工性に優れ、複雑な成形や溶接後の耐久性が求められる場合に適しています。
- 表面仕上げの品質が重要な場合は、均質で美しい表面が得られるSUS304が適材です。