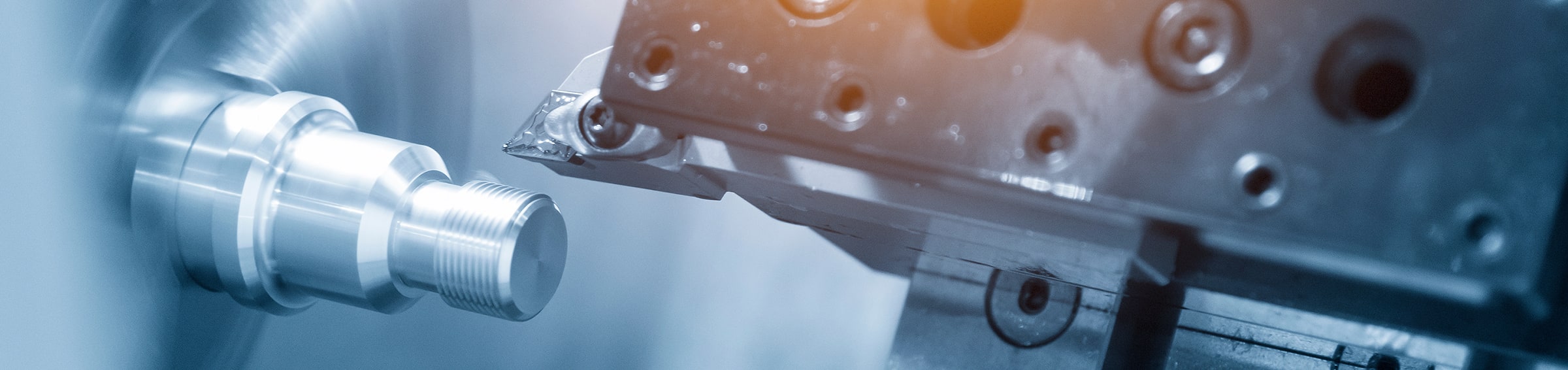
コラム column
ステンレスSUS選びで失敗しない!種類・特性・用途別使い道完全解説
ステンレスSUS(ステンレス鋼)を選ぶ際、失敗したくないですよね。どの種類が最適か、どんな特性があるか、またそれぞれの用途に合った使い道は何か――これらに関する情報を完全に解説します。ステンレス鋼は、その優れた耐久性や美しい外観からさまざまな用途に使用されていますが、種類ごとに特性が異なります。本記事では、ステンレスSUSの選び方や使い方について詳しく掘り下げます。それでは、失敗を避けてステンレスSUSを上手に活用するためのポイントをご紹介します。
ステンレスSUSの基礎知識
ステンレスSUSとは
ステンレスSUSとは、一般的にはステンレス鋼の一種を指します。SUSは、Steel Use Stainless(スチールユーズステンレス)の略称であり、主に日本で使われている呼び方です。ステンレスSUSは耐食性に優れ、錆びにくい特性があります。種類によっては強度や耐熱性、加工しやすさなどに違いがあります。
例えば、キッチン用品や建築材料、医療機器などのさまざまな分野で使用されています。特に、食品業界や海洋環境など、錆や腐食に強い特性が求められる場所で広く活用されています。
用途別に適したSUSを選ぶことで、効率的に利用できるだけでなく、長期的な耐久性も向上させることができます。ステンレスSUSの選び方を間違わないように注意して、適切に活用しましょう。
ステンレス鋼の歴史と発展
ステンレス鋼は、錆びにくい性質を持ち、さまざまな用途に利用される素材です。その歴史は古く、19世紀に誕生しました。当初は道具やカトラリーなどの製造に使われていましたが、その後、工業製品や建築材料などへの応用が広がりました。ステンレス鋼は、クロムを含むことで錆びにくさが実現されており、耐久性に優れています。食品加工業界や医療業界、建設業界など幅広い分野で使用されています。さまざまな種類があり、それぞれ特性や用途が異なります。適切な種類を選ぶことで、効果的に活用できます。ステンレスSUSを選ぶ際は、使用する環境や目的に合わせて適切な種類を選定することが重要です。
ステンレスSUSの主要成分と役割
ステンレスSUSは、さまざまな種類があり、それぞれ異なる特性や使い道があります。主要成分としては、鉄、クロム、ニッケルが挙げられます。クロムは錆びにくさを高める働きをしており、ニッケルは耐熱性を向上させる役割を果たしています。
SUSの種類によって、用途も異なります。たとえば、SUS304は一般的なステンレスとして広く使われており、食器やキッチン用具などによく使われています。一方、SUS316は食品加工業界や海洋環境での使用に適しており、耐食性に優れています。
ですので、ステンレスSUSを選ぶ際には、使用する環境や目的に合わせて適切な種類を選ぶことが大切です。適切なSUSを選ぶことで、効率的に利用することができ、長期間品質を維持できることが期待されます。
ステンレスSUSの種顺と特性
SUS種類の分類方法
ステンレスの選び方に失敗しないためには、SUS(ステンレス鋼)の種類を理解することが重要です。まず、SUSの分類方法について解説します。SUSはクロムを主成分とする鋼の総称であり、種類によって特性や用途が異なります。主な種類には、SUS304やSUS316などがあり、304は一般的なステンレス鋼であり、316は耐食性に優れたものです。
SUS304は一般的なキッチン用品や建築材料に使用され、一般家庭での利用に適しています。一方、SUS316は海水や薬品に耐性があり、食品工場や海洋施設で使用されることが多いです。自分の目的に合わせて適切なSUSを選ぶことが大切です。特性や使い道を考慮して、失敗せずに適切なSUSを選んでください。
代表的なSUS種類とその特性
ステンレスは、さまざまな用途に利用される素材です。代表的なSUSの種類とその特性について紹介します。まず、SUS304は一般的であり、耐食性に優れています。食器や厨房用具などによく使われています。SUS316はSUS304よりも耐食性が高く、海水などの腐食性が強い環境でも使用されます。例えば、船舶部品や海洋施設に適しています。また、SUS430は磁性があり、耐熱性に優れているため、家電製品や炉の部品として利用されています。それぞれの特性を理解して適切なSUSを選ぶことが重要です。用途や環境に合わせて適切なSUSを選ぶことで、長い間安心して利用することができます。
各種ステンレスSUSの耐蝕性について
ステンレスSUSは耐蝕性が高いため、様々な用途に使用されています。その耐蝕性能力は、鉄やその他の金属に比べて優れています。例えば、海水や化学薬品にさらされる環境での使用でも劣化が少なく、長期間にわたって品質を保つことができます。
種類によってその耐蝕性能力は異なります。SUS304やSUS316などの種類があり、それぞれ異なる特性を持っています。SUS304は一般的で耐食性が高く、家庭用品や建築など幅広い分野で使用されています。一方、SUS316は塩素や酸化物に強いため、海洋環境や製薬産業など厳しい条件下での使用に向いています。
ステンレスSUSを選ぶ際には、使用する環境や条件に適した種類を選ぶことが重要です。適切なSUSを選ぶことで耐久性や品質を確保することができます。
ステンレスSUSの耐熱性と強度
ステンレスSUSの耐熱性と強度は、その素材特性から注目される重要なポイントです。ステンレスSUSは、高温環境においても安定した性能を発揮し、変形や劣化が少ないため耐久性に優れています。例えば、厨房用の調理器具や熱交換器などの用途では、高温にさらされることが多いため、耐熱性が求められます。
さらに、ステンレスSUSは強度も優れており、重い荷物を支える構造物や屋外で使用される部品など、強い力に耐える必要がある場面で活躍します。そのため、建築や自動車産業など幅広い分野で利用されています。
ステンレスSUSの耐熱性と強度が優れているため、さまざまな産業で重要な役割を果たしています。その特性を活かして、安定した性能と耐久性を求める用途に幅広く活用されています。
ステンレスSUSの選定方法
使用環境に応じたSUSの選び方
ステンレスSUS選びで失敗しない!種類・特性・用途別使い道完全解説
SUS(ステンレス)は、さまざまな用途に使用される素材です。適切なSUSを選ぶためには、使用環境に応じて適した種類を選ぶことが重要です。例えば、食品工場では腐食に強いSUSが必要です。化学工場では耐熱性が求められます。
さらに、SUSの特性も考慮する必要があります。耐食性、耐熱性、強度などが重要な要素です。例えば、海水にさらされる環境では耐食性が重要です。
最後に、具体的な用途に合わせてSUSを選ぶことが大切です。建築用途、医療機器、家庭用品など、それぞれに適したSUSがあります。
使用環境、特性、用途を考慮してSUSを選ぶことで、効率的に素材を活用できることが重要です。
加工性に基づくSUSの選定
ステンレスの選定において重要な要素の一つは加工性です。SUSの種類や特性によって加工しやすさが異なります。例えば、SUS304は一般的で耐食性に優れるため、食品加工機器や厨房機器などに適しています。一方、SUS316は耐食性に優れ、塩水や酸性環境にも適しているため、海洋環境や化学プラントなどで使用されます。
加工性の良さからSUS430は金属切削加工や溶接加工に適しており、一般機械部品や自動車部品などの製造に使用されます。さらに、SUS420は高硬度で耐摩耗性に優れているため、刃物や金型などの高品質な部品に適しています。
適切なSUSの選定は使用用途に合わせた性能を引き出すために重要です。加工性に基づいた選定を行うことで効率的な生産や耐久性の向上につながります。
コストパフォーマンスを考慮したSUS選び
ステンレス製品を選ぶ際には、コストパフォーマンスも大切な要素です。例えば、SUS304は一般的なステンレスであり、耐食性に優れていますが、価格も比較的リーズナブルです。一方で、SUS316は塩分や酸に強いため、海水などの環境で使用する場合に適していますが、価格が高めです。さらに、SUS430は磁性があるため、磁石がくっつく場所などに使用されることが多いです。
用途に応じて適切なステンレスを選ぶことが重要です。例えば、屋外で使用する場合には耐久性が求められるため、SUS316やSUS430を選ぶのが適切です。一方、食器や調理器具など食品関連の用途には耐食性が必要なため、SUS304が適しています。
これらのポイントを考慮して、コストパフォーマンスをしっかりと考えた上で、最適なSUSを選ぶことが失敗しないポイントと言えます。
ステンレスSUSの見分け方
ステンレスSUSの見分け方を知っていますか?ステンレスは、種類や特性によってさまざまな用途に使われています。例えば、SUS304は一般的なステンレスであり、一般家庭や食品工場で使用されます。SUS316は耐食性が高く、海水や化学薬品による腐食に強いため、海洋環境や医療機器に適しています。ステンレスの使い道を選ぶ際には、環境や使用目的に適した種類を選ぶことが重要です。例えば、屋外で使用する場合は、耐食性の高いSUS316が適しています。種類ごとの特性を理解し、適切に使い分けることで、失敗せずに効果的に活用できます。ステンレスSUSを選ぶ際には、用途に合わせた種類を選んで、安全で長持ちする素材として活用しましょう。
ステンレスSUSの用途別使い道
建築・建設分野でのSUS利用
ステンレスSUSは、建築・建設分野で幅広く利用されています。その耐久性や耐食性から、外壁や屋根などの外装材として採用されることがあります。また、内装においても、キッチンや浴室の設備、手すりや階段などで使用されることが一般的です。耐久力やメンテナンスのしやすさから、公共施設や商業施設、住宅など、さまざまな場所で活躍しています。
特に、厨房設備や食品加工ラインなどの衛生面が重要な場所では、ステンレスSUSの使用が推奨されています。そのため、食品工場や病院、研究施設などでも広く使用されています。ステンレスSUSは、環境にやさしく、長期間にわたり美しい姿を保つことから、建築・建設分野でのニーズが高まっています。
食品・医療分野でのSUS利用
SUS(ステンレス)は、食品や医療分野で幅広く利用されています。その理由は、SUSが優れた耐食性を持ち、衛生的で清潔に保ちやすいからです。例えば、食品加工業では、SUS製の調理器具やタンクが使われています。これらは腐食しにくく、食品の品質を保つのに適しています。また、医療機器にもSUSが使われることが多く、手術道具やインプラントなどにも採用されています。
さらに、SUSは熱伝導性に優れているため、高温処理が必要な食品加工や滅菌プロセスにも適しています。そのため、食品や医療現場での信頼性が高い素材として重宝されています。これらの特性から、SUSは食品・医療分野で幅広く使われ、その重要性がますます高まっています。
自動車・航空機分野でのSUS利用
ステンレス鋼(SUS)は、自動車や航空機分野で幅広く利用されています。その耐食性、強度、耐熱性などの特性から、さまざまな部品や構造材として重要な役割を果たしています。例えば、自動車の排気管や車体パーツ、航空機の構造部品などに使用されています。
SUSにはさまざまな種類があり、それぞれ異なる特性や用途があります。例えば、耐食性に優れたSUS316は海洋環境で使用されることが多く、強度が求められる部品にはSUS304が適しています。
航空機の場合、軽量化と耐久性が求められるため、特に高強度で軽量なSUSを使用する傾向があります。これらの特性を理解し、適切なSUSを選ぶことで、自動車や航空機の性能向上に貢献することができます。
一般家庭でのSUS製品とその選び方
一般家庭でのSUS製品を選ぶ際には、用途に合った種類を選ぶことが重要です。例えば、キッチン用の調理器具や食器棚で使用する場合は、耐久性が求められるため、SUS304が適しています。SUS304は錆びにくく、清潔な状態を保ちやすい特性があります。一方、外装用途での使用には、見た目や光沢が重要となるため、SUS316が適しています。SUS316は錆びにくさと美しい仕上がりが特徴です。
その他にも、浴室やトイレの設備に使用する場合はSUS430が適しており、耐湿性があり手入れも簡単です。家庭内での使用においては、用途に合ったSUSを選ぶことで効果的に使い分けることができ、製品の寿命や美観を保つことができます。
ステンレスSUSの保守とメンテナンス
ステンレスSUS製品の日常的な手入れ
ステンレス製品は丈夫で扱いやすい素材ですが、日常的な手入れは大切です。汚れや錆を防ぐため、洗浄や乾燥が必要です。柔らかい布やスポンジを使い、中性洗剤で優しく拭いてください。その後、水で洗い流し、十分に乾かすことで美しい光沢を保つことができます。また、錆が発生した場合は、金属専用のクリーナーを使用して丁寧に取り除きましょう。ステンレスSUS製品は種類や特性によって使い道が異なるため、適切な手入れをして長く使えるようにしましょう。手入れを怠ると表面が劣化し、見た目や使い勝手が損なわれる可能性があります。日常的な手入れを行うことで、ステンレス製品の美しさを保ち、長く愛用できます。
ステンレスSUSの長期保全のコツ
ステンレスSUSを選ぶ際に失敗しないためには、種類や特性、用途別の使い道を理解することが重要です。例えば、SUS304は一般的に耐食性が高く、キッチン用品や建築など幅広い用途に向いています。一方、SUS316は塩水環境に強いため、海洋関連の設備や装置に適しています。使い道を明確に把握することで、材料の性質に適したSUSを選ぶことができます。
また、SUSの長期保全のコツとしては定期的な清掃やメンテナンスが欠かせません。特に、錆や汚れが溜まりやすい部分は定期的なチェックが重要です。適切な手入れを怠らず、必要に応じて適切な洗浄剤や方法を使うことで、SUSの性能を長く維持することができます。これらのポイントを押さえて、ステンレスSUSの選び方や保全について正しく理解しましょう。
錆や劣化の対策方法
ステンレスSUSを選ぶ際に失敗しないためには、適切な種類を理解し、特性と用途に合った使い道を知ることが重要です。ステンレスSUSは錆や劣化に強い素材として知られています。例えば、SUS304は一般的で汎用性が高く、家庭用品や建築材料によく使用されます。一方、SUS316は塩水や薬品に耐性があり、海洋環境や化学工業など厳しい条件下で使用されます。使用環境や目的によって適したSUSを選ぶことで、劣化を防ぎ長期間の使用を可能にします。確実な選択をするためには、専門家のアドバイスを受けることも大切です。適切なSUSを選ぶことで、素材の特性を最大限に活かし、効果的に利用することができます。
ステンレスSUSの購入ガイド
購入前に確認すべきポイント
ステンレスSUSを選ぶ際に失敗しないためのポイントをご紹介します。ステンレス鋼は種類によって特性が異なり、用途に適したものを選ぶことが重要です。例えば、SUS304は一般的な用途に向いており、食器やキッチン用品に使われます。一方、SUS316は耐食性に優れており、海洋環境や化学工業での使用に適しています。さらに、SUS430は耐熱性に優れているため、炊飯器やオーブンなどの高温で使用される機器に適しています。用途に合ったSUSを選ぶことで、品質や耐久性を確保できます。それぞれの特性を理解し、正しく選んで利用することで、失敗を防ぎ、長く使える製品をお楽しみいただけます。
ステンレスSUSの品質基準と認証マーク
ステンレスSUSを選ぶ際に失敗しないためには、適切な品質基準と認証マークを理解することが重要です。ステンレス鋼は、耐食性や耐熱性に優れており、さまざまな用途に使われています。しかし、異なる種類のSUSがあり、それぞれ特性が異なります。例えば、SUS304は一般的な食器やキッチン用具に向いていますが、SUS316は海水や薬品に強いため、造船や医療機器に使用されます。
さらに、ステンレスSUS製品には品質を示す認証マークがあります。JISマークやISOマークなどの認証を持つ製品は、信頼性が高く、安心して使用できます。適切な品質基準と認証マークを確認することで、自宅のキッチンから産業機器まで幅広い場面でステンレスSUSを活用し、失敗せずに使い道を見つけることができます。
信頼できるメーカーとブランドの選び方
ステンレスSUSを選ぶ際に失敗しないためには、信頼できるメーカーやブランドを選ぶことが重要です。日本で信頼性の高いメーカーは、品質と信頼性が確保されています。例えば、●●メーカーは種類によって高い強度や耐食性を持っており、建築や食品業界で広く使用されています。他にも●●ブランドは耐久性に優れており、環境に配慮した製品を提供しています。これらのメーカーやブランドを選ぶことで、安心してステンレスSUSを選ぶことができます。結論として、信頼できるメーカーやブランドを選ぶことで、ステンレスSUSの種類や特性に合った使い道を見つけることができます。
よくある質問とトラブルシューティング
ステンレスSUS選びでのよくある誤解
ステンレスSUSを選ぶ際によくある誤解として、同じステンレスSUSでも種類や特性、用途によって適しているものが異なることが挙げられます。例えば、SUS304は一般的な用途に向いており、SUS316は耐食性に優れているため食品工場や外部設備に適しています。その他にも、SUS430は磁性があり熱に弱いため、一般家庭の調理器具に使われることが多いです。
種類や特性を理解していないと、適切な使い道を見誤る可能性があります。したがって、ステンレスSUSを選ぶ際には、どのような環境や用途で使用するのかを考慮し、適切な種類を選ぶことが重要です。それにより、長い期間使い続ける上での効果的な選択ができるでしょう。
ステンレスSUS使用時のトラブルと解決策
ステンレスSUSを選ぶ際に起こりやすいトラブルや解決策についてお伝えします。異なるSUSタイプを誤って使用すると、耐久性や耐食性が不十分になり、錆や劣化が生じる可能性があります。たとえば、SUS304は一般的な用途に適していますが、酸化剤やクロライドイオンに弱いため、高温多湿な環境ではSUS316を選ぶ方が適しています。SUS430は熱や酸化物に強いが、耐食性が劣ります。
正しいSUSを選ぶことで、寿命を延ばし、メンテナンスコストを抑えることができます。使用環境や要件に合わせて適切なSUSを選択し、定期的な点検や管理を行うことが大切です。最適なSUSを選ぶことで、長期間安心して使用することができます。
ステンレスSUSに関するQ&A
ステンレスSUSに関するQ&A
ステンレスSUSを選ぶ際に失敗しないように、種類や特性、用途を理解しておくことが重要です。ステンレスSUSは耐久性に優れ、さまざまな分野で使用されています。例えば、キッチン用具や建築材料、医療機器など幅広い用途があります。
ステンレスSUSの種類には、SUS304やSUS316などがあり、それぞれ特性が異なります。SUS304は一般的で耐食性が高いため、食器や調理器具に適しています。一方、SUS316は塩水や酸に強く、海洋環境や医療機器などで重宝されています。
適切なステンレスSUSを選ぶことで、使用用途に応じた耐久性や安全性を確保できます。そのため、用途に合わせて適切な種類を選ぶことが大切です。
最新トレンドと未来のステンレスSUS
ステンレスSUSの新技術と研究動向
ステンレスSUSは、多種多様な用途に活用される素材です。最新の技術や研究動向について informality います。例えば、SUS304は一般的なステンレス鋼で、耐食性に優れています。食品加工業や建築業界で広く使用されています。SUS316は塩分の多い環境での使用に適しており、海水浴場や海洋プラントで重宝されています。また、SUS430は磁性があり、家庭用品や自動車部品などに利用されています。適切なSUSの選択は、製品の性能や耐久性に直結します。研究により、より強靭なSUS合金や耐熱性を持つ新素材が開発されています。これらの進化により、様々な産業でのステンレスSUSの活用がさらに広がることが期待されます。
環境に優しいステンレスSUSの開発
ステンレスSUSは、環境に優しい素材として開発が進んでいます。環境問題が深刻化する中、持続可能な生産と使用が求められています。ステンレスSUSはその点で優れた特性を持ち、再利用やリサイクルが可能なことから注目を集めています。
例えば、自動車業界では、環境への配慮から軽量で高強度なステンレスSUSが使用され、燃費向上や排出ガス削減に貢献しています。また、建築業界でも耐久性や美観を兼ね備えたステンレスSUSが建材として使用され、長期的な環境負荷を低減しています。
これからも、さまざまな産業でステンレスSUSの利用が広がることが期待されます。環境負荷の低減や持続可能な社会の実現に向け、ステンレスSUSの進化と活用が重要なポイントとなるでしょう。
今後のステンレスSUS市場の展望
今後のステンレスSUS市場の展望
ステンレスSUS(ステンレススチール)は様々な種類があり、その特性や用途も異なります。ステンレスSUSの選び方で失敗しないためには、用途に合った適切な種類を選ぶことが重要です。
たとえば、キッチン用品などの食品関連アイテムには錆びにくいSUS304が適しています。一方、強度が求められる建築や構造物にはSUS316が適しています。さらに、熱伝導性が必要な調理器具にはSUS430が適しています。
用途によって選ぶSUSの種類が異なるため、適切な選択をすることで耐久性や安全性を確保できます。ステンレスSUS市場は今後も需要が高まると予測されており、適切に選ぶことで失敗せず効果的に活用できるでしょう。
まとめ
ステンレスSUSの選び方について、種類や特性、用途に応じた使い道について解説しました。ステンレスSUSはさまざまな種類があり、それぞれ異なる特性を持ちます。適切な種類を選ぶことで、使用する用途に最適な性能を発揮させることができます。選び方に失敗しないために、この解説を参考にしてみてください。
ステンレスSUSクロム合金の特性と選び方
ステンレスSUSクロム合金の特性と選び方について知識を深めたいと思ったことはありませんか?ステンレス製品を選ぶ際には、素材の特性や適用場所に合った選び方が重要です。この記事では、ステンレスSUSクロム合金の特性や選び方について詳しく解説します。どのような特性を持ち、どのように選ぶべきか、そのポイントを明確に紐解きます。製品を選ぶ際に迷っている方やステンレス製品に興味のある方にとって、役立つ情報が満載です。是非、最適な選択をするためのヒントを得てみてください。
ステンレスSUSクロム合金の基本
ステンレスとは:定義と歴史
ステンレスSUSクロム合金の特性と選び方
ステンレスSUSクロム合金は、耐食性に優れた素材です。これは、クロムを含む合金が表面を酸化させ、錆びずに使い続けられるからです。クロムの割合が高いほど、耐久性が増します。
例えば、キッチン用の調理器具や建築材料としてよく使われています。その理由は、ステンレスSUSクロム合金が優れた耐熱性と耐久性を持つからです。さらに、清潔感があり、メンテナンスがしやすい点も人気の秘密です。
選び方としては、使用目的や環境に合わせてクロム含有量や強度などを考慮することが重要です。素材の特性を理解し、適切なステンレスSUSクロム合金を選ぶことで、長い間快適に使用することができます。
SUSクロム合金の特性
SUSクロム合金は、耐久性や耐蝕性が高く、さまざまな用途に適しています。クロムの添加により酸化防止や耐食性が向上し、錆びにくい特性を持ちます。例えば、キッチン用品や建築材料などに広く使用されています。また、高温にも強く、熱処理を施すことで硬度が向上するため、機械部品や工業製品にも適しています。これにより、長期間使用しても劣化しにくいという利点があります。素材選びの際には、使用目的や環境に適したクロム合金を選ぶことが重要です。特に、SUS304やSUS316などが一般的に使用されています。適切な合金を選ぶことで、製品の品質や耐久性を高めることができます。
ステンレスの分類とSUSクロムの位置づけ
ステンレスの分類とSUSクロムの位置づけ
ステンレスは耐食性に優れるため、様々な用途に利用されています。その中でもSUSクロム合金は一般的なステンレスの一種です。SUSとは、Steel Use Stainlessの略であり、クロムを主成分とする合金です。クロムの添加により、酸化や腐食に強くなります。
例えば、SUS304は一般的なステンレスとして広く使われています。食器やキッチン用品、建築材料など多岐にわたる製品に使用されています。SUS316は、海水環境や化学工業など厳しい環境下での利用に適しています。
ステンレスを選ぶ際には、使用環境や要求される性能に合わせて適切な種類を選ぶことが重要です。このように、SUSクロム合金はその特性によって様々な分野で重要な位置を占めています。
ステンレスの種類と特徴
オーステナイト系ステンレスの特徴
ステンレスSUSクロム合金は、耐食性や耐熱性に優れたオーステナイト系ステンレスの一種です。クロムを主成分とするこの合金は、一般的には食器や建築材料など幅広い分野で使用されています。その特性から、食品加工業界や化学工業などで多く採用されています。
SUSクロム合金は、錆びにくく美しい外観を維持することができるため、建築材料として人気があります。さらに、耐熱性が高いため、高温の環境でも安定した性能を発揮します。
例えば、キッチン用具や食器類に使用されるステンレス製品は、その耐久性や使いやすさから一般家庭でも広く愛用されています。これらの特性から、SUSクロム合金は幅広い用途に適しており、選ぶ際には使用目的に合わせて適切な合金を選ぶことが重要です。
フェライト系ステンレスの特徴
ステンレスSUSクロム合金の特性と選び方
SUSクロム合金は、耐食性に優れ、錆びにくい特性があります。この特性は様々な用途に適しています。例えば、厨房機器や建築材料などで広く使用されています。SUSクロム合金は、その強度や耐熱性も優れているため、高温環境や腐食性のある環境においても優れたパフォーマンスを発揮します。
選ぶ際には、使用する環境や目的に合わせて適切な種類のSUSクロム合金を選ぶことが重要です。例えば、耐熱性が求められる場合は、適切なクロム含有量や他の合金成分を考慮する必要があります。また、見た目や加工性も重要な要素となります。適切なSUSクロム合金を選ぶことで、長期間にわたり高い性能を維持することが可能となります。
マルテンサイト系ステンレスの特徴
ステンレスSUSクロム合金の特性と選び方
ステンレスSUSクロム合金は、耐食性に優れ、強度も高く、耐熱性もあるのが特徴です。クロムの添加により、酸化物皮膜を形成し、外部からの侵食を防ぎます。また、クロムの含有量が高いほど、耐食性が向上します。このため、海洋環境や化学工業などの厳しい環境下でも優れた性能を発揮します。
SUSクロム合金を選ぶ際には、使用環境に合ったクロム含有量や耐熱性などの特性を考慮することが重要です。例えば、海水に接する部品や高温環境で使用する部品など、用途に応じて適切なステンレスSUSクロム合金を選ぶことが大切です。結局、正しい選択をすることで、長期的な耐久性や安定性を確保できます。
複合系(デュプレックス)ステンレスの特徴
ステンレスSUSクロム合金の特性と選び方
ステンレスSUSクロム合金は、耐腐食性に優れた特性を持ち、耐熱性や強度も高いという特長があります。このため、厨房機器や建築材料、様々な工業製品など幅広い用途に使用されています。
SUSクロム合金の選び方には、使用環境や耐久性の要求などを考慮する必要があります。例えば、海水や化学物質にさらされる場所では、耐食性が重要になります。また、高温環境では耐熱性が求められます。
具体例として、厨房用途ではSUS304が一般的に使用され、建築材料にはSUS316が好まれます。選び方を間違えると、性能が十分発揮されず、劣化や破損のリスクが高まります。したがって、用途に合わせて適切なステンレスSUSクロム合金を選ぶことが重要です。
ステンレスの適切な使用法と取り扱い方法
ステンレス製品の一般的な使用法
[ステンレスSUSクロム合金の特性と選び方]
SUSクロム合金は、耐久性、耐食性、そして美しい外観が特徴です。これらの特性から、料理器具や建築材料、輸送機器など幅広い用途で使用されています。例えば、キッチン用品や自動車の排気管などが挙げられます。
ステンレスSUSクロム合金を選ぶ際には、使用環境や目的に適した合金を選ぶことが重要です。環境によっては、耐熱性や耐蝕性が必要となるため、適切な合金を選択することが必要です。また、外観や加工性も考慮するとよいでしょう。
要するに、SUSクロム合金の特性と適性を理解し、使用目的に合った合金を選ぶことが重要です。これにより、長い耐久性と美しい外観を持つ製品を選ぶことができます。
ステンレスSUSクロム合金の取り扱い上の注意点
ステンレスSUSクロム合金の特性と選び方
SUSクロム合金は、その耐久性と耐食性により広く使用されています。クロムの添加によってさらなる強度と耐久性が付加され、さまざまな産業分野で重要な役割を果たしています。クロムの割合が高いほど、耐食性が向上し、表面が光沢を保ちやすくなります。
選び方において重要なポイントは、使用目的に合ったクロムの割合と強度を選定することです。たとえば、食品業界では衛生管理が重要なため、高クロム含有率の合金が好まれます。一方、建築業界では強度が求められるため、強度を重視した合金が適しています。
このように、SUSクロム合金はその特性に応じて選ぶことが重要です。使用目的や要件に合った適切な合金を選ぶことで、耐久性や効率性を向上させることができます。
環境に応じたステンレスの使用
ステンレスSUSクロム合金は、その特性からさまざまな環境で使用されています。例えば、耐食性に優れているため、海水や化学物質のある環境でも錆びずに長持ちします。これは、海洋施設や工場などの厳しい環境下でも安心して使用できる理由です。
さらに、SUSクロム合金は強度が高く、高温にも耐えることができます。そのため、熱処理装置や高温の機械部品などの用途にも適しています。例えば、炉内部の構造部品や航空機のエンジン部品などに広く使用されています。
環境に応じて適切なステンレスを選ぶことが重要です。ステンレスSUSクロム合金はその特性から幅広い分野で活躍しており、適切に選ぶことで長期間利用することができます。
ステンレスの選び方と適切な用途
用途に応じたステンレスの種類の選び方
ステンレスSUSクロム合金は様々な用途に応じて異なる特性を持っています。例えば、食品加工機械や厨房機器などの食品業界では、SUS304が広く用いられています。SUS304は耐食性が高く、洗浄や消毒にも適しています。一方、耐熱性が求められる炉や熱交換器などの高温環境では、SUS310Sが適しています。さらに、耐食性や磁性が必要な場合は、SUS430が選ばれることがあります。
したがって、ステンレスSUSクロム合金を選ぶ際には、用途に応じた特性を確認することが重要です。適切なステンレスを選ぶことで、長期間の使用や効率的な機能を実現することができます。要件に合った適切なステンレスを選ぶことで、品質の向上とコスト削減につながることを忘れないようにしましょう。
SUSクロム合金の選択基準
SUSクロム合金の選択基準
SUSクロム合金は、耐食性や強度に優れた特性を持つ素材です。選ぶ際には、使用目的や環境に合わせて適切な種類を選ぶことが重要です。
まず、使用目的に合わせて選ぶことがポイントです。例えば、屋外での使用や高温環境下での利用を考える場合は、耐食性が高いSUSクロム合金を選ぶ必要があります。
さらに、具体的な例として、食品加工業界ではSUS304が広く使用されています。これは、食品との相性が良く衛生面でも安心できるためです。
適切なSUSクロム合金を選ぶことで、長期間安定した性能を発揮し、維持管理の負担も軽減されます。使用環境や目的を考慮して、最適なSUSクロム合金を選択しましょう。
特定の産業でのステンレスの選び方
[特定の産業でのステンレスの選び方]
ステンレスSUSクロム合金は、さまざまな産業で重要な素材として使われています。素材を選ぶ際に重要なポイントは、耐久性、耐食性、加工性などです。例えば、建築業界では、外部環境にさらされる建築物には耐久性が求められます。そのため、SUS316やSUS316Lのような耐食性に優れたタイプが適しています。また、食品業界では、食品衛生基準をクリアするためにSUS304が一般的に利用されています。
つまり、ステンレスSUSクロム合金を選ぶ際には、その素材特性を産業や用途に合わせて選定することが重要です。適切なステンレスを選ぶことで、耐久性や耐食性を確保しつつ、業務効率や品質の向上につなげることができます。産業ごとの適切な選定が、ステンレスの効果的な活用につながります。
ステンレスの加工と加工技術
ステンレスの成形方法
ステンレスSUSクロム合金の特性と選び方
ステンレスSUSクロム合金は、耐久性と美観を兼ね備えた素材として広く使用されています。その特性を理解し、適切に選ぶことが重要です。
まず、ステンレスSUSクロム合金の耐食性や強度を考慮して選ぶことが大切です。例えば、屋外で使用する場合は錆びにくいタイプが適しています。また、使い方によっては耐熱性や耐摩耗性も重要な要素となります。
さらに、環境にやさしい素材であるかどうかも重要です。リサイクル性や清潔性なども考慮すべき点です。
このように特性を考慮し、目的に合ったステンレスSUSクロム合金を選ぶことで、長い間利用することができます。適切な選択は、安全性や使いやすさなどの面でも重要です。
SUSクロム合金の溶接技術
[ステンレスSUSクロム合金の特性と選び方]
SUSクロム合金は耐食性に優れ、さまざまな分野で幅広く使用されています。この特性を活かすためには、適切な溶接技術の選択が重要です。
まず、SUSクロム合金の溶接技術を選ぶ際に考慮すべき点は、合金の成分や硬さ、溶接箇所の用途などです。例えば、高クロム含有量の合金は炭素鋼よりも溶接難易度が高いため、適切な電極や溶接方法を選択する必要があります。
さらに、溶接が必要な部位の規模や形状も考慮することが重要です。適切なプロセスや溶接機器を選択することで、強固な溶接接合を実現できます。
適切な溶接技術を用いることで、SUSクロム合金の特性を最大限に活かし、高品質な製品を生産することが可能です。
表面処理と仕上げ技術
[ステンレスSUSクロム合金の特性と選び方]
ステンレスSUSクロム合金は、耐食性や耐熱性に優れています。クロムの添加によって錆びにくくなり、長期間使用しても品質を保ちます。また、表面処理や仕上げ技術によってさらなる特性が引き出されます。
例えば、鏡面仕上げは美しく光沢があり、装飾や外観に適しています。サテン仕上げは光沢を抑え、指紋や傷が目立ちにくい特徴があります。さらに、耐熱性を求める場合は焼き入れ処理を施すことで耐熱特性が向上します。
これらの特性を考慮して、使用目的や環境に適したステンレスSUSクロム合金を選ぶことが重要です。適切な表面処理や仕上げ技術を選択することで、製品の耐久性や美観を向上させることができます。
ステンレス製品のメンテナンスとお手入れ方法
日常的なステンレス製品のお手入れ
「ステンレスSUSクロム合金の特性と選び方」
ステンレスは耐食性に優れ、さまざまな用途で利用されています。SUSとはステンレス鋼を表す略語であり、その中でもクロム合金は強靭で錆びにくい特性を持っています。一般的な家庭用品から建築材料まで幅広く使用されています。
ステンレスSUSクロム合金を選ぶ際には、使用環境や耐久性を考慮することが重要です。例えば、屋外での利用や食品加工器具には耐久性が求められます。また、デザイン性やメンテナンスの容易さも選定ポイントとなります。
したがって、ステンレス製品を選ぶ際には、使用目的や環境に合った適切なクロム合金を選ぶことが重要です。そのような特性を考慮することで、長期間にわたって安心して使用することができます。
SUSクロム合金製品の特別なメンテナンス
[SUSクロム合金の特性と選び方]
ステンレスSUSクロム合金は、耐久性や耐食性に優れた素材として知られています。この合金は、錆びや腐食に強く、高温や低温にも強い特性を持っています。そのため、食品加工業や化学工業など、さまざまな産業で広く利用されています。
SUSクロム合金を選ぶ際には、使用環境や目的に合ったグレードを選ぶことが重要です。たとえば、食品加工業ではSUS304が一般的に使用されますが、耐食性が求められる場合はSUS316が適しています。また、外装用途にはSUS430が適しています。
適切なSUSクロム合金を選ぶことで、長い間安定した性能を維持することができます。素材の特性を理解し、適切に選ぶことで、製品や設備の劣化を防ぎ、安全性や耐久性を確保できます。
長期保管時のステンレス製品のケア方法
[ステンレスSUSクロム合金の特性と選び方]
ステンレスSUSクロム合金は、耐久性と耐食性に優れた素材です。この特性から、さまざまな用途に幅広く使用されています。例えば、キッチン用品や建築材料、医療機器などに利用されています。そのため、選ぶ際には使用目的に合った適切なクロム含有量や硬さを選ぶことが重要です。
ステンレスSUSクロム合金の中でも、SUS304やSUS316などが一般的に用いられています。SUS304は一般家庭用品に適しており、SUS316は耐食性に優れているため、外部環境にさらされるものに適しています。使用環境や耐久性などを考慮して適切な合金を選ぶことで長く使える製品を選ぶことができます。
ステンレスSUSクロム合金のトラブルシューティング
錆や腐食の原因と対策
ステンレスSUSクロム合金は、錆や腐食といった問題に強い素材です。クロムを含むことで、酸化被膜が形成され、金属表面を保護します。このため、湿気の多い環境や腐食性のある物質にさらされても、優れた耐久性を発揮します。例えば、キッチン用具や建築材料など、様々な分野で幅広く利用されています。
SUSクロム合金を選ぶ際には、使用環境に適した耐久性や強度が重要です。特に屋外や食品関連の設備では、クロム含有量や耐食性に注目すると良いでしょう。例えば、海水や塩分の多い場所では、モリブデンを含むタイプのSUSクロム合金が適しています。
耐久性や強度を考慮しつつ、使用環境に適したステンレスSUSクロム合金を選ぶことで、長期間安心して利用することができます。
破損や変形への対応
ステンレスSUSクロム合金は、その耐久性や強度から幅広い用途に使用されています。この合金は一般的に、耐食性や熱伝導性に優れており、さまざまな環境下で優れた性能を発揮します。
例えば、キッチン用具や建築材料、医療機器など幅広い分野で使用されています。そのため、選ぶ際には使用用途や環境に合わせた適切な種類を選ぶことが重要です。
破損や変形への対応も重要なポイントです。選ぶ際には耐久性や加工性などを考慮して、最適なSUSクロム合金を選ぶことが大切です。
まとめると、ステンレスSUSクロム合金はその特性から幅広い用途に適しており、選ぶ際には使用用途や耐久性などを考慮して適切な種類を選ぶことが大切です。
修理と補強の方法
ステンレスSUSクロム合金は、耐食性や強度に優れ、様々な用途に使われています。その特性を理解し、適切な選び方をすることが重要です。
まず、ステンレスSUSクロム合金の特性は、耐食性が高いことです。これは錆びにくい素材であり、長期間使用しても劣化しにくい特徴があります。さらに、強度も兼ね備えており、耐久性に優れています。
例えば、キッチン器具や建築資材、自動車部品など、さまざまな分野で活躍しています。これらの製品は、ステンレスSUSクロム合金の特性を活かしているのです。
したがって、選ぶ際には使用用途に合ったクロム含有量や強度などを考慮して適切な材料を選ぶことが大切です。ステンレスSUSクロム合金はその特性から幅広い分野で重宝されており、適切に選ぶことで高い性能を発揮します。
ステンレスSUSクロム合金の市場と今後の展望
現在のステンレス市場の動向
ステンレスSUSクロム合金の特性と選び方
ステンレスSUSクロム合金は、耐摩耗性、耐食性、および加工性に優れています。特に、SUS304合金は一般的であり、食器や建築材料など幅広い用途に使用されます。クロムの添加により、酸化物皮膜が形成され、耐食性が向上します。
選び方においては、使用環境や用途に適した合金を選ぶことが重要です。例えば、海洋環境ではSUS316が適しており、耐食性が求められる機械部品にはSUS440Cが適しています。
要するに、ステンレスSUSクロム合金を選ぶ際には、耐摩耗性や耐食性などの特性を考慮し、使用環境に最適な合金を選ぶことが重要です。これにより、製品の耐久性や品質向上につながるでしょう。
新しいSUSクロム合金の開発
新しいSUSクロム合金は、工業製品や建築など様々な分野で利用されています。これらの合金は、耐久性や耐食性に優れていることが特徴です。SUSクロム合金は、日本国内の多くの製品に使用されており、その需要は増加の一途を辿っています。
例えば、キッチン用具や自動車部品など、日常生活で使われる様々な製品にSUSクロム合金が使用されています。その耐久性や美観から、多くの消費者に支持されています。実際、日本の製造業は世界的に高い評価を受けており、その一部がSUSクロム合金の製造に貢献しています。
最近の開発では、新しいSUSクロム合金がさらなる性能向上を遂げています。これにより、製品の品質や効率が向上し、さまざまな産業分野での利用価値が高まっています。新しいSUSクロム合金の選び方には、目的に応じた材質の特性や耐用年数などを考慮することが重要です。
ステンレスの持続可能性と環境への影響
ステンレスSUSクロム合金の特性と選び方
ステンレスSUSクロム合金は、耐食性や耐熱性に優れており、さまざまな用途で広く使用されています。クロムの添加により、錆びにくく、高温にも強い特性を持っています。そのため、キッチン用品や建築材料などの製品によく使われています。
ステンレスSUSクロム合金を選ぶ際には、使用目的に適した耐熱性や耐食性を考慮することが重要です。例えば、屋外で使用する場合は耐久性が求められますが、室内で使用する場合は見た目も重要となります。
クロム合金の選び方には、材料の耐久性やメンテナンスのしやすさ、価格などを考慮することが大切です。適切なステンレスSUSクロム合金を選ぶことで、製品の長寿命化や使用環境における安全性を確保することができます。
まとめ
ステンレスSUSクロム合金は耐食性に優れ、高温環境にも強い特性を持っています。その耐食性は、さまざまな化学物質や環境に対して優れた耐性を示し、長期間の使用にも適しています。また、クロムの添加によって耐摩耗性や硬度も向上し、耐久性が向上します。これにより、機械部品や建築材料など、さまざまな分野で幅広く利用されています。選び方としては、使用環境や目的に適したクロム含有量や特性を適切に選定することが重要です。
SUS素材の鏡面仕上げに挑戦!研磨で差をつける方法
ステンレス鏡面仕上げの基礎知識
ステンレス(SUS)材料とは
項目 | 詳細 |
---|---|
基本概要 | ステンレス鋼(SUS)は、クロムを含む耐腐食性の高い合金鋼です。 |
代表的な種類 | SUS304(一般用途向け)、SUS316(耐食性がさらに高い)などが代表例。 |
特徴 | 高強度、耐熱性、耐食性に優れ、幅広い分野で利用されます。 |
用途 | キッチン用品、建築部材、医療機器、自動車部品など多岐にわたります。 |
ステンレス材料の特性
- 高い耐腐食性により、湿度の高い環境や化学物質にさらされる場所でも使用可能。
- 鉄と比較して硬度が高いため、加工時に適切な工具選びが必要。
鏡面仕上げのメリット
項目 | 詳細 |
---|---|
美観の向上 | 表面が滑らかで光沢があり、高級感のある仕上がりを提供。 |
耐汚染性の向上 | 滑らかな表面が汚れや錆を防ぎ、清掃が容易。 |
耐食性の向上 | 表面粗さを減らすことで腐食の進行を抑える効果を発揮。 |
用途の拡大 | デザイン性を求められるインテリアや装飾用途に最適。 |
利用シーン
- 高級家具や建築装飾品。
- 鏡面効果を活用した反射材やディスプレイ。
- 医療器具や食品加工設備での清掃性向上。
鏡面磨きに挑戦する前の準備
項目 | 詳細 |
---|---|
適切な研磨剤の選定 | ステンレスに適した研磨剤(例:酸化アルミニウムやダイヤモンドペースト)を準備。 |
作業環境の整備 | 安全な作業スペースと十分な換気、照明を確保。 |
適切な工具の用意 | 研磨ホイール、研磨パッド、バフなどを用途に応じて用意。 |
試し磨きの実施 | 余った材料や目立たない部分でテストを行い、適切な仕上げ手法を確認。 |
保護具の装着 | 作業時には保護メガネ、手袋、エプロンを着用し、安全を確保。 |
準備のポイント
- 研磨剤と工具の組み合わせを確認し、作業効率を最大化する。
- 作業前に素材の表面状態を確認し、傷や汚れがある場合は事前処理を行う。
- 作業時間を十分に確保し、焦らず丁寧に行うことが成功の鍵。
全体のまとめ
ステンレスの鏡面仕上げは、美観や耐久性を向上させるだけでなく、さまざまな用途での利用価値を高めます。効率的な仕上げのためには以下の点が重要です:- ステンレスの特性を理解し、適切な手法を選択。
- メリットを把握して作業の目的を明確化。
- 準備を万全に整えることで、均一かつ高品質な鏡面仕上げを実現。
ステンレスの鏡面仕上げ方法
研磨工程の概要
工程 | 内容 |
---|---|
表面の清掃 | 作業開始前に表面の汚れや油分をしっかり落とし、クリーンな状態を確保します。 |
粗研磨 | 初期状態の表面を整えるため、#120~#240程度の粗い研磨剤を使用して研磨します。 |
中研磨 | 表面の傷を均一に整えるため、#400~#600の研磨剤でさらに滑らかに仕上げます。 |
仕上げ研磨 | 鏡面に近い仕上がりにするため、#800以上の研磨剤やバフを使って丁寧に磨きます。 |
仕上げ処理 | 最後に研磨剤を落とし、ステンレス専用のコーティング剤を塗布して保護します。 |
初心者向けステップバイステップガイド
- 必要な道具を準備する
- 研磨ホイールやパッド、さまざまな粒度の研磨剤を用意。
- 清掃用クロス、保護具(手袋・ゴーグル)を準備。
- ステンレスの表面を確認
- 初期状態を把握し、大きな傷や凹みがあれば補修しておく。
- 粗研磨を行う
- 粗めの研磨剤を使用し、全体を均一に磨く。
- 研磨の方向を一定に保つことで均一な仕上がりが得られる。
- 中研磨で滑らかに仕上げる
- 細かい傷を消すため、粒度を上げた研磨剤で再度磨く。
- 仕上げ研磨を丁寧に実施
- 鏡面仕上げ用のバフや非常に細かい研磨剤を使い、光沢を出す。
- 最終仕上げと清掃
- 研磨剤を拭き取り、表面を保護するコーティング剤を塗布。
SUS 研磨仕上げのコツ
ポイント | 詳細 |
---|---|
研磨方向を統一 | 研磨中に方向を統一することで、均一な表面仕上げを実現できます。 |
粒度を徐々に上げる | 粒度の粗いものから細かいものへと順番に変更することで、滑らかな仕上がりが得られます。 |
過度な力を避ける | 強い力を加えると傷が深くなったり、熱変形の原因になるため注意が必要です。 |
清掃をこまめに行う | 研磨剤や削りカスを除去することで、次の工程がスムーズに進みます。 |
適切な工具を選ぶ | 仕上げの粒度や作業範囲に応じて適切な工具を選ぶことで作業効率が向上します。 |
全体のまとめ
ステンレスの鏡面仕上げを成功させるためには、以下の点を押さえてください:- 計画的な研磨工程を設定し、工程ごとに適切な工具と材料を使用。
- 丁寧な作業を心がけ、焦らずに進めること。
- 研磨方向や粒度の変更を段階的に行うことで、滑らかかつ美しい仕上がりを実現。
鏡面磨きでの失敗と修正方法
よくある鏡面磨きの失敗例
失敗例 | 原因 |
---|---|
表面に深い傷が残る | 粗い研磨剤を使用した後に、中研磨や仕上げ研磨を十分に行わなかった。 |
研磨跡が不均一 | 研磨方向がバラバラだったり、研磨圧力が一定でなかった。 |
表面が曇る | 適切な粒度の研磨剤を使用しなかったか、仕上げのバフが不十分だった。 |
熱変形が起きる | 研磨時に過度の力を加えたり、研磨速度が速すぎた。 |
仕上げに汚れが残る | 研磨剤や削りカスをきちんと拭き取らなかった。 |
失敗を修正する方法
修正手順 | 詳細 |
---|---|
傷を修正する | 深い傷がある場合は、もう一度粗研磨からやり直し、徐々に粒度を上げて仕上げる。 |
研磨跡を均一にする | 一方向に磨くようにし、圧力を一定に保ちながら再研磨する。 |
曇りを取り除く | 仕上げ研磨で#800以上の細かい研磨剤や高品質のバフを使用する。 |
熱変形を防ぐ | 研磨時の圧力を軽減し、作業を中断して冷却を挟む。 |
汚れを除去する | 清掃クロスで表面をしっかり拭き取り、最後に保護コーティング剤を塗布する。 |
失敗から学ぶ研磨のポイント
- 適切な粒度の選定
- 初めから粗すぎる粒度を使用しない。
- 粒度を徐々に上げていくことで、効率よく傷を取り除く。
- 研磨方向を一定に保つ
- 磨く方向を統一することで、ムラのない美しい仕上がりを実現。
- 力加減と研磨時間の調整
- 過度な力や高速作業は避ける。
- 適切な圧力と十分な時間をかけて磨く。
- 作業中の清掃を忘れない
- 研磨剤や削りカスが表面に残らないよう、工程ごとに清掃を行う。
- 作業環境を整える
- 十分な照明と作業スペースを確保し、失敗を未然に防ぐ。
まとめ
鏡面磨きは繊細な作業ですが、失敗を修正するための対策を理解し、ポイントを押さえれば誰でも高品質な仕上げが可能です。失敗から学び、計画的に作業を進めましょう。ステンレス用鏡面仕上げ剤の選び方
鏡面仕上げ剤の種類
種類 | 特徴 | 主な用途 |
---|---|---|
コンパウンドタイプ | 微細な研磨粒子が含まれており、細かい傷や曇りを除去する。 | 最終仕上げや光沢出しに適している。 |
液体ポリッシュ | 液体状で使いやすく、軽い研磨作業や日常のメンテナンスに便利。 | 小規模な傷や曇りの除去。 |
ペースト状ポリッシュ | 粘度が高く、研磨力が強い。深めの傷や曇りを除去する際に使用。 | 初期段階の傷補修に適している。 |
ワックス系コーティング剤 | 光沢を保つための保護膜を形成する。研磨後の仕上げに使用すると効果的。 | 鏡面仕上げ後の保護用。 |
鏡面仕上げ剤の適切な使用方法
ステップ | 方法 | 注意点 |
---|---|---|
表面を清掃する | 研磨剤を塗布する前に表面の汚れや油分をしっかり取り除く。 | 汚れが残ると研磨剤がムラになりやすい。 |
少量を塗布する | 必要最低限の量を柔らかい布やスポンジに取り、表面に均一に広げる。 | 過剰な量は作業効率を下げる。 |
一定方向に磨く | 強く押し付けず、一定方向に均一な圧力で磨く。 | 力を入れすぎると表面に傷を付ける可能性がある。 |
研磨後に拭き取る | 研磨剤を完全に拭き取り、必要に応じて再度仕上げる。 | 残留物が表面に曇りを生じさせる場合がある。 |
コーティングを施す | 最終的にワックスや保護剤を使用して表面を保護する。 | 塗布後はしっかり乾燥させる。 |
ポイント解説
- 用途に応じた研磨剤の選択
- 傷の深さや仕上げの段階に応じてコンパウンド、液体ポリッシュ、ワックスを選ぶ。
- 作業環境を整える
- 十分な照明と平らな作業台を用意し、均一に作業できる環境を整える。
- 適切な道具を使用する
- 柔らかい布、専用スポンジ、または適切なバフを選び、表面を傷つけないようにする。
バフ研磨による鏡面仕上げ
バフ研磨の基本
項目 | 説明 |
---|---|
目的 | 表面を滑らかにし、光沢を持たせる。 |
使用する道具 | バフホイール、研磨剤(コンパウンド)、研磨機(電動または手動)。 |
特徴 | ステンレスやアルミニウムなどの金属に適用できる。作業が適切であれば鏡面のような仕上がりを得られる。 |
バフ研磨の手順
ステップ | 方法 | 注意点 |
---|---|---|
1. 表面の清掃 | 作業前に表面の汚れや油分を完全に拭き取る。 | 汚れが残っているとバフホイールが目詰まりし、仕上がりに影響を与える。 |
2. 研磨剤の塗布 | バフホイールに適量の研磨剤を塗布する。 | 研磨剤が多すぎると作業効率が落ちる。 |
3. 粗研磨 | 中目のバフホイールを使用し、傷を徐々に消していく。一定方向に圧力をかけて磨く。 | 強く押し付けすぎない。表面に新たな傷を付ける原因となる。 |
4. 中研磨 | 細目のバフホイールに切り替え、表面をさらに滑らかにする。 | 適切な速度と圧力を維持する。 |
5. 最終研磨 | 最も細かい目のバフホイールを使用し、鏡面のような仕上げに磨き上げる。 | 常に均一な動作を心掛ける。 |
6. 残留物の拭き取り | 最後に布で研磨剤の残留物を拭き取り、完成した表面を確認する。 | 拭き残しがあると曇りが生じる可能性がある。 |
バフ研磨時の注意点
項目 | 注意点 |
---|---|
研磨剤の選定 | 使用する金属に適した研磨剤を選ぶことが重要。 |
バフホイールの清潔さ | 使用後はバフホイールを清掃し、目詰まりを防ぐ。 |
速度調整 | 研磨機の速度を適切に調整し、高速過ぎる場合は表面が焼ける可能性がある。 |
安全対策 | 防塵マスクや保護メガネを着用し、研磨中に発生する粉塵や飛散物から目や鼻を保護する。 |
作業環境 | 十分な換気を確保し、滑りにくい安定した作業台で行う。 |
ポイント解説
- 効率的な手順の選択
- 初めは粗い研磨から始め、段階的に細かい研磨へ進むことで効率よく仕上げることができます。
- 均一な動きの重要性
- バフを動かす速度や方向が不均一になると仕上がりにムラが出るため、注意が必要です。
- 適切な研磨剤の使用
- 金属の種類に応じて、専用の研磨剤を選ぶことで最良の結果を得ることができます。
ステンレス板の鏡面研磨に使える研磨剤
研磨剤の種類と特徴
研磨剤の種類 | 特徴 |
---|---|
粗目研磨剤 | 初期段階の研磨で使用。表面の大きな傷や不純物を取り除き、均一な状態に仕上げる。 |
中目研磨剤 | 粗目研磨後に使用し、さらに表面を滑らかにして細かな傷を取り除く。 |
細目研磨剤 | 最終段階で使用し、鏡面仕上げを実現するために表面を光沢のある状態に仕上げる。 |
ダイヤモンド研磨剤 | 高精度な仕上げが可能で、ステンレスなどの硬い金属にも適用可能。微細な研磨ができる。 |
ステンレス板専用の研磨剤
研磨剤の種類 | 特徴 |
---|---|
ステンレス用研磨剤 | ステンレスの特性に合わせた研磨剤で、汚れやサビの除去ができ、金属表面を滑らかに仕上げることができる。 |
シリコンカーバイド研磨剤 | ステンレスに適した強力な研磨剤で、表面を滑らかにしつつ効率的に研磨。 |
研磨コンパウンド | 微粒子を使って高い光沢を出すことができるため、鏡面仕上げに最適。多様な粒度が揃っており用途に応じて選べる。 |
研磨剤の選び方と使用方法
ポイント | 詳細 |
---|---|
用途に合わせた研磨剤選び | 初期研磨では粗目、中間研磨で中目、最終仕上げには細目やダイヤモンド研磨剤を選ぶ。 |
ステンレス専用の研磨剤使用 | ステンレスの特性に合った専用研磨剤を使うことで、効率的に鏡面仕上げが可能。 |
粒度の調整 | 研磨の進行具合に応じて粒度を調整し、傷を最小限に抑えて滑らかな表面を作る。 |
研磨剤の適切な量 | 研磨剤を適量使用することが重要。多すぎると表面が曇り、少なすぎると効果が薄い。 |
研磨の圧力と速度 | 過度な圧力をかけず、一定の速度で研磨することが大切。強い圧力は金属にダメージを与える場合がある。 |
ポイント解説
- 粒度と研磨段階
- 粗目から細目にかけて段階的に研磨することで、均一な仕上げが可能となります。最終仕上げで鏡面を作り出すためには、細かい粒度の研磨剤を使用することが重要です。
- 研磨剤の適切な量
- 研磨剤が多すぎると、研磨作業が効率的でなくなり、逆に仕上がりに影響を与える可能性があるため、適量を使用することが大切です。
- 専用研磨剤の使用
- ステンレス専用の研磨剤を使うことで、金属表面の特性に合わせた最適な仕上げが可能です。金属に合わせた研磨剤を選び、作業を効率よく進めましょう。
ステンレスの美しさを最大限に!SUSの研磨仕上げの基本とテクニック
SUSの研磨仕上げの魅力と基本
項目 | 内容 |
---|---|
ステンレスの特性と研磨の重要性 | SUS(ステンレス)は耐食性、耐久性、美観に優れており、研磨によりその特性がさらに引き立ちます。 |
研磨仕上げとは | 表面を滑らかにし、目的に応じた光沢や模様を施す加工技術です。 |
鏡面仕上げとヘアライン仕上げの違い | 鏡面仕上げは光沢のある反射性の高い表面、ヘアライン仕上げは細い直線模様のマットな表面を実現します。 |
ステンレスの特性と研磨の重要性
- 耐食性の向上:
- ステンレスはもともと高い耐食性を持つが、研磨することで微細な傷を取り除き、腐食のリスクをさらに低減。
- 美観の向上:
- 光沢や模様を施すことで、製品のデザイン性を向上。
- 用途の広がり:
- 研磨仕上げにより、建築資材、装飾品、医療機器など多様な分野で利用可能。
研磨仕上げとは
- 研磨の目的:
- 表面を平滑にし、特定の仕上がりを得ることで、耐久性や美観を向上。
- 研磨のプロセス:
- 粗磨きから始めて、目の細かい砥石やペーパーで段階的に仕上げ。
- 仕上がりのバリエーション:
- 鏡面、ヘアライン、バフ仕上げなど多彩な仕上げ方法が存在。
鏡面仕上げとヘアライン仕上げの違い
特徴 | 鏡面仕上げ | ヘアライン仕上げ |
---|---|---|
見た目 | 鏡のような反射性の高い光沢面 | 細い直線模様が均一に入ったマットな表面 |
用途 | 装飾品、建築内装、医療機器 | 建築外装、厨房機器、機械カバー |
加工難易度 | 高い:研磨工程が複雑で丁寧さが要求される | 中程度:均一な模様を出すための技術が必要 |
メンテナンス | 高い光沢を保つため定期的な清掃が必要 | 汚れや指紋が目立ちにくく、比較的簡単 |
鏡面仕上げの方法
項目 | 内容 |
---|---|
鏡面仕上げの手順 | 鏡面仕上げは段階的な研磨工程を経て、光沢を出す加工方法です。粗磨きから始め、細かい研磨を行います。 |
研磨剤の種類と選び方 | 研磨剤の種類は研磨の目的や素材に応じて選びます。細かい粒度の研磨剤を使用することで高い光沢を得ます。 |
研磨仕上げの基本とテクニック | 鏡面仕上げは丁寧に研磨を重ねることが重要。適切な研磨圧とスピードで、均一な仕上がりを実現します。 |
鏡面仕上げの手順
- 粗磨き:
- 初めに粗い研磨剤を使用し、表面の大きな傷や不均一を取り除きます。
- 中研磨:
- 次に中程度の研磨剤で表面を平滑にし、細かい傷を除去します。
- 細研磨:
- 最後に非常に細かい研磨剤を使い、表面を滑らかにして光沢を出します。
- 仕上げ作業:
- バフ仕上げを行うことで、鏡面のような反射性の高い光沢を得ることができます。
研磨剤の種類と選び方
- 粗研磨剤:
- 例:アルミナ、シリコンカーバイドなど。主に表面の大きな不均一や傷を取り除くために使用。
- 中研磨剤:
- 例:酸化アルミニウム、ダイヤモンドペーストなど。次の段階での細かい傷を除去するために使用。
- 細研磨剤:
- 例:酸化鉄、ダイヤモンドスラリーなど。仕上げ用で、微細な傷を取り、最終的な光沢を出すために使用。
研磨仕上げの基本とテクニック
- 均一な圧力をかける:
- 研磨作業中は均一な圧力を維持し、仕上がりにムラが出ないように注意します。
- スピードと角度の調整:
- 研磨時のスピードや角度を調整することで、研磨剤の効果を最大化し、均一な光沢を出すことができます。
- 研磨液の使用:
- 研磨液を使うことで、研磨中に発生する熱を抑え、仕上がりを向上させることができます。
ステンレスとアルミのヘアライン研磨
項目 | 内容 |
---|---|
ヘアライン研磨の基礎知識 | ヘアライン研磨は、細かな線状の仕上げ模様を作る技術です。耐久性を高め、光沢を加えることができます。 |
ステンレスとアルミの扱い方の違い | ステンレスとアルミでは研磨方法に微妙な違いがあり、材質ごとの適切な研磨を行うことが重要です。 |
ヘアライン研磨の基礎知識
- 目的:
- ヘアライン研磨は、表面に均一な細かい線を作り出し、光沢感を与える仕上げ方法です。
- 特に装飾的な目的や表面強度を向上させるために使用されます。
- 使用する工具:
- ベルトサンダーや研磨機、研磨パッドなどを使用して、均等な線を作り上げます。
- 研磨剤は粒度の異なるものを順番に使用し、粗いものから細かいものへと段階的に磨きます。
- 仕上がり:
- ヘアライン仕上げは、細い線模様が均一に表面に現れるため、表面の光沢を増し、美しい外観を作り上げます。
ステンレスとアルミの扱い方の違い
- ステンレスの研磨:
- ステンレスは硬度が高く、研磨時に熱が発生しやすいため、冷却液や研磨液を使い、温度を管理することが重要です。
- ステンレスのヘアライン仕上げは、サビや汚れを防ぐための耐久性を高める効果があります。
- アルミの研磨:
- アルミはステンレスよりも柔らかいため、研磨時に傷がつきやすいですが、仕上げが比較的簡単です。
- 研磨中にアルミの酸化膜が壊れやすいので、酸化防止のために適切な研磨液を使用することが推奨されます。
- 違いのポイント:
- ステンレスは研磨中に熱や圧力に強い注意が必要ですが、アルミは柔らかいため、細かい粒度の研磨剤を使用して表面の傷を防ぐ必要があります。
- 両者ともに研磨の最後には仕上げ作業が必要で、十分な冷却と適切な研磨剤選定が重要です。
よくある質問とトラブルシューティング
項目 | 内容 |
---|---|
研磨に関するFAQ | 研磨作業でよく聞かれる質問をまとめました。 |
研磨中のトラブルとその解決策 | 研磨作業中に発生することのあるトラブルと、それを解決するための方法を紹介します。 |
研磨作業の効率を上げるコツ | 研磨作業の効率を改善し、仕上がりを良くするための実践的なアドバイスを提供します。 |
研磨に関するFAQ
- 研磨剤の選び方は?
- 研磨剤は研磨対象の材質に適したものを選びましょう。例えば、金属には金属用の研磨剤を、プラスチックにはプラスチック専用のものを使います。
- ヘアライン仕上げと鏡面仕上げの違いは?
- ヘアライン仕上げは、細い線状の模様が特徴で、鏡面仕上げは光沢感が強く、反射率の高い仕上がりになります。
- どのくらいの圧力で研磨すべきか?
- 研磨中は過度な圧力をかけず、均等に力を入れて作業することが重要です。圧力が強すぎると研磨剤が早く摩耗し、仕上がりが悪くなることがあります。
研磨中のトラブルとその解決策
- 表面に傷がついてしまった
- 解決策: より細かい粒度の研磨剤を使い、再度均等に研磨します。また、研磨中の圧力を調整し、傷がつかないように注意します。
- 研磨剤がすぐに消耗してしまう
- 解決策: 研磨剤の使用量を減らし、適切な速度で作業を行うことを心がけます。冷却液や研磨液を使用することで研磨剤の寿命を延ばせます。
- 研磨後の表面が光沢を持たない
- 解決策: 研磨作業を順番に段階的に進め、粒度を細かくしていくことで、最終的な仕上がりが光沢を持つようになります。
研磨作業の効率を上げるコツ
- 均等な圧力をかける
- 研磨中に均等な圧力をかけることで、表面の仕上がりが均一になります。また、圧力をかけすぎると研磨剤が早く摩耗し、効率が下がります。
- 適切な速度で作業を進める
- 研磨機の回転速度や作業速度を適切に調整することで、効率的に作業を進められます。過度なスピードは逆に仕上がりを悪くします。
- 冷却液を使用する
- 研磨作業中に冷却液を使うことで、研磨剤の摩耗を遅らせ、表面の温度上昇を防ぐことができます。これにより、作業効率が向上し、仕上がりも改善されます。
まとめ
ステンレスの表面仕上げにおいて、SUS研磨は美しい仕上がりを実現するための基本となります。研磨作業は、表面の均一な仕上げや傷を取り除くことで、ステンレスの美しさを最大限に引き出します。また、適切な研磨テクニックを用いることで、光沢感や耐久性を向上させることが可能です。 研磨作業の際には、適切な研磨剤と柔らかい布を使用することが重要です。また、作業中には一定の圧力と速度で行うことで、均一な仕上がりを実現します。さらに、途中で布を交換することで、きれいな仕上がりを保つことができます。このような基本的なテクニックをマスターすることで、SUS研磨によるステンレスの美しい仕上がりを実現することができます。「SUS鋼材入門!素材の特性と選び方ガイド」
鉄鋼の一種であるSUS鋼材は、その特性や選び方について知っておくことが重要です。工業製品や建築物など、さまざまな分野で使用されているSUS鋼材は、どのような特性を持ち、どのように選ぶべきなのでしょうか。
本ガイドでは、SUS鋼材の基本的な特性や選び方について詳しく解説します。SUS鋼材の特性を理解することで、適切な素材を選ぶ際に役立つ情報を提供します。さらに、素材の選び方に関する具体的なガイドも紹介しますので、初心者から上級者まで幅広いニーズにお応えできる情報となっています。
SUS鋼材について知識を深め、正しく選ぶためのヒントを手に入れましょう。読み進めることで、SUS鋼材の世界が広がり、工作や製品開発においてより良い選択をすることができるかもしれません。
Contents
SUS鋼材入門とは
SUS鋼材とは何か
SUS鋼材は、ステンレス鋼の一種です。ステンレス鋼は、錆びずに長持ちする特性を持ちます。SUSとは、Steel Use Stainless(ステンレス鋼使用)の略称であり、日本工業規格(JIS)で規定されています。このため、耐食性や耐熱性が高く、さまざまな用途に使われています。例えば、キッチン用品や建築材料、医療機器などに広く使用されています。
SUS鋼材を選ぶ際には、用途に応じて適切な材質や形状を選ぶことが重要です。例えば、食品加工業では食品衛生法に適合したSUS材を選ぶ必要があります。また、外部環境にさらされる場合は耐候性を考慮する必要があります。
要するに、SUS鋼材は高い耐久性と使い勝手の良さからさまざまな産業で利用されています。適切な選び方をすることで、効果的に活用することができます。
SUS鋼材の歴史と発展
SUS鋼材は、日本の鉄鋼製品の一つであり、その歴史と発展には興味深い要素があります。SUSは”Stainless Steel”の略語であり、その特性として錆びにくさや耐食性が挙げられます。このような特性から、食品加工業や建設業など幅広い産業で利用されています。
SUS鋼材の選び方においては、用途に応じた強度や耐久性が重要です。例えば、食品加工業では清潔さが求められるため、表面の仕上げが滑らかであることが重要となります。また、海洋環境で使用する場合は塩害に強いSUS材が選ばれることが一般的です。
SUS鋼材は、その特性や選び方を理解することで、効果的に使用することができます。産業界において欠かせない素材として、今後も注目を集めることが期待されます。
ステンレス鋼と他の金属材料との比較
SUS鋼材は、耐食性に優れた素材として広く使われています。他の金属材料と比較すると、SUS鋼は錆びにくく、強度も高い特性を持っています。例えば、SUS鋼は家庭用品から建築材料まで幅広い分野で使用されており、その信頼性が高く評価されています。日本では特に、食品や医療機器などの分野でSUS鋼の需要が高まっています。このように、SUS鋼は多くの産業において重要な素材として使われています。そのため、SUS鋼材を選ぶ際には、その耐久性や特性をしっかりと理解し、適切な用途に使用することが重要です。要するに、SUS鋼はその優れた性能と広範な用途で、他の金属材料と比較して優れた選択肢となっています。
ステンレス鋼の基本的な特性
耐食性
SUS鋼材は、その耐食性が特徴的です。この耐食性は、錆びや腐食から素材を守る働きがあります。日本では、海洋気候や工業地域など、腐食が進む環境が多いため、耐食性が重要視されています。例えば、食品加工業界では、SUS鋼材が衛生的で清潔な状態を保つのに適しているため重宝されています。また、建築や自動車部品など幅広い分野で使用されており、その信頼性が評価されています。このように、SUS鋼材の耐食性はさまざまな産業で重要な役割を果たしています。耐食性を考慮して素材を選ぶ際には、SUS鋼材の特性を理解し、適切に選定することが大切です。
強度と硬度
SUS鋼材について知っておくべきことを解説します。SUS鋼材は強度と硬度に優れており、さまざまな用途に使用されます。例えば、建築や自動車産業ではその耐久性が評価されています。また、食品加工業界でも衛生的な特性から広く利用されています。このように、SUS鋼材は幅広い分野で重要な役割を果たしています。
厳選した素材を選ぶ際には、使用目的や環境に適した品質や強度を考慮することが重要です。例えば、耐食性が求められる場合はSUS316を選ぶと良いでしょう。選び方を間違えると、使用する材料が適していない可能性があるため、専門家のアドバイスを受けることをお勧めします。
SUS鋼材は多くの業界で重要な素材として使われており、その特性を理解することで適切に選ぶことができます。
熱耐性
SUS鋼材は、その素材の特性や選び方を知ることが重要です。SUS鋼材は、耐熱性に優れており、高温下で安定した性能を発揮します。例えば、熱処理や溶接など、高温環境で使用される場面で活躍します。このような特性から、自動車部品や工業機械の製造など、幅広い産業で使用されています。選び方のポイントは、使用環境や耐久性の要件に合わせて最適な種類を選択することです。素材の選択が適切でないと、耐熱性や耐食性などの性能が低下し、機能が損なわれる可能性があります。したがって、適切なSUS鋼材を選ぶことで、製品の性能向上や耐久性強化につながります。
衛生的な特性
SUS鋼材は、様々な用途に適した素材です。SUSはステンレス鋼の国際規格記号で、耐食性に優れ、錆びにくい特性があります。そのため、食品加工業や医療機器などの衛生面が重要な分野で広く使用されています。工業製品や建築材料にも利用され、耐久性が求められる環境で優れた性能を発揮します。
SUS鋼材の選び方においては、使用目的に応じて適切な種類を選定することが重要です。例えば、SUS304は一般的なステンレス鋼であり、一般的な用途に適しています。一方、SUS316はより耐食性に優れたタイプであり、塩水環境や化学物質にさらされる場所に適しています。
選ぶ際には、使用環境や耐久性などを考慮し、適切なSUS鋼材を選ぶことで、長期間安定した性能を期待することができます。
加工性と溶接性
SUS鋼材は、加工性と溶接性が重要な特性です。加工性とは、金属を加工する際の容易さを表します。SUS鋼は硬度が高く、熱処理する必要がないため、比較的容易に加工できます。これにより、様々な形状やサイズに加工することが可能となります。一方、溶接性は、金属同士を溶接する際の性質を指します。SUS鋼は溶接性に優れており、強固な溶接が可能です。
例えば、自動車のボディパーツや建築構造物など、幅広い用途にSUS鋼が利用されています。これは、その加工性と溶接性が高いためです。加工性と溶接性が優れていることから、SUS鋼はさまざまな産業分野で重要な素材として活躍しています。そのため、適切な条件での加工や溶接により、SUS鋼の性能を最大限に引き出すことができるのです。
ステンレス鋼の種類と特徴
オーステナイト系ステンレス鋼
SUS鋼材入門!素材の特性と選び方ガイド
ステンレス鋼は、耐食性に優れ、錆びにくい素材として知られています。その中でも、オーステナイト系ステンレス鋼は一般的な素材です。オーステナイト系ステンレス鋼は、非磁性であり、加工性や溶接性に優れています。また、耐熱性も高く、食器や建築材料など幅広い用途で使用されています。
例えば、キッチン用具や食器などで、錆びにくさや衛生面が重視される場面でオーステナイト系ステンレス鋼が使用されます。また、建築材料としても、外観の美しさや耐久性を求める場面で重宝されています。
素材選びの際には、使用環境や目的に応じて適切な種類のステンレス鋼を選ぶことが大切です。耐食性や耐熱性などの特性を理解し、適切に選ぶことで長持ちする製品を作ることができます。
フェライト系ステンレス鋼
SUS鋼材は、日本の建築や製造業で幅広く利用されている素材です。フェライト系ステンレス鋼は、その中でも一般的なタイプの一つです。この鋼材は耐食性に優れ、錆びにくい特性があります。また、磁性があるため、磁石を使う機器や部品にも適しています。
フェライト系ステンレス鋼は、キッチン用品や建築材料など幅広い分野で利用されています。例えば、キッチンの調理器具やシンク、さらには建物の外装などにも使用されています。その耐久性や使い勝手の良さから、多くの人々に信頼されています。
このように、フェライト系ステンレス鋼は様々な用途に適しており、その特性から幅広い分野で重要な役割を果たしています。これからも、SUS鋼材の選び方を理解し、適切に活用することが、さらなる発展につながるでしょう。
マルテンサイト系ステンレス鋼
マルテンサイト系ステンレス鋼は、強度と耐摩耗性に優れています。これは、炭素を多く含むためです。例えば、包丁や工業用の刃物などの製品に使用されています。熱処理によって硬度を調整できるので、さまざまな用途に適しています。マルテンサイト系ステンレス鋼は、刃先が長持ちするため、切れ味が良く、作業効率が向上します。耐食性が低いため、湿気や酸にさらされる環境では、定期的なお手入れが必要です。このように、マルテンサイト系ステンレス鋼は、その特性からさまざまな産業で重宝されています。
デュプレックス(二相)ステンレス鋼
SUS鋼材は、日本の工業製品や建築に幅広く使われている素材です。その中でも、デュプレックス(二相)ステンレス鋼は注目されています。この素材は、耐食性や強度に優れているため、海洋環境や化学工業など厳しい環境下で使用されることが多いです。
デュプレックスステンレス鋼は、クロムやニッケルなどの合金を適切な割合で含むことで、通常のステンレス鋼よりも優れた性能を持っています。例えば、海水中での腐食に強く、強度も高いため、海洋プラントや海底パイプラインなどで重要な役割を果たしています。
このように、デュプレックスステンレス鋼は厳しい環境下で高い性能を発揮する素材として、さまざまな産業で活躍しています。その特性を理解し、適切に選ぶことで、安全性や耐久性を確保しながら、効果的に利用することができます。
耐熱ステンレス鋼
SUS鋼材は様々な用途で使われる耐熱ステンレス鋼の一種です。この素材は熱に強く、耐食性に優れています。例えば、高温での加工や化学薬品にさらされる環境でも優れた性能を発揮します。自動車部品、建築材料、調理器具など幅広い分野で利用されています。
SUS鋼材を選ぶ際には、使用環境や耐久性などを考慮することが重要です。例えば、熱や腐食に対する耐性が必要な場合は、SUS316が適しています。一方、一般的な用途にはSUS304が使われることが多いです。
耐熱ステンレス鋼の特性を理解し、適切に選ぶことで、耐久性や安定性を確保できます。そのため、SUS鋼材を使用する際には、用途に合った適切な種類を選ぶことが重要です。
ステンレス鋼の選び方と用途別ガイド
選び方の基本
「SUS鋼材入門!素材の特性と選び方ガイド」
SUS鋼材の選び方を理解する際には、その特性に注意を払うことが重要です。SUS鋼は耐食性に優れ、錆びにくいという特性を持っています。この特性から、食品加工業や建築業など幅広い分野で利用されています。例えば、食品加工ラインや海洋施設、外装部材などに広く採用されています。
SUS鋼の中でも、SUS304やSUS316などが一般的に使われており、それぞれの特性や用途によって適したタイプを選ぶことが重要です。例えば、SUS304は一般用途に向いており、SUS316は耐食性が求められる場面で適しています。
適切なSUS鋼材を選ぶことで、長期的な耐久性や効率的な利用が期待できます。素材の特性を理解し、適切な選択をすることが大切です。
用途と適合するSUS鋼材の種類
SUS鋼材は、さまざまな用途に適した素材です。例えば、建築や自動車産業、食品加工機械などの分野でよく使用されています。SUS鋼材の特性としては、耐食性や耐熱性、加工性などがあります。これらの特性により、様々な環境や条件下で信頼性の高い製品を生産することが可能です。たとえば、食品加工機械に使用されるSUS鋼材は、食品との接触に安全で、清潔な状態を保つことができます。建築業界では、外部の気候条件に耐える耐食性が重要となります。
選び方のポイントとしては、使用する環境や目的に合わせて適切なSUS鋼材を選定することが重要です。例えば、耐食性が求められる場合はSUS304を選ぶなど、適合する種類を選ぶことが大切です。これらの特性や選び方を理解することで、製品開発や製造において効果的に活用することができます。SUS鋼材は、その特性と多様な種類から、様々な産業分野で重要な役割を果たしています。
表面仕上げとその影響
「SUS鋼材入門!素材の特性と選び方ガイド」
SUS鋼材は、耐久性に優れ、錆びにくい特性があります。これは、日本の工業製品や建築分野で広く使用されている理由です。例えば、キッチン用具や自動車部品、建物の外装などで活用されています。
SUS鋼材を選ぶ際には、用途に合った強度や耐久性を考慮する必要があります。例えば、外部装飾には耐候性が重要ですが、食品加工機器には耐蝕性が重要です。適切なSUS鋼材を選ぶことで、製品や建築物の品質や耐久性を向上させることができます。
選び方を間違えると、劣化や事故のリスクが高まる可能性があります。そのため、専門家の意見を聞いたり、用途に適したSUS鋼材を選ぶ際には慎重に検討することが重要です。SUS鋼材の適切な選定は、製品や建築物の安全性を確保する上で欠かせません。
コストパフォーマンスを考慮した選び方
SUS鋼材は、様々な用途に使用される素材であり、その選び方を考える際にはコストパフォーマンスを重要視することがポイントです。例えば、SUS304は一般的に耐食性に優れているため、食品加工業や建築業で広く使用されています。一方、SUS316はSUS304よりも耐食性が高く、海洋環境や化学プラントなど厳しい環境下での使用に適しています。また、SUS430は耐熱性に優れており、熱交換器や燃焼炉などの高温環境で使用されることが多いです。
素材の特性を把握し、使用する環境や条件に適したSUS鋼材を選ぶことが重要です。コストパフォーマンスを考慮しながら、適切なSUS鋼材を選ぶことで、効率的な素材活用が可能となります。
購入時のチェックポイント
SUS鋼材は、素材の特性や選び方を理解することが重要です。SUSはステンレス鋼の種類の一つであり、耐食性や強度に優れています。選ぶ際には、用途や環境に適したタイプを選定することが大切です。
例えば、食品加工業界ではSUS304が一般的に使用されます。これは錆びにくく衛生的な特性があるためです。一方、建築業界ではSUS316が好まれます。これは海水などの腐食性環境に強いためです。
さらに、SUS鋼材の表面処理も重要です。鏡面仕上げやサテン仕上げなど、見た目や機能に影響を与えます。適切な素材と仕上げを選ぶことで、耐久性や美観を保つことができます。要するに、適切なSUS鋼材を選ぶことで、長期間安心して利用することができるのです。
SUS鋼材の加工とメンテナンス
加工方法と注意点
SUS鋼材は、様々な用途に使われる耐食性の高い素材です。その特性や選び方について理解することは重要です。SUS鋼材の特性は、耐蝕性や強度に優れており、食品加工機械や建築材料など幅広い分野で使用されています。選ぶ際には、使用環境や耐久性の要求に合わせて適切な種類を選ぶことが大切です。例えば、海洋環境では耐食性が求められるため、適切なSUS鋼材のグレードを選定する必要があります。その他、加工方法や注意点も重要です。適切な加工方法を選択することで、素材の特性を最大限に生かすことができます。素材の特性や選び方を理解し、適切に取り扱うことで、安全性や耐久性を確保することができます。
メンテナンスと清掃のヒント
SUS鋼材は、様々な用途において重要な素材です。その特性や選び方を理解することは、適切な使用やメンテナンスに役立ちます。SUS鋼材は耐食性に優れ、食品業界や建築業界で広く使用されています。例えば、食品加工機器やキッチン用品などでその重要性が高く評価されています。選び方のポイントとしては、使用する環境や耐久性の必要性を考慮することが重要です。さらに、適切なメンテナンスを行うことで、長い間効果的に利用することができます。SUS鋼材の選択とメンテナンスは、安全性や耐久性を確保するために欠かせない要素です。しっかりとした知識を持ち、適切な対処を行うことで、効果的に活用できることでしょう。
長期的な耐久性を保つコツ
SUS鋼材は、その耐久性や強度などの特性から様々な用途で利用されています。例えば、建築や自動車産業、キッチン用具など幅広い分野で活躍しています。SUS鋼材を選ぶ際には、使用する環境や目的に合わせて適切な種類を選ぶことが重要です。 例えば、外部で使用する場合は耐候性を考慮し、食品加工業で使用する場合は衛生面を重視した素材を選ぶ必要があります。また、SUS304やSUS316などの種類によっても特性が異なるため、使用する場面に応じて適切なものを選びましょう。適切に選ぶことで、長期間にわたり安定した性能を保つことができます。SUS鋼材の選び方を理解することで、より効果的に利用することができます。
よくある質問と誤解
SUS鋼材に関する誤解と真実
SUS鋼材に関する誤解と真実
SUS鋼材に関する誤解が存在しますが、実際にはその特性や選び方について理解することが重要です。SUS鋼材はステンレス鋼の一種であり、耐食性や耐熱性に優れています。これにより、食品加工業や建築業など幅広い分野で使用されています。
選び方のポイントとしては、使用環境や目的に応じて適切なSUS鋼材を選ぶことが重要です。例えば、耐食性が求められる場合にはSUS316が適しています。また、外観にもこだわりたい場合には鏡面仕上げのSUS304が選択肢の一つとなります。
SUS鋼材はその特性により、様々な産業で重要な役割を果たしています。正しい情報を知ることで、SUS鋼材を活用する際に役立つ選択ができるでしょう。
選択時のよくある疑問
SUS鋼材とは、ステンレス鋼のことであり、その特性や選び方について解説します。SUS鋼材は耐食性や耐熱性に優れており、さまざまな用途に利用されています。例えば、キッチン用品や建物の外装、医療機器などに使用されています。特に、食品関連や薬品関連の産業では衛生面を考慮してSUS鋼材が重宝されています。
SUS鋼材を選ぶ際には、使用環境や耐久性、加工のしやすさなどを考慮する必要があります。材料の硬さや強度、耐食性などが重要な要素となります。さらに、デザイン性やコスト面も検討することが大切です。適切なSUS鋼材を選ぶことで、長期間にわたり安定した性能を発揮し、さまざまな産業で活躍することができます。
専門家によるアドバイス
「SUS鋼材入門!素材の特性と選び方ガイド」
SUS鋼材はさまざまな用途に使われる素材です。その特性や選び方を理解することは重要です。例えば、SUS鋼材は耐食性に優れており、食品加工業や建築業界で広く使用されています。また、磁性がないため、精密機器の製造にも適しています。
選び方においては、使用する環境や条件を考慮する必要があります。例えば、外部での使用には耐候性が重要です。また、強度や耐熱性も重要な要素です。適切なグレードと厚さを選ぶことで、最適な素材を選ぶことができます。
SUS鋼材を選ぶ際には、目的に合った特性や適切な厚さ、グレードを選ぶことがポイントです。適切な選択をすることで、製品や構造物の耐久性や安全性を高めることができます。
ステンレス鋼の未来と持続可能性
環境への影響とリサイクル
SUS鋼材は、耐久性と耐食性に優れ、さまざまな産業で幅広く使用されています。この特性から、建築や自動車産業、食品加工業など多岐にわたる分野で重要な素材として活躍しています。例えば、食品加工業では、SUS鋼材が衛生管理や食品の加工に適しているため、衛生面や安全面での利点があります。
また、SUS鋼材の選び方について、使用する環境や用途に合わせて適切な種類を選ぶことが大切です。耐食性や強度、加工性などの特性を考慮し、最適な素材を選定することが重要です。例えば、屋外で使用する場合は耐久性が求められるため、適切な表面処理を施したSUS鋼材を選ぶことがポイントとなります。
このように、SUS鋼材はその特性や選び方によって、さまざまな産業で重要な役割を果たしています。
新しい技術と市場の動向
「SUS鋼材入門!素材の特性と選び方ガイド」
SUS鋼材は、さまざまな用途で使われる素材です。その特性や選び方を知ることで、より効果的に利用できます。
まず、SUS鋼材の特性について考えてみましょう。SUS鋼は耐食性に優れ、錆びにくい特性があります。このため、食品加工業や建設業などで幅広く使用されています。
次に、選び方のポイントを見てみましょう。使用する環境や目的によって適したSUS鋼の種類が異なります。例えば、屋外使用に適したものや高温に耐えるものなどがあります。
したがって、用途や環境に合わせて適切なSUS鋼材を選ぶことが重要です。素材の特性を理解し、選び方のポイントを押さえることで、効果的な利用が可能となります。
持続可能な開発とSUS鋼材の役割
持続可能な開発において、SUS鋼材は重要な素材として活躍しています。SUS鋼は耐食性に優れ、強度もあり、さまざまな産業で広く使用されています。例えば、建築業界では外壁や屋根にSUS鋼を用いることで、耐久性が向上し、長期間にわたってメンテナンスコストを抑えることができます。また、環境に優しい素材としても注目されており、リサイクルがしやすい特性も持っています。
さらに、SUS鋼は食品業界や医療機器製造業においても重要な役割を果たしています。その優れた耐食性や衛生性から、食品加工機器や医療器具などに広く利用されています。持続可能な開発を目指す上で、SUS鋼の特性を理解し適切に利用することが重要です。
まとめ
不動産投資は魅力的な投資先の一つとして考えられます。元手が少額でもレバレッジ効果によって投資効率を高めることが可能です。また、自己資金ゼロでもフルローンを利用する方法があります。不動産投資は融資を受けられるのが大きなメリットであり、これは株式や債券の投資とは異なる点です。初心者が不動産投資を始めるなら、区分マンションがおすすめです。物件価格が比較的安く融資も少額で済むため、返済の負担が抑えられます。頭金なしのフルローンも可能な投資用新築マンションの購入を検討してみてはいかがでしょうか。
「SUS鋼材とは何か?基本的な知識と活用方法を徹底解説」
SUS鋼材の基本情報
SUS鋼材とは
項目 | 詳細 |
---|---|
名称の由来 | SUSは「Steel Use Stainless」の略で、ステンレス鋼を指します。 |
定義 | 鉄にクロムやニッケルなどの元素を添加して、耐食性や耐熱性を向上させた合金鋼。 |
主な用途 | キッチン用品、自動車部品、建築材料、医療機器など広範な分野で使用されています。 |
SUS鋼材の主要な成分と役割
成分 | 含有量の例(%) | 主な役割 |
---|---|---|
鉄 (Fe) | 基本構成成分 | 鋼材の主要成分として、強度と加工性を提供。 |
クロム (Cr) | 10.5%以上 | 耐食性を向上させ、表面に不働態皮膜(酸化膜)を形成して腐食を防止。 |
ニッケル (Ni) | 8~12% | 耐食性をさらに強化し、延性や靭性を向上。 |
モリブデン (Mo) | 2~3%(一部) | 耐孔食性や耐酸性を向上(特に塩化物環境で効果的)。 |
炭素 (C) | 0.08%以下 | 強度を向上させるが、耐食性を低下させるため低含有量が推奨される(低炭素型ステンレス:例 SUS304L)。 |
SUS鋼材の特徴
- 耐食性:錆びにくく、過酷な環境下でも優れた性能を発揮。
- 加工性:成形しやすく、溶接や切削など多様な加工が可能。
- 耐熱性:高温環境下でも強度を保つため、工業用途で重宝される。
- 審美性:光沢のある表面仕上げが可能で、装飾用途にも使用。
ステンレス鋼の種類と特徴
ステンレス鋼の細分化された種類と特性
種類 | 細分類 | 主な特徴 | 用途例 |
---|---|---|---|
オーステナイト系 | 304系 | – 一般的な耐食性と加工性を持つ – 価格が比較的手頃 | 厨房機器、建築材料、医療器具 |
316系 | – モリブデン添加により耐孔食性が向上 – 塩化物環境に強い | 化学プラント、海洋構造物、食品加工設備 | |
321系 | – チタン安定化により高温下での耐クリープ性が向上 – 耐食性は304系と同等 | 高温環境での配管、航空機部品など | |
マルテンサイト系 | 410系 | – 耐摩耗性と加工性が高い – 耐食性は限定的 | 刃物、工具、バルブ部品 |
420系 | – 硬度が高く耐摩耗性に優れる – 耐食性は中程度 | メス、ハサミ、手術器具 | |
440系 | – 高硬度・高強度が特長 – 耐摩耗性が最も高いが加工は難しい | 精密ベアリング、計量機部品 | |
デュプレックス系 | 2205系 | – 高い耐孔食性と応力腐食割れ耐性 – 強度はオーステナイト系の約2倍 | 石油精製、海洋構造物、化学工業用途 |
2507系(スーパー系) | – 非常に高い耐食性 – コストは高め | 海洋設備、脱塩プラント | |
フェライト系 | 430系 | – 高い耐食性と低コスト – 溶接性は劣る | 家電部品、装飾用途、台所用シンク |
446系 | – 高温下でも耐酸化性が優れる – 耐食性も高い | ボイラー部品、排気系部品 | |
析出硬化系 | 17-4PH系 | – 高強度と耐食性のバランスが良い – 耐食性は304系以下 | 航空機部品、ポンプ、石油産業 |
各細分類の詳細比較
項目 | 304系 | 316系 | 321系 | 410系 | 2205系 |
---|---|---|---|---|---|
耐食性 | 高い | 非常に高い | 高い | 中程度 | 非常に高い |
強度 | 中程度 | 中程度 | 中程度 | 高い | 高い |
加工性 | 優れる | 優れる | 優れる | やや劣る | やや劣る |
耐孔食性 | 中程度 | 高い | 中程度 | 低い | 非常に高い |
添加元素 | クロム、ニッケル | クロム、ニッケル、モリブデン | クロム、ニッケル、チタン | クロム、炭素 | クロム、モリブデン、窒素 |
主な用途 | 一般用途、厨房用品 | 化学工業、海洋環境 | 高温用途 | 刃物、工具 | 石油産業、化学プラント |
細分化された種類の選択基準
条件 | 推奨する種類 | 理由 |
---|---|---|
耐孔食性が必要な場合 | 316系、2205系 | モリブデンや窒素の添加により塩化物環境でも安定した耐食性を発揮。 |
高硬度と耐摩耗性 | 440系 | 高い硬度と耐摩耗性を持ち、刃物やベアリングなどに最適。 |
高温用途 | 321系 | チタン安定化による高温耐性が求められる環境に適している。 |
低コストが重視 | 430系 | ニッケルを含まずコストを抑えつつ、耐食性を確保。 |
溶接性が必要な場合 | 304系、2205系 | 施工性と溶接後の安定性が求められる用途に対応可能。 |
ステンレス鋼の加工とメンテナンス
一般的な加工方法
加工方法 | 主な特徴 | 適用範囲 |
---|---|---|
切削加工 | – 高速工具を使用して加工可能 – 切削熱が発生しやすいため冷却が必要 | 複雑な形状や部品の製造 |
研削加工 | – 表面仕上げに最適 – 耐摩耗性の向上や寸法精度の確保 | 鏡面仕上げ、耐摩耗部品の加工 |
プレス加工 | – 成形性が高いオーステナイト系に適する – 高い圧力が必要 | 車両部品、建築用パネル |
溶接 | – TIG溶接、レーザー溶接などが一般的 – オーステナイト系は溶接後の耐食性が良い | 配管、タンク、構造物 |
鍛造 | – 高温で成形し強度を向上させる – 主にマルテンサイト系で使用 | 工具、軸受け、バルブ部品 |
エッチング | – 精密加工が可能 – 製品表面に模様や微細構造を付与 | 精密機器、装飾部品 |
メンテナンスのポイントと寿命
メンテナンス項目 | ポイント | 効果 |
---|---|---|
洗浄 | – 中性洗剤で洗浄 – 塩分や汚れを放置しない | 腐食の防止、外観の維持 |
点検 | – 表面状態や溶接部分を確認 – ひび割れや変色を早期発見 | 構造的な安全性の確保 |
保護処理 | – 必要に応じてパッシベーション処理 – 研磨剤や防錆剤を使用 | 耐食性の向上 |
環境管理 | – 酸や塩分が多い環境では適切なグレードを選択 – 使用環境を清潔に保つ | 素材寿命の延長 |
交換部品の確認 | – 高応力を受ける部品の摩耗や変形を確認 | 全体の性能維持、故障リスクの軽減 |
錆び取り完全ガイド!SUS素材の錆対策とメンテナンス方法
錆び。その見た目は美しくないし、素材を傷めることもある。そんな錆びに悩まされている方々に向けて、今回は「錆び取り完全ガイド」をご紹介します。SUS素材の錆対策やメンテナンス方法について詳しく解説します。
錆びは防げないものと思われがちですが、実際には適切なケアや対処法を知ることで防ぐことができます。この記事では、SUS素材を取り巻く錆びの問題に焦点を当て、どのように対策すればよいのか、どのようにメンテナンスを行えばよいのかについて分かりやすく解説します。
錆対策やメンテナンスについて正しい知識を身に付けることで、あなたの大切な素材を美しく保ち、長く使い続けることができます。さあ、一緒に錆対策の世界を探索し、素材を輝かせる方法を学んでいきましょう!
Contents
- ステンレスシンクのサビ落としと予防策
- ステンレス風呂の錆対策とメンテナンス
- ステンレスキッチンの錆びの原因と対策
- 浴槽のサビ補修とホーロー浴槽の特性
- ホーロー浴槽のサビの特徴
- 浴槽サビの補修方法
- ホーロー浴槽のサビ予防と定期的なケア
- SUS素材は錆びにくい素材ですが、正しいメンテナンスが重要です。錆取りの適切な方法は錆を起こす原因によって異なります。例えば、塩分や湿気が原因であれば、中性洗剤で汚れを落とし、完全に乾燥させることが重要です。また、定期的な防錆剤の塗布も効果的です。SUS素材は耐久性が高いため、適切なメンテナンスをすることで長く美しい状態を保つことができます。錆は素材の劣化を招き、外観や機能性を損なう可能性があるため、定期的なチェックとケアを怠らないことが重要です。適切な対策とメンテナンスを行うことで、SUS素材の製品を長持ちさせることができます。
- アクセサリーのサビ取りと自宅でのケア
- SUS素材のサビに関するよくある質問 (FAQ)
- 専門家のアドバイス:SUS素材のメンテナンス
- まとめ
ステンレスシンクのサビ落としと予防策
ステンレスシンクにサビが発生する原因
SUS素材は耐錆性に優れた素材であり、一般的にはサビにくいとされています。しかし、ステンレスシンクにサビが発生する原因は何でしょうか?実は、適切なメンテナンスが行われないことが一つの要因です。例えば、使用後に水滴や汚れを放置しておくと、それが錆の原因となります。また、強い酸性・アルカリ性の洗剤を使うことも、素材表面を傷つけてサビの発生を促してしまうことがあります。
そこで、ステンレスシンクの錆対策としては、使った後はしっかりと拭いて乾かすことや中性の洗剤を使用することが大切です。定期的にメンテナンスを行い、表面の汚れを取り除くことで、長く美しい状態を保つことができます。錆び取りのポイントを抑えて、気持ちよくキッチンを使い続けましょう。
効果的なサビ落とし方法
SUS素材の錆取りについて考えてみましょう。例えば、SUS素材は錆びにくいと言われていますが、適切なメンテナンスが必要です。錆びが発生した場合、効果的なサビ取り方法を知っておくことが重要です。まず、錆を落とすためには専用のクリーナーや研磨剤を使うことが一般的です。その後、清潔な布で拭き取り、乾いた状態に保つことがポイントです。
さらに、錆びを防ぐために定期的なメンテナンスが必要です。例えば、定期的なクリーニングや防錆剤の塗布が有効です。特に屋外や湿気の多い場所に使用する場合は、より注意が必要です。適切なメンテナンスを行うことで、SUS素材を長持ちさせることができます。これらの対策をしっかりと実施することで、SUS素材の錆び対策を効果的に行うことができます。
日常的なサビ予防策
SUS素材の錆対策とメンテナンス方法は重要です。錆は金属製品の敵であり、日常的なケアが必要です。まず、錆の原因を理解しましょう。湿気や塩分が錆の主な原因です。そのため、SUS素材をきちんと保護することが重要です。例えば、錆び止め剤や定期的な清掃でメンテナンスを行います。定期的な点検や油を差し、保管場所を湿気から遠ざけることも効果的です。SUS素材の表面にできた小さな傷も錆の原因になりますので、注意が必要です。結論として、SUS素材の長寿命を保つためには、定期的なメンテナンスが欠かせません。丁寧な手入れを行い、錆対策をしっかりとることで、SUS素材製品を長く美しく保つことができます。
ステンレス専用のクリーニング用品紹介
【錆び取り完全ガイド!SUS素材の錆対策とメンテナンス方法】
SUS素材は錆びにくいとされていますが、適切なメンテナンスが必要です。なぜなら、環境や使用状況によっては錆びる可能性があります。例えば、海辺や塩害のある地域では、錆びやすくなります。
そのため、SUS素材を長持ちさせるためには定期的なメンテナンスが欠かせません。具体的には、水で洗い、乾かすことが重要です。さらに、専用のクリーニング用品を使用して定期的に磨くことで、錆びを予防できます。
したがって、SUS素材の製品を長く美しく保つためには、適切なメンテナンスが欠かせません。適切な方法でメンテナンスを行うことで、SUS素材の製品を長くお使いいただけます。
ステンレス風呂の錆対策とメンテナンス
ステンレス風呂が錆びるメカニズム
SUS素材とは、ステンレスを指します。ステンレス製品は錆びにくい特性を持っていますが、特定の条件下では錆が発生することがあります。一般的な浴室の湿気や塩分などの影響で、風呂釜や排水口などの部分が錆びることがあります。
風呂釜の場合、水滴がたまりやすい部分や使用後の水滴が残る箇所が錆びやすいです。排水口は排水のたびに水がかかるため、錆びやすい部位と言えます。
錆取りの方法としては、中性洗剤で汚れを落とした後、柔らかいスポンジや布で水分を拭き取り、完全に乾かすことが重要です。さらに、定期的な乾拭きや風通しを良くすることで、錆びを防ぐことができます。メンテナンスを怠らず、清潔に保つことで、風呂の美しさと耐久性を保つことができます。
ステンレス風呂の正しいお手入れ方法
SUS素材の錆対策とメンテナンス方法を知ることは重要です。錆びが原因で損傷が生じることを防ぐために、適切なケアが必要です。SUS素材の特性を理解し、錆対策を行うことが大切です。例えば、定期的な清掃とメンテナンスを行うことで、SUS素材の寿命を延ばすことができます。特に湿気の多い環境では、錆びやすいので、こまめなメンテナンスが必要です。また、適切な錆対策用品を使用することも効果的です。SUS素材の持つ耐久性を生かすために、適切な対策を行い、長く美しい状態を保つことが大切です。正しいメンテナンスをすることで、SUS素材の製品を長くご利用いただけます。
長期的な風呂の錆予防策
SUS素材の錆対策とメンテナンス方法について知識を深めることは、重要です。錆は金属が酸素や水と反応して腐食する現象であり、特に長期間使用される風呂などの設備では防止が必要です。SUS素材は錆に強いとされていますが、適切なメンテナンスが欠かせません。定期的な清掃や乾燥を行うことで、錆の発生を防ぐことができます。
具体的な対策として、酸性・アルカリ性の洗剤は避け、中性洗剤を使用することが重要です。さらに、水滴や汚れがたまらないよう風呂場を清潔に保つこともポイントです。錆びた箇所が見つかった場合は、専用の錆取り剤を使用して取り除くことが大切です。
適切な対策とメンテナンスを行うことで、SUS素材の設備を長く美しく保つことができます。結果として、快適な風呂タイムを楽しむことができるでしょう。
ステンレスキッチンの錆びの原因と対策
キッチンでのサビの原因とは
SUS素材のキッチン用品は、長く使っていると錆びることがあります。その原因は、水や食材の残りカスに含まれる塩や酸がSUS素材の表面に付着し、サビを引き起こすことが挙げられます。特に、包丁やお箸などの切れるものは、刃先が摩擦などで薄くなることでサビやすくなります。
このサビを防ぐためには、使用後にきちんと乾かして保管することが大切です。食器用洗剤で洗って、しっかりと水気を拭き取り、完全に乾燥させることが重要です。さらに、酸化を防ぐためにキッチンペーパーや布巾で覆うといった対策も有効です。
定期的なメンテナンスと丁寧な取り扱いをすることで、SUS素材のキッチン用品の寿命を延ばし、綺麗な状態を保つことができます。キッチンでのサビ対策は、日常のことですが、これらのポイントを意識することで長く使えるキッチン用品となるでしょう。
ステンレスキッチンの錆び取り手順
SUS素材の錆対策とメンテナンス方法
錆が気になる方におすすめのSUS素材の錆対策とメンテナンス方法をご紹介します。SUS素材は耐食性に優れているため、錆びにくい特性があります。しかし、長い時間を経ると錆びる可能性もありますので、定期的なメンテナンスが重要です。
まず、SUS素材を清潔に保つことが大切です。定期的な拭き掃除や洗浄を行い、水分や汚れをしっかりと拭き取りましょう。さらに、塩分や化学物質に触れないように注意することも大切です。
錆びた場合は、中性洗剤や専用のクリーナーを使用して丁寧に汚れを落とし、乾いた布で水分を拭き取ります。そして、錆びた箇所に錆止め剤を塗布して再発を防ぎましょう。定期的な手入れでSUS素材の美しさを保ちながら、長くご利用いただけます。
キッチン用ステンレスのメンテナンスと保護
SUS素材は、キッチンなどでよく使用されるステンレス鋼の一種です。しかし、錆が発生することもあります。この記事では、SUS素材の錆対策とメンテナンス方法をご紹介します。
まず、なぜSUS素材が錆びるのか、その理由を見ていきましょう。SUS素材は耐食性に優れていますが、長期間使用すると表面が傷つき、酸化が進んで錆びる可能性があります。
では、具体的なメンテナンス方法はどのようなものでしょうか?SUS素材を清潔に保つことがポイントです。定期的に水で洗い、乾いた布で拭くことで汚れや酸化を防ぎます。さらに、専用のクリーナーや防錆剤を使うことで、SUS素材の輝きを長持ちさせることができます。
このように、適切なメンテナンスを行うことでSUS素材のキッチン用品を美しく保つことができます。是非参考にしてみてください。
浴槽のサビ補修とホーロー浴槽の特性
ホーロー浴槽のサビの特徴
SUS素材は、錆びにくい性質を持つため、日常のメンテナンスが比較的簡単です。しかし、長期間の使用や特定の環境条件下では、錆びる可能性があります。その際には、適切な対策とメンテナンスが欠かせません。
SUS素材の錆びは、水滴や薬品の付着によるものが一般的です。特に水滴が長時間付着すると、サビの原因となります。そのため、使用後はしっかりと拭き取ることが重要です。さらに、専用のクリーナーやワックスを使って定期的に清掃し、保護膜を形成することで、錆びを防ぐことができます。
定期的なメンテナンスを行うことで、SUS素材の長寿命化と美観を維持することができます。錆対策とメンテナンスをしっかりと行い、快適な生活空間を保つことが大切です。
浴槽サビの補修方法
[heading]=錆び取り完全ガイド!SUS素材の錆対策とメンテナンス方法
[text]=SUS素材で作られた製品は高い耐久性と優れた品質で知られています。しかし、長期間使用していると錆が発生することがあります。錆は製品の見た目や機能を損なうだけでなく、健康にも悪影響を及ぼす可能性があります。そこで、錆び対策と適切なメンテナンスが重要となります。
錆びを取り除く方法はさまざまですが、軽度の場合は中性洗剤や専用のクリーナーを使うことで対処できます。重度の錆びの場合は専門家に相談することが必要です。定期的な清掃と保湿処理を行うことで、SUS製品の寿命を延ばすことができます。
大切な製品を長く使うために、適切な錆び取り対策とメンテナンスを怠らず行うことがポイントです。
ホーロー浴槽のサビ予防と定期的なケア
SUS素材は錆びにくい素材ですが、正しいメンテナンスが重要です。錆取りの適切な方法は錆を起こす原因によって異なります。例えば、塩分や湿気が原因であれば、中性洗剤で汚れを落とし、完全に乾燥させることが重要です。また、定期的な防錆剤の塗布も効果的です。SUS素材は耐久性が高いため、適切なメンテナンスをすることで長く美しい状態を保つことができます。錆は素材の劣化を招き、外観や機能性を損なう可能性があるため、定期的なチェックとケアを怠らないことが重要です。適切な対策とメンテナンスを行うことで、SUS素材の製品を長持ちさせることができます。
アクセサリーのサビ取りと自宅でのケア
ネックレスなどのアクセサリーにサビがつく原因
SUS素材の錆対策とメンテナンス方法
アクセサリーなどのアイテムにサビがつく原因は、主に湿気や酸素、塩分などが挙げられます。特に、ステンレス素材(SUS素材)は錆びにくいとされていますが、長期間使用すると錆びる可能性もあります。湿気が直接付着したり、塩分が付着することでサビや汚れが生じるため、定期的なメンテナンスが重要です。
SUS素材のアクセサリーを長く美しく保つためには、使った後は柔らかい布で優しく拭くことや、水気をしっかり拭き取ることが大切です。また、保管場所は湿気や直射日光を避け、空気の通り道や換気がきちんとできる場所に保管すると効果的です。定期的なメンテナンスを怠らず、愛用のアクセサリーをいつも美しく保ちましょう。
自宅でできるアクセサリーのサビ取り方法
この度は、SUS素材の錆対策とメンテナンス方法についてご紹介します。SUS素材は耐食性に優れていますが、長期間の使用や適切な手入れがないと錆びることがあります。錆びが発生すると見た目が損なわれるだけでなく、機能面でも問題を引き起こす可能性があります。
まず、錆びの原因を理解することが重要です。湿気や塩分の影響など様々な要因が錆びを引き起こします。そのため、定期的なメンテナンスが欠かせません。メンテナンス方法としては、柔らかい布で定期的に拭き取ることや錆び取り剤を使うことが有効です。
具体的な例として、キッチン用品や屋外の家具など、日常的に使用するアイテムは特に錆びやすい傾向にあります。こうしたアイテムは定期的なメンテナンスを行い、錆びを防ぐことが大切です。
大切なSUS素材のアイテムを長く美しく保つために、適切な錆対策とメンテナンスが欠かせません。しっかりと手入れをすることで、その素材本来の特性を引き出し、長くご利用いただけます。
アクセサリーのサビを防ぐための保管方法
SUS素材の錆取り完全ガイド!SUS素材の錆対策とメンテナンス方法
SUS素材は錆びにくい素材として知られていますが、適切なケアが必要です。錆対策の理由は、SUS素材でも長期間の使用や適切なメンテナンスが行われないと、錆びる可能性があります。例えば、湿気の多い場所や塩分の多い環境では、SUS素材も錆びることがあります。
そのため、SUS素材のアクセサリーなどを長持ちさせるためには、定期的なメンテナンスが重要です。例えば、柔らかい布で定期的に拭き取ることや、外部からの湿気を避けるために適切な保管方法を遵守することが大切です。
これらの対策を行うことで、SUS素材のアクセサリーが美しく長持ちし、錆びを防ぐことができます。
SUS素材のサビに関するよくある質問 (FAQ)
SUS素材とは何か
SUS素材は、ステンレス鋼の一種で、錆びにくい性質が特徴です。この素材は様々な用途に使われており、建築や食品加工、医療機器など幅広い分野で重宝されています。錆び取りの方法として、定期的な洗浄とメンテナンスが重要です。錆びができてしまった場合、中性洗剤や専用のクリーナーを使って丁寧に汚れを落とすことがポイントです。特に外部で使用されている場合は、雨や風などの自然要因からも保護することが大切です。メンテナンスを怠ると、SUS素材の寿命が縮まってしまう可能性があります。そのため、定期的なケアと注意が必要です。錆び取りの完全ガイドを実践することで、SUS素材製品の美しさと耐久性を保つことができます。
SUS素材の錆びに関する誤解とその解明
SUS素材の錆びに関する誤解とその解明
一般的に、SUS素材は錆びにくいとされていますが、完全に錆びないというわけではありません。特に、環境や使用条件によっては錆びる可能性があります。そのため、適切なメンテナンスが重要です。
例えば、SUS素材は鉄とクロムを主成分としていますが、クロムの保護皮膜が破損すると錆びやすくなります。海水や塩分の多い環境では、特に注意が必要です。定期的な洗浄や塗装などの対策が大切です。
つまり、SUS素材でも錆びる可能性があるため、適切な管理が欠かせません。メンテナンスを怠らず、定期的なチェックを行うことで、SUS素材の耐久性を保つことができます。
SUS素材の正しい取り扱いとメンテナンスのポイント
SUS素材の正しい取り扱いとメンテナンスのポイント
錆び取りは重要なメンテナンス作業です。SUS素材を長持ちさせるために、錆対策は欠かせません。まず、定期的な清掃が必要です。湿気の多い場所では、水気を拭き取ることが重要です。さらに、錆の初期段階では中性洗剤やクリーナーを使用してこすらないようにしましょう。
例えば、屋外で使用するSUS素材製品を考えてみましょう。雨風にさらされることで錆びやすくなります。こうした場合は、防水カバーを使用するか、定期的に乾いた布で拭くことで錆びを防ぐことができます。
大切なのは、定期的なメンテナンスと適切な対策です。これらのポイントを守ることで、SUS素材製品の寿命を延ばし、美しい状態を保つことができます。
専門家のアドバイス:SUS素材のメンテナンス
プロが教えるSUS素材の長持ちさせる秘訣
SUS素材を使った製品は、錆びや腐食から守るために信頼されています。しかし、適切なケアやメンテナンスが必要です。SUS製品を長持ちさせるためには、定期的な清掃と保護が不可欠です。湿気や塩分、化学物質などは錆びの原因となります。そのため、定期的な拭き取りや専用の防錆剤の使用が重要です。具体的な例を挙げると、屋外で使用されるSUS製のガーデン家具は、雨や風にさらされるため錆びやすいです。こうした場合、特に雨後は乾拭きして水分を拭き取り、防錆スプレーを定期的に塗布すると効果的です。きちんとしたメンテナンスを心がければ、SUS素材の製品は長く美しく使うことができます。
錆び取りのプロセスと安全な取り扱い
SUS素材の錆対策とメンテナンス方法を知ることは、品物を長持ちさせるために重要なポイントです。まず、錆び取りのプロセスを理解することから始めましょう。SUS素材は錆びにくい特性を持っていますが、適切なメンテナンスが必要です。錆びが発生した場合、専用のクリーナーや研磨剤を使って丁寧に錆を取り除きます。この作業を丁寧に行うことで、素材の劣化を防ぎます。
安全な取り扱いも大切です。作業時には適切な保護具を着用し、換気をよくして作業することが重要です。例えば、手袋やマスクを着用し、作業場を十分に換気しておきましょう。
錆び取りのプロセスと安全な取り扱いを守ることで、SUS素材の品質を保ち、安全に使用することができます。メンテナンスを怠らず、長く使えるように心がけましょう。
おすすめのメンテナンス用品と使用方法
SUS素材の錆対策とメンテナンス方法
錆び取りはSUS素材の大切なメンテナンスです。SUS素材は錆びにくい特性を持ちながらも、対策を怠ると錆が発生する可能性があります。定期的な清掃と保護が重要です。
まず、錆び取り用品として推奨されるアイテムは、中性洗剤や専用のクリーナーです。これらを使って定期的に表面の汚れを落とし、乾いた布で拭き取りましょう。さらに、錆対策としては防錆剤やコーティング剤の利用が効果的です。
具体的な例として、戸外で使用されるSUS製品は雨や湿気から守るために定期的なメンテナンスが必要です。洗浄後は必ず乾燥させ、防水スプレーなどで保護処理を行うと良いでしょう。
錆び取りの手順をしっかり守り、適切なメンテナンス用品を使用することで、SUS素材を長く美しく保つことができます。お手入れを怠らず、大切な製品をいつまでも良い状態で保つようにしましょう。
まとめ
SUS素材は錆びにくいため、錆対策とメンテナンスは比較的簡単です。SUS素材の製品を使用する際には、定期的な清掃や保護フィルムの使用が重要です。また、塗装や表面処理を施すことで、耐久性を高めることができます。これらの方法を実践することで、SUS素材を長く美しい状態で保つことができます。
「SUS酸洗いで輝く!ステンレス表面処理の効果的な方法」
「SUS酸洗いで輝く!ステンレス表面処理の効果的な方法」
皆さん、ステンレス製品の美しさを保つ方法を知っていますか?その秘訣は、「SUS酸洗い」にあります。ステンレス製品は耐久性や美観が魅力ですが、長期間使っていると表面に汚れや錆が付着してしまうことがあります。そんなときこそ、SUS酸洗いが輝く力を発揮します。
この記事では、SUS酸洗いの効果的な方法を詳しく解説します。SUSとは何か、酸洗いとはどういう作業なのか、そしてその効果的な方法まで、全てを丁寧にお伝えいたします。
もし、自宅や工場でステンレス表面の美しさを保ちたいと考えているのであれば、ぜひこの記事をご覧になってください。SUS酸洗いをマスターし、ステンレス製品をいつまでも輝かせる方法を身につけましょう。
Contents
SUS酸洗いとは
SUS酸洗いの基礎知識
SUS酸洗いは、ステンレス鋼の表面処理方法の一つです。この処理は、酸性の浸漬液を使用してステンレス鋼表面から不純物を取り除くことで、素材の輝きを取り戻す効果があります。酸洗いは表面の汚れや酸化皮膜を取り除き、耐食性や見た目の美しさを向上させる重要な工程です。
ステンレス製品の製造業界では、SUS酸洗いが品質向上や耐久性向上に不可欠なプロセスとして利用されています。具体的な例として、建築資材や調理器具、日常生活用品などでSUS酸洗いが活用されています。
このように、SUS酸洗いはステンレス製品の品質と見た目を向上させる効果的な方法として、幅広い産業で重要な役割を果たしています。
ステンレスと酸洗いの関係
ステンレス製品は日常生活や産業分野で幅広く使用されていますが、長期間使用すると表面に汚れや劣化が生じます。そこで、SUS酸洗いという特殊な処理方法が効果的です。この処理は酸性の液体に浸すことで、ステンレス表面の汚れや酸化物を取り除き、輝きを取り戻すことができます。
例えば、キッチン用品や建築資材など、日常生活でよく使われるステンレス製品は、定期的な酸洗いによって美しさを保つことができます。さらに、工業製品の表面処理においても、SUS酸洗いは耐久性や品質向上に貢献します。
したがって、ステンレス製品の美しさや機能性を維持するためには、定期的なSUS酸洗い処理が欠かせません。この方法を活用することで、ステンレス製品の寿命を延ばし、品質を高めることができます。
酸洗いの歴史的背景と発展
SUS酸洗いは、ステンレス表面処理の重要な工程の一つです。酸洗いの歴史的背景は古く、その効果的な方法が発展してきました。ステンレス製品は、錆や汚れを取り除き、美しい光沢を保つために酸洗いが欠かせません。
酸洗いの重要な理由は、ステンレス表面の清浄化や腐食の予防にあります。例えば、自動車や建築物の外装パーツ、キッチン用品など、さまざまな製品に酸洗い処理が施されています。このような処理により、ステンレス製品の耐久性や美観が向上し、品質の向上につながります。
つまり、SUS酸洗いはステンレス製品の品質と見栄えを向上させるための効果的な方法であり、製品の長寿命化にも貢献しています。
SUS酸洗いの目的
表面の酸化皮膜の除去
表面の酸化皮膜の除去
ステンレス製品は美しさと耐久性で人気ですが、時間が経つと表面に酸化皮膜ができてしまいます。この酸化皮膜を取り除く作業は非常に重要です。その方法の一つがSUS酸洗いです。
まず、酸洗いは酸性の溶液を使って酸化皮膜を溶かすプロセスです。これにより表面がきれいになり、新品同様の輝きを取り戻します。例えば、キッチン用品や建築資材など、さまざまな製品で使用されています。
SUS酸洗いの効果的な方法は定期的なメンテナンスです。定期的な酸洗いによって、ステンレス製品の寿命を延ばし、美しさを保つことができます。
美しさと耐久性を保つために、SUS酸洗いは重要な工程であり、適切な方法で行うことが大切です。
耐食性向上のための処理
SUS酸洗いは、ステンレス鋼の耐食性を向上させる効果的な表面処理方法です。ステンレス鋼はその耐食性や美観から幅広い用途に使用されていますが、長期間の使用や環境の影響により表面に汚れや腐食が生じることがあります。こうした問題を解決するために、SUS酸洗いが活用されています。
SUS酸洗いの主な効果は、表面の汚れや酸化皮膜を取り除き、ステンレス鋼本来の輝きや耐食性を回復させることです。例えば、食品加工業界や建築業界において、SUS酸洗いされたステンレス製品は衛生面や耐久性の向上に貢献しています。
このように、SUS酸洗いはステンレス鋼製品の保護や美観維持に効果的な方法として広く利用されています。耐食性の向上や品質の維持において、SUS酸洗いは重要な役割を果たしています。
製品の美観を高める効果
SUS酸洗いで輝く!ステンレス表面処理の効果的な方法
ステンレス鋼は、耐久性や美観からさまざまな製品に広く使用されています。その美しさを長く保つためには、SUS酸洗いという特殊な処理が重要です。この処理には、表面の汚れや酸化物を取り除き、艶やかな仕上がりを実現する効果があります。
SUS酸洗いは、製品の耐久性を向上させるだけでなく、見た目の美しさも高めます。例えば、キッチン用品や建築材料など、日常生活でよく使われる製品において、SUS酸洗いは品質を保つために欠かせない工程となっています。
SUS酸洗いの効果を活かすことで、製品の寿命を延ばし、美観を保つことができます。品質と外観を重視する製品において、SUS酸洗いは重要な工程であり、製品価値を高める一助となります。
酸洗いのプロセス
前処理としての脱脂
SUS酸洗いで輝く!ステンレス表面処理の効果的な方法
ステンレス製品を美しく保つために重要な工程の1つが、SUS酸洗いという前処理です。この工程は、ステンレス表面から不純物や油分を取り除くことで、表面処理の効果を最大限に引き出す役割を果たします。
ステンレス製品は耐久性があり、光沢が美しいため、さまざまな産業で広く使用されています。しかし、長期間の使用や環境の影響により、表面に汚れや酸化が生じることがあります。こうした状況において、SUS酸洗いを行うことで、ステンレス表面をクリーンで美しい状態に保つことができます。
例えば、キッチン用品や建築材料などのステンレス製品は、SUS酸洗いによって長持ちし、品質を維持することができます。そのため、製品の寿命を延ばし、美しさを保つために、ステンレス製品の定期的なSUS酸洗いは欠かせません。
酸洗いのステップ
SUS酸洗いは、ステンレス表面処理において重要な工程です。まず第一に、酸洗いのステップは表面の汚れや酸化物を取り除き、素材をクリーンな状態に戻す役割があります。これにより、ステンレスの耐食性や美観を向上させることができます。
この処理は、錆びや汚れの原因となる不純物を効果的に取り除くだけでなく、表面の均一性を確保します。例えば、工業製品や建築材料などで使用されるステンレス製品は、長期間使用されるため、定期的な酸洗いは品質を維持するために欠かせません。
したがって、SUS酸洗いはステンレス製品の耐久性と美観を保つために効果的な方法であり、製品の品質向上に不可欠な工程と言えます。
中和と後処理
「SUS酸洗いで輝く!ステンレス表面処理の効果的な方法」
ステンレス製品は、美しく輝く外観を保つために、SUS酸洗いという特別な処理が欠かせません。この処理は、表面に付着した不純物を除去し、耐久性や耐食性を向上させる効果があります。
その理由は、ステンレスは美しいだけでなく、錆びにくく頑丈な素材であるため、多くの産業や製品で広く利用されています。例えば、キッチン用品や建築材料、医療機器など様々な分野でステンレス製品が重要な役割を果たしています。
したがって、SUS酸洗いは、ステンレス製品の品質を保ち、長い間美しい状態を維持するために欠かせない工程なのです。ステンレス製品が光り輝く魅力を引き出す効果的な方法と言えるでしょう。
SUS酸洗いの効果
長期的な耐久性の向上
SUS酸洗いで輝く!ステンレス表面処理の効果的な方法
ステンレス製品の長期的な耐久性を高めるために重要なのが、SUS酸洗いという処理方法です。この処理によって、表面の汚れや酸化を取り除き、美しい光沢を取り戻すことができます。
まず、SUS酸洗いの理由としては、ステンレス表面に付着した不純物や酸化皮膜を効果的に除去することが挙げられます。これにより、表面の清潔さや美しさが保たれ、耐久性が向上します。
具体的な例として、キッチン用品や建築資材など日常的に使用されるステンレス製品があります。これらがSUS酸洗いを施すことで、長く美しい状態を保つことができます。
以上から、SUS酸洗いはステンレス製品の美しさや耐久性を向上させる効果的な方法であることが分かります。是非、定期的なメンテナンスとして取り入れてみてください。
メンテナンスコストの削減
酸洗い処理はステンレス製品に光沢と耐久性を与える方法です。この方法の効果は信じられないほど効果的です。まず、酸洗いによって表面の不純物や酸化物が取り除かれ、ステンレスの美しい輝きが蘇ります。その後、耐食性が向上し、長期間使用しても劣化が少なくなります。例えば、建築物や調理器具、家具など、さまざまな製品にこの処理が施されています。この方法を活用することで、製品の寿命を延ばし、メンテナンスコストを削減できます。要するに、酸洗い処理はステンレス製品の価値を高めるだけでなく、長期的な視点からもコストを節約する手段として非常に効果的です。
環境への影響と安全性
「SUS酸洗いで輝く!ステンレス表面処理の効果的な方法」
ステンレス鋼は、耐久性や美しさで広く使われている素材です。その表面処理方法の1つにSUS酸洗いがあります。SUS酸洗いは、表面の不純物を取り除き、酸化被膜を形成することで耐食性を高める効果があります。
この処理方法は、環境への影響と安全性にも配慮されています。酸洗いに使用される化学薬品は、適切に処理されることで環境への負荷を最小限に抑えています。また、作業時の安全対策や適切な設備の整備によって作業者の安全も確保されています。
SUS酸洗いは、ステンレスの美しさや耐久性を高めるだけでなく、環境への配慮と作業者の安全を考えた効果的な表面処理方法と言えます。
ステンレスの酸洗い注意点
使用する酸の種類と濃度
「SUS酸洗いで輝く!ステンレス表面処理の効果的な方法」
SUS酸洗いは、ステンレスの表面処理において重要な工程です。この工程で酸を使用してステンレス表面を洗浄し、光沢や耐久性を向上させることができます。使用する酸の種類と濃度は、処理の効果に大きく影響します。
例えば、硝酸を使用すると表面の酸化皮膜を取り除き、ステンレスの輝きを引き出すことができます。また、塩酸を使用すると錆の除去や清浄効果が期待できます。適切な酸の選定や濃度の調整は、処理品質を向上させるポイントです。
ステンレス製品の美しさと品質を保つためには、正確な酸洗い工程が欠かせません。適切な酸の選定と濃度管理によって、効果的なステンレス表面処理が可能となります。
処理時間と温度の管理
「SUS酸洗いで輝く!ステンレス表面処理の効果的な方法」
ステンレス表面処理の重要なポイントは処理時間と温度の管理です。適切な時間と温度で行うことで、ステンレス製品の表面がきれいになり、耐久性も向上します。
例えば、SUS酸洗いは、ステンレス表面に付着した汚れや酸化物を取り除く方法です。この処理を正確な時間と温度で行うことで、ステンレス製品の輝きを取り戻すことができます。
したがって、ステンレス製品を美しく保ちたい場合は、適切な処理時間と温度を守ることが重要です。適切な管理を行うことで、ステンレス製品の美しさと耐久性を保つことができます。
安全な作業環境の確保
「SUS酸洗いで輝く!ステンレス表面処理の効果的な方法」
ステンレス製品は、その美しさと耐久性から幅広い用途で使用されています。しかし、長期間使用していると表面に汚れや錆が付着し、見た目や機能性が損なわれることがあります。そこで、SUS酸洗いという表面処理方法が登場します。
SUS酸洗いは、酸性洗浄液を使用してステンレス表面の汚れや酸化物を取り除くプロセスです。この処理により、ステンレス表面の輝きがよみがえり、耐食性や耐久性も向上します。例えば、キッチン用品や建築材料など、様々な製品に活用されています。
効果的なSUS酸洗いを行うことで、ステンレス製品の寿命を延ばし、美しさを保つことができます。このような手法を活用することで、ステンレス製品の価値をより長く維持できるでしょう。
SUS酸洗いと他の表面処理手法との比較
機械的研磨との違い
“SUS酸洗いで輝く!ステンレス表面処理の効果的な方法”
ステンレス製品には、美しい光沢や耐久性を保つために表面処理が欠かせません。その中でも、SUS酸洗いは効果的な方法の一つです。SUS酸洗いは、表面に付着した不純物を取り除き、均一な仕上がりを実現します。これによって、ステンレス製品の見た目や性能が向上し、長期間美しさを保つことができます。
一方、機械的研磨とは異なり、SUS酸洗いは化学的な処理を行うため、微細な傷を取り除くことができます。特に食品業界や医療機器業界では、衛生面を考慮してSUS酸洗いが選ばれることが多くあります。
つまり、SUS酸洗いはステンレス製品を美しく保ち、品質向上に貢献する効果的な表面処理方法と言えます。そのため、製品の価値を高めるためにも、適切な処理が重要であることを覚えておきましょう。
電解研磨との対比
「SUS酸洗いで輝く!ステンレス表面処理の効果的な方法」
酸洗いは、ステンレス製品を輝かせる重要な工程です。この処理は、表面に付着した不純物を取り除き、美しい仕上がりを実現します。一方、電解研磨と比較すると、酸洗いは特定の部分に焦点を当て、細かな部分まで手作業で処理できる利点があります。
例えば、建築やキッチン用具などのステンレス製品は、酸洗いによって汚れや傷を除去し、耐久性を向上させることができます。さらに、食品関連の産業や医療機器の製造でも、酸洗いは製品の品質向上に欠かせない工程となっています。
結論として、SUS酸洗いはステンレス製品の品質を向上させ、美しい仕上がりを実現するための効果的な方法と言えます。
コーティングとの相違点
「SUS酸洗いで輝く!ステンレス表面処理の効果的な方法」
ステンレス製品の表面処理は重要です。SUS酸洗いは、ステンレス表面をきれいにし、耐食性や美観を向上させる効果的な方法です。酸洗いを行うことで、表面に付着した不純物や酸化皮膜を除去し、美しい光沢を取り戻すことができます。
例えば、建築資材や調理器具など、日常生活でよく使われるステンレス製品は、長期間使用すると表面に汚れやくすみが生じます。こうした場合、SUS酸洗いを行うことで、再び輝く美しい表面を取り戻すことができます。
ステンレス製品の寿命や品質を向上させるためにも、SUS酸洗いは重要な工程と言えるでしょう。効果的な表面処理を行うことで、ステンレス製品の魅力を引き立てることができます。
酸洗い後のステンレスの維持管理
日常のお手入れ方法
「SUS酸洗いで輝く!ステンレス表面処理の効果的な方法」
ステンレス製品は日常使いに欠かせない素材ですが、時間が経つと表面に汚れや傷がついてしまいます。そんな時に重宝するのがSUS酸洗いという方法です。この方法は、ステンレス表面の汚れや錆を効果的に除去し、輝きを取り戻すことができます。
具体的には、SUS酸洗いは酸性の洗浄液を使用してステンレス表面を浸し、汚れや錆を溶かす方法です。この処理によって表面がきれいになり、耐久性も向上します。例えば、キッチン用品や建築資材など、さまざまな製品にこの処理が施されています。
SUS酸洗いは、ステンレス製品の美しさと長持ちさを維持するために欠かせない方法と言えます。日常のお手入れ方法として、定期的にこの処理を行うことで、ステンレス製品をいつまでも輝かせることができます。
サビや汚れ防止策
酸洗いは、ステンレス製品の表面処理において重要な方法です。この処理により、ステンレスの表面からサビや汚れを除去し、光沢を取り戻すことができます。さらに、酸洗いによって表面の耐久性も向上し、製品の寿命を延ばすことが可能です。
例えば、キッチン用品や建築材料など、日常生活で使用されるさまざまな製品において、酸洗いは効果的な手法として利用されています。特に、長期間使用される製品は、定期的な酸洗いを行うことで美しさと耐久性を保つことができます。
したがって、ステンレス製品の長寿命と美しい外観を維持するためには、適切な酸洗いが欠かせません。定期的なメンテナンスや適切な処理を行うことで、製品の品質を保ち、より長くご利用いただくことができます。
維持管理のための推奨品
「SUS酸洗いで輝く!ステンレス表面処理の効果的な方法」
ステンレス製品は、美しさと耐久性で人気があります。その美しさを保つためには、定期的なメンテナンスが欠かせません。その中でもSUS酸洗いは、効果的な表面処理方法として注目されています。
SUS酸洗いは、ステンレス表面の酸化皮膜を取り除き、新品同様の輝きを取り戻すことができます。例えば、建築物やキッチン用品など、さまざまな製品に活用されています。この方法を定期的に行うことで、ステンレス製品の寿命を延ばし、美しさを保つことができます。
要するに、SUS酸洗いはステンレス製品を長く使用するために欠かせない手段です。定期的なメンテナンスを行うことで、ステンレス製品が永く輝き続けることができるのです。
酸洗いを行う際の環境配慮
廃液処理の重要性
ステンレス表面処理において、SUS酸洗いは非常に効果的な方法です。SUS酸洗いは、表面に付着した不純物や酸化物をしっかりと除去し、素材本来の輝きを取り戻すことができます。この処理は、ステンレス製品の品質や耐久性を向上させるために欠かせません。
例えば、建築やキッチン用具などで使用されるステンレス製品は、頻繁に使用されるため表面が汚れやすくなります。SUS酸洗いを行うことで、これらの製品を定期的にメンテナンスすることができ、長く美しい状態で使用することが可能です。
要するに、SUS酸洗いはステンレス製品の美しさや機能性を保つために重要な工程であると言えます。その効果を最大限に引き出すためにも、適切な方法で定期的に処理を行うことが大切です。
環境保護基準と法規制
「SUS酸洗いで輝く!ステンレス表面処理の効果的な方法」
ステンレス製品は、耐久性や美しさで人気がありますが、その輝きを長持ちさせるためには、定期的なメンテナンスが必要です。その中でもSUS酸洗いは、ステンレス表面処理の中でも特に効果的な方法の一つです。酸洗いをすることで、表面に付着した汚れや酸化皮膜を除去し、美しい輝きを取り戻すことができます。
SUS酸洗いの効果を理解するためには、具体的な例を見てみましょう。例えば、キッチンの排水口や浴室のステンレス蛇口などは、日常的な水アカや汚れが付着しやすい箇所です。定期的にSUS酸洗いを行うことで、これらの箇所を清潔に保ち、美しさを保つことができます。
要するに、SUS酸洗いはステンレス製品の美しさや耐久性を保つために欠かせないメンテナンス方法と言えます。定期的なお手入れを行うことで、あなたのステンレス製品もいつまでも輝き続けることができるでしょう。
グリーン化学への取り組み
「SUS酸洗いで輝く!ステンレス表面処理の効果的な方法」
ステンレス製品の表面には、使用や環境の影響で汚れや錆が付着しやすくなることがあります。このような問題を解決するために、SUS酸洗いが効果的な方法として注目されています。
まず、SUS酸洗いは、表面の汚れや酸化皮膜を取り除くことができます。これにより、ステンレス製品の美しい光沢を取り戻し、長期間使用しても品質を保つことができます。例えば、キッチン用品や建築材料など、さまざまな製品でSUS酸洗いが活用されています。
SUS酸洗いは環境にやさしいグリーン化学の一環としても評価されており、製品の耐久性を向上させるだけでなく、環境への配慮も促進します。ステンレス製品を長く美しく保つために、SUS酸洗いの効果を活用しましょう。
SUS酸洗いの事例紹介
工業分野での応用事例
SUS酸洗いは、ステンレス表面をきれいにする効果的な方法です。ステンレス製品は耐久性があり、長持ちしますが、時間とともに表面に汚れがつきます。この汚れを取り除くために、SUS酸洗いが活用されます。
まず、酸性の溶液を使用してステンレス表面の汚れや酸化物を除去します。これにより、製品の美しさや機能を保つことができます。たとえば、建築用のステンレス手すりやキッチン用品など、さまざまな製品に活用されています。
SUS酸洗いは、ステンレス製品のメンテナンスに欠かせない技術であり、製品の寿命を延ばすことができます。このように、SUS酸洗いはステンレス製品を輝かせる重要な方法として、工業分野で広く活用されています。
生活用品における事例
「SUS酸洗いで輝く!ステンレス表面処理の効果的な方法」
ステンレス製品は広く使われていますが、時間とともに錆びや汚れが付着することがあります。そんなときに役立つのがSUS酸洗いという表面処理方法です。SUS酸洗いは、ステンレス表面から汚れや酸化皮膜を取り除くことで、美しい光沢を取り戻すことができます。
この方法は、耐久性を高めるだけでなく、見た目も美しく保つことができます。例えば、キッチン用品や車のパーツなど、さまざまな生活用品にSUS酸洗いを施すことで、長い間美しい姿を保つことができます。
ですから、ステンレス製品を長く使いたい方や美しさを保ちたい方にとって、SUS酸洗いは効果的な方法と言えるでしょう。美しいステンレス製品を長く使いたい方は、ぜひSUS酸洗いを活用してみてください。
酸洗い技術の未来展望
「SUS酸洗いで輝く!ステンレス表面処理の効果的な方法」
ステンレス表面処理において、SUS酸洗い技術は重要な役割を果たしています。この技術には、表面の浄化や腐食物質の除去といった効果があります。例えば、自動車や建築物などのステンレス製品は、長年の使用によって汚れや錆が付着し、美観や耐久性が損なわれることがあります。そこで、SUS酸洗い技術を用いることで、素材本来の輝きや品質を取り戻すことが可能となります。
さらに、SUS酸洗いは環境にも配慮した方法であり、再利用やリサイクルが容易です。このような効果的な表面処理方法が、製品の寿命を延ばし、美しさを保つために重要な役割を果たしています。したがって、SUS酸洗い技術の進化は、ステンレス製品の品質向上や持続可能性への貢献が期待されています。
酸洗いに関するよくある質問
酸洗いの安全性について
酸洗いは、ステンレス表面処理において効果的な方法の一つです。このプロセスは、表面から不純物を取り除き、素材をきれいな状態に整えることができます。この方法の安全性について、適切な注意が必要です。酸洗いには強い腐食性があり、適切な手袋や保護メガネを着用することが不可欠です。また、作業場所はよく換気することが重要です。
例えば、自動車部品の製造工程において、酸洗いは部品の表面を清潔にし、塗装やめっきの密着性を向上させる重要な工程として利用されています。このように、適切な対策を講じることで、酸洗いは安全かつ効果的に利用することができます。
酸洗いを適切に行うことで、ステンレス製品の品質や耐久性を向上させることができ、美しい仕上がりを実現することが可能です。そのため、酸洗いはステンレス表面処理において重要な役割を果たしています。
自宅での酸洗いは可能か
ステンレス製品の表面処理として、SUS酸洗いが注目されています。この方法は、表面の錆や汚れを取り除き、光沢を引き出す効果があります。一般家庭でも自宅での酸洗いは可能ですが、注意が必要です。適切な換気を確保し、専用の酸洗い剤を使用することが重要です。例えば、キッチン用品や浴室のステンレス製品を磨いて輝かせることができます。しかし、酸性の薬品は取り扱いに十分な知識と慎重さが必要です。自宅での酸洗いは効果的な方法ですが、安全面に留意し、適切な手順を守ることが大切です。充分な注意を払えば、ステンレス製品を美しく保つことができるでしょう。
酸洗いサービスの選び方
「SUS酸洗いで輝く!ステンレス表面処理の効果的な方法」
ステンレス製品は、日常生活や産業分野で幅広く使用されています。その美しさや耐久性を保つために重要なのが、SUS酸洗いという表面処理方法です。SUS酸洗いは、ステンレス表面の清潔さや耐食性を向上させる効果があります。
この方法を効果的に行うためには、適切な酸洗いサービスを選ぶことが不可欠です。信頼できる業者を選ぶことで、製品の品質や耐久性を向上させることができます。例えば、自動車部品や建築資材など、さまざまな産業でSUS酸洗いが活用されています。
酸洗いの選び方は重要です。適切な方法で製品を処理することで、ステンレス製品の寿命を延ばし、美しさを保つことができます。正しい酸洗いサービスを選ぶことで、ステンレス製品が輝きを取り戻し、長く利用することが可能となります。
まとめ
ステンレス表面処理の方法であるSUS酸洗いは、ステンレス製品や部品の表面をクリーニングし、輝きを取り戻す効果的な手段です。この方法は、ステンレスの表面に付着した汚れや酸化皮膜を取り除き、新品同様の美しい光沢を取り戻すことができます。特に、環境に関する懸念が高まっている現代では、再利用やリサイクルの観点からも効果的な方法として注目されています。ステンレス製品の美しさを保つためには、定期的なSUS酸洗い処理が重要です。
【精密加工必見】SUS材の切削加工方法と注意点
SUS材とは
SUS材の特性と用途
SUS材は、その高い耐久性と耐食性から様々な産業で広く使用されています。たとえば、自動車産業ではエンジン部品や排気管などにSUS材が使われており、その信頼性が求められています。また、食品加工業界でもSUS材は衛生面や耐食性から重宝されています。 SUS材の切削加工方法には、適切な切削速度や刃具の選定が重要です。刃具の選定を誤ると加工精度が低下し、材料が傷ついてしまう可能性があります。例えば、硬いSUS材を切削する際には、適切な刃具を使用して高速で切削することがポイントです。 そのため、SUS材の特性を理解し、適切な切削加工方法を選択することが重要です。適切な処理を行うことで、SUS材の性能を最大限に活かし、効率的かつ品質の高い加工が可能となります。ステンレス(SUS)の種類と特徴
ステンレス鋼(SUS)は、優れた耐食性と機械的特性を持ち、多種多様な用途で使用されています。以下では、主なステンレス鋼の種類とその特徴について整理します。ステンレス鋼の主な種類
種類 | 主な成分 | 特徴 | 主な用途 |
---|---|---|---|
オーステナイト系 | クロム・ニッケル | 優れた耐食性と加工性を持つ。非磁性。 | 台所用品、建築材料、化学プラント部品など。 |
フェライト系 | クロム | 強度はやや劣るが、耐食性があり磁性を持つ。 | 自動車部品、家庭電化製品部品など。 |
マルテンサイト系 | クロム | 高強度・高硬度を特徴とし、耐摩耗性に優れる。 | 刃物、バルブ、工具など。 |
析出硬化系 | クロム・ニッケル・銅 | 高強度で耐食性を持ち、精密部品に適する。 | 航空宇宙、精密機器部品など。 |
二相系(デュプレックス) | クロム・ニッケル・モリブデン | オーステナイト系とフェライト系の特性を併せ持つ。 | 海洋構造物、化学プラント、タンクなど。 |
ステンレス鋼の特徴と特性
特徴 | 詳細 |
---|---|
耐食性 | クロムが酸化膜を形成し、錆びにくい性質を持つ。 |
機械的強度 | 種類により異なるが、高い強度と耐摩耗性を持つものが多い。 |
加工性 | オーステナイト系は加工が容易で、フェライト系やマルテンサイト系は加工性が低い。 |
耐熱性 | 高温環境での使用に適した種類も多い(特にオーステナイト系)。 |
磁性 | フェライト系やマルテンサイト系は磁性を持つが、オーステナイト系は非磁性。 |
SUS材を使用する際のメリット
SUS材を使用する際のメリットは、その耐久性と柔軟性にあります。SUS材はステンレス鋼の一種で、錆びにくく、強度が高いため、切削加工に適しています。例えば、自動車部品や精密機器などの製造では、SUS材がよく使用されます。これは、環境にさらされる部品や耐摩耗性が求められる機器に適しているからです。工業製品の中でも、高い品質が要求される場面において、SUS材は信頼性が高い素材として重宝されています。したがって、切削加工の際には、SUS材の耐久性と柔軟性を活かした加工方法を選択することが重要です。これにより、製品の品質向上や長寿命化が期待できます。SUS材の切削加工方法
切削工具の選択基準
SUS材の切削加工方法を考える際に、まず重要なのは切削工具の選択基準です。切削工具を選ぶ際には、材料特性や加工する形状などを考慮する必要があります。例えば、SUS材は硬い材料であるため、耐摩耗性に優れた切削工具が必要です。 特に、高速度鋼や硬質合金製の切削工具がSUS材の切削に適しています。これらの工具は高い硬度を持ち、SUS材の加工により長期間耐えることができます。 注意しなければならない点は、切りくずの適切な除去や切削熱の対策です。SUS材は熱に弱いため、冷却液を使用して加工中の熱を逃がす必要があります。 以上のように、SUS材の切削加工には適切な切削工具の選択と適切な加工条件の確保が重要です。SUS切削の基本プロセス
SUS切削の基本プロセスは、まず適切な工具や切削条件を選択することから始まります。SUS材は耐食性や耐熱性に優れており、その特性を考慮して適切な切削工具を選ぶことが重要です。また、切削条件も適切に設定することで、効率的かつ精密な加工が可能となります。 例えば、高速度鋼や硬質合金を使用した切削工具を選択して、SUS材を効率的に削ることができます。さらに、適切な切削速度や切削深さを設定することで、加工時の摩耗や熱の影響を最小限に抑えることができます。 要するに、SUS切削においては、適切な工具と条件を選択することが重要です。これにより、高品質で効率的な加工が可能となり、加工精度や生産性を向上させることができます。加工速度とフィードレートの設定
切削加工において重要な要素は加工速度とフィードレートの設定です。切削速度が速すぎると工具が早く摩耗し、逆に遅すぎると材料が熱を持ち切れ味が悪化します。フィードレートは、一度にどれだけ材料を削るかを示し、適切なフィードレートを設定することで効率的な加工が可能となります。 例えば、SUS材を切削する際には適切な加工速度とフィードレートを選択する必要があります。適切な設定を行わないと加工精度が低下するだけでなく、工具の寿命も短くなる可能性があります。したがって、正確な加工条件を設定し、材料特性や工具の状態に注意しながら切削加工を行うことが重要です。ステンレス切削加工の技術的ポイント
ステンレス鋼は耐食性や強度に優れていますが、切削加工時に特有の課題が発生します。以下では、熱処理や加工精度の向上に関する重要な技術ポイントを解説します。
熱処理とその影響
項目 | 詳細 |
---|---|
熱処理の目的 | 強度、硬度、靭性、耐摩耗性の向上、内部応力の除去 |
ステンレス鋼の熱処理の種類 | 焼き入れ、焼き戻し、固溶化熱処理、時効硬化 |
加工への影響 | – 焼き入れ後は硬度が高くなり、切削性が低下。 |
– 焼き戻しにより硬度を調整し、加工性を改善。 | |
– 固溶化熱処理で耐食性と靭性が向上。 | |
注意点 | 熱処理により材料の変形が発生するため、後工程での仕上げが必要となる。 |
切削液の種類と使い方
SUS材の切削加工は、金属を精密に形作る際に重要です。切削液は切削加工において不可欠な要素です。切削液の主な種類には、水溶性切削液と油性切削液があります。水溶性切削液は冷却効果が高く、廃液処理が簡単です。一方、油性切削液は潤滑効果が高く、加工精度を向上させることができます。
切削加工を行う際には、適切な刃物と切削条件を選択することが重要です。例えば、高速鋼や硬質合金の刃物を選ぶことで、効率的な切削が可能となります。また、適切な切削条件を設定することで、材料の劣化を最小限に抑えることができます。
以上のポイントに留意しながら、SUS材の切削加工を行うことで、高精度な加工が可能となります。切削液の使い方や刃物の選択に注意を払いながら、効率的かつ精密な加工を行いましょう。
切削加工における精度向上のコツ
1. 切削工具の選定
- 推奨工具材質: 超硬工具やセラミック工具を使用。
- コーティング: TiNやTiAlNなどのコーティングにより摩耗を低減。
2. 切削条件の設定
- 切削速度: 過熱を防ぐため適切な低速設定。
- 送り速度: 高すぎると工具寿命が短縮、低すぎると仕上げ面に悪影響。
3. 冷却液の使用
- 高い熱伝導性の冷却液を使用し、加工時の発熱を抑制。
- 切削点へ直接供給し、潤滑と冷却効果を最大化。
4. クランプの工夫
- 工具やワークが振動しないように、しっかり固定する。
- 加工中の変形を防ぐため、応力を分散するクランプ方法を採用。
5. 加工手順の最適化
- 荒加工と仕上げ加工を明確に分け、精度向上を図る。
- 熱膨張を考慮し、加工工程を計画。
6. 仕上げ面の改善
- 切削後の表面粗さを改善するため、研削や研磨工程を追加。
- 精密なバリ取りで仕上がり精度を向上。
ステンレス加工におけるトラブルと対策
トラブル内容 | 原因 | 対策 |
---|---|---|
工具摩耗が激しい | 高硬度材料に対し工具が不適合。 | 超硬工具やコーティング工具を使用。 |
発熱による変形 | 切削速度や冷却不足。 | 適切な冷却液を使用し、速度を調整。 |
表面仕上げが粗い | 工具の摩耗や切削条件の不適合。 | 工具を交換し、仕上げ工程を見直す。 |
振動や騒音が発生 | 工具やワークの固定が不十分。 | クランプ方法を見直し、剛性の高い工具を使用。 |
まとめ
ステンレス鋼の切削加工では、材料特性に合わせた熱処理、工具の選定、加工条件の最適化が不可欠です。これらのポイントを抑えることで、加工精度の向上とトラブルの軽減が可能となります。
ステンレス切削加工のトラブルと解決方法
ステンレス切削加工では、材料特性や加工条件に起因するトラブルが発生することがあります。以下では、主なトラブルとその解決方法を解説します。トラブルと解決方法の概要
トラブル内容 | 主な原因 | 解決方法 |
---|---|---|
工具摩耗が激しい | – 硬度が高いステンレス鋼の特性 | – 耐摩耗性の高い超硬工具を使用。 |
– 切削速度が高すぎる。 | – 適切な低速での切削速度に調整。 | |
発熱による変形 | – 高速切削による発熱。 | – 冷却液を適切に供給し熱を抑制。 |
– クランプ不足でワークが歪む。 | – ワークの固定方法を見直し応力を分散。 | |
表面粗さが悪い | – 工具の摩耗や不適切な刃物角度。 | – 工具を新品に交換し刃物角度を最適化。 |
– 不十分な潤滑。 | – 高性能潤滑液を使用し供給量を増やす。 | |
切りくず排出が不良 | – 切りくずの形状が大きく絡みやすい。 | – 適切なチップブレーカー付き工具を選択。 |
– 冷却液不足で排出が悪化。 | – 冷却液の流量と供給方法を改善。 | |
振動や騒音が発生 | – 工具やワークの固定が不十分。 | – 強固なクランプや剛性の高い工具を使用。 |
– 機械剛性の不足。 | – 加工条件を見直し、加工速度を調整。 |
トラブル発生時の対応策
- 工具摩耗への対応
- 耐摩耗性のあるコーティング工具(例: TiN、TiAlN)を使用。
- 工具寿命を監視し、定期的に交換。
- 切削速度を適正に設定し、工具への負荷を軽減。
- 発熱や変形への対応
- 冷却液を切削点に直接供給することで熱を効果的に除去。
- 荒加工と仕上げ加工を分け、加工負荷を分散。
- ワークの取り付けを改善し、応力集中を防ぐ。
- 表面粗さ改善の対応
- 刃先の鋭利な工具を選択し、最適な送り速度を設定。
- 切削中に発生する微振動を防ぐため、機械剛性を高める。
- 表面仕上げ用の追加工程(例: 研削、研磨)を導入。
- 切りくず排出不良の対応
- チップブレーカー付きの工具を使用し、切りくずを小さく分断。
- 冷却液の供給方法を見直し、排出をスムーズにする。
- 切りくずの絡まりを防ぐため、加工のインターバルを調整。
まとめ
ステンレス切削加工では、トラブルの発生を未然に防ぐために、適切な工具、加工条件、冷却液の選択が重要です。また、トラブルが発生した際には原因を迅速に特定し、適切な対策を講じることで加工効率と仕上がり品質を向上させることが可能です。ステンレス加工のコスト削減方法
加工工程の最適化
SUS(ステンレス鋼)材料の切削加工は、精密な技術が必要です。切削工程を最適化することで、作業効率を向上させることができます。具体的には、適切な切削条件を設定することが重要です。例えば、適切な切削速度や切削深さを決定することで、材料の効率的な加工を実現できます。さらに、切削工具の選定も重要です。適切な切削工具を選ぶことで、材料への負荷を減らし、加工精度を高めることができます。注意点としては、切削時に生じる熱による変形やチッピングを防ぐため、十分な冷却や潤滑を行うことが重要です。切削加工においては、正確な工程管理と注意深い作業が求められます。工具寿命の延長テクニック
SUS材は、精密加工の際に重要な素材です。SUS材の切削加工方法には、注意点があります。適切な切削速度や切削量を調整することが重要です。切削速度が速すぎると刃物が摩耗しやすくなり、遅すぎると切削面が粗くなります。 また、切削冷却液を効果的に使用することも大切です。これにより切削時の熱を逃がし、刃物の寿命を延ばすことができます。さらに、適切な刃形や刃角を選択することも精密加工の鍵となります。 例えば、SUS材を加工する際には、適切な切削速度と冷却液の使用を心がけることが重要です。そのような注意点を守ることで、SUS材の切削加工において高い精度と効率を実現することができます。まとめ
SUS材を切削する際には、適切な切削条件を選択することが重要です。また、切削速度や切削深さ、切削用具の選択など、様々な注意点があります。SUS材は硬い材料であるため、切削時には適切な冷却や潤滑を行うことが必要です。素材の特性を考慮しながら、正確な切削工程を設定することが加工の品質を向上させます。 精密加工においては、切削工具の適切な選択が重要です。また、適切な切削速度や刃先の形状なども考慮する必要があります。加工の際には、細かな注意点に留意しつつ、最適な切削条件を設定することで、高品質な加工が可能となります。耐食性に優れたSUS素材の特性と選び方
SUS(ステンレス鋼)とは?
SUS素材の基本的な理解
SUS素材は、耐食性に優れた特性を持つ素材です。この特性から、食品加工業や医療機器など幅広い分野で使用されています。例えば、調理器具や食器、医療用具など、日常生活でも身近に使われています。SUS素材は錆びにくく、清潔で衛生的な面でも優れています。 SUS素材を選ぶ際には、使用する環境や目的に合った適切な種類を選ぶことが重要です。例えば、耐熱性や耐食性が求められる場合は、適切なグレードのSUS素材を選ぶことが必要です。さらに、加工しやすさや強度なども考慮して選択することが大切です。 適切なSUS素材を選ぶことで、耐久性や安全性を確保できるだけでなく、製品の品質向上にもつながります。そのため、使用目的や環境に応じて適切なSUS素材を選ぶことが重要です。SUSの歴史と発展
SUS素材は、その耐食性と信頼性で広く利用されています。SUSは、ステンレス鋼の一種であり、錆びにくく、強度が高い特性を持っています。そのため、食品加工業や建築業など幅広い産業で使用されています。 SUSの歴史は古く、第二次世界大戦後に開発されました。当初は軍事用途で使用されていましたが、その後産業用途に広がりました。現在では、様々な形状や厚さのSUS製品が市場で利用されています。 例えば、キッチン用品や自動車部品、建築材料などにSUS素材が使われています。その耐久性や衛生面からも、多くの場面で重宝されています。 SUS素材を選ぶ際には、使用する環境や目的に合わせて適切な種類を選択することが重要です。しっかりとした選定を行うことで、SUS素材の特性を最大限に活かすことができます。身近な金属素材としてのSUS
耐食性に優れたSUS素材は、日常生活で身近な金属素材の一つです。SUSはステンレス鋼の一種であり、錆びにくく、使い勝手がよいため、様々な場面で利用されています。例えば、キッチン用具や食器、建築材料など幅広い分野でSUS素材が採用されています。 SUS素材を選ぶ際には、耐食性だけでなく、強度や加工性も考慮することが重要です。特に、食品関連のアイテムや水回りの設備など、衛生面が重要な場所ではSUS素材の選定が特に重要です。 耐久性や美観を求める場合には、SUS素材が適しています。さまざまな状況に対応できるSUS素材は、日常生活を快適にするために欠かせない素材の一つです。SUSの種類と特徴
SUS素材の分類
分類 | 特徴 | 主な用途 |
---|---|---|
オーステナイト系 | 耐食性に優れ、非磁性。加工しやすく、低温でも脆くならない。 | キッチン用品、食品加工機械、医療器具 |
フェライト系 | 強度と耐熱性が高く、コストが比較的低い。磁性を持ち、溶接性はやや劣る。 | 自動車部品、家庭用器具 |
マルテンサイト系 | 高い強度と硬度を持ち、耐摩耗性に優れるが、耐食性はやや低い。 | 刃物、ばね、工具 |
析出硬化系 | 高い強度と耐食性を兼ね備え、熱処理によりさらに強度を向上可能。 | 航空機部品、精密機械 |
二相系(デュプレックス系) | オーステナイト系とフェライト系の特徴を併せ持ち、強度と耐食性に優れる。 | 化学プラント、海洋構造物 |
代表的なSUS材料の種類
材料名 | 特徴 | 主な用途 |
---|---|---|
SUS304 | 汎用性が高く、耐食性と加工性に優れる。オーステナイト系の代表格。 | 台所用品、建築材料、医療機器 |
SUS316 | SUS304より耐食性が高く、塩水や化学環境に強い。 | 化学プラント、海洋設備 |
SUS430 | フェライト系で耐熱性が高いが、耐食性はオーステナイト系よりやや劣る。 | 家電製品、自動車部品 |
SUS410 | マルテンサイト系で強度と硬度が高く、耐摩耗性が優れるが、耐食性は低い。 | 刃物、工具、機械部品 |
SUS329J1 | 二相系ステンレスで、塩素環境における耐食性が高く、強度と延性を兼ね備える。 | 化学プラント、オフショア構造物 |
各種SUS素材の用途と特性
用途 | 適したSUS材質 | 特性 |
---|---|---|
食品加工機械 | SUS304, SUS316 | 耐食性と加工性が高く、食品衛生に適合。化学薬品や塩水への耐性が必要な場合はSUS316を選択。 |
建築材料 | SUS304, SUS430 | 耐久性と美観を兼ね備える。SUS430はコストパフォーマンスが高く、屋内用途に適する。 |
自動車部品 | SUS430, SUS410 | 強度と耐熱性が必要な部分に最適。SUS410は工具や高強度部品に向く。 |
海洋設備 | SUS316, SUS329J1 | 塩害や腐食環境に強く、長寿命を確保。 |
精密機械 | SUS304, SUS631(析出硬化系) | 高精度で強度が必要な部分に適する。加工性と耐久性を重視。 |
詳細情報:SUS材料を選定する際のポイント
- 使用環境
- 塩害や化学薬品環境が予想される場合は、SUS316や二相系を選択。
- 高温環境ではフェライト系や二相系が適する。
- 加工性とコスト
- 加工性が求められる場合はSUS304を選ぶ。
- コストパフォーマンスを重視する場合は、フェライト系のSUS430が適する。
- 耐久性と安全性
- 耐摩耗性が必要な用途では、マルテンサイト系のSUS410を選択。
- 食品や医療用途には、非磁性で耐食性に優れるオーステナイト系が推奨される。
耐食性に優れたSUS素材の選び方
耐食性の基礎知識
項目 | 説明 |
---|---|
耐食性とは | 素材が腐食に対して耐え、劣化しにくい性質のこと。 |
腐食の原因 | 化学薬品、塩水、酸性・アルカリ性溶液、湿度や高温環境など。 |
ステンレス鋼の耐食性 | クロム含有量が高いほど耐食性が向上。酸化被膜を形成し、表面を保護する。 |
代表的な耐食性グレード | SUS304(汎用)、SUS316(塩水耐性)、SUS329J1(二相系で優れた耐食性)。 |
環境に合わせたSUS素材の選定
使用環境 | 適したSUS素材 | 選定理由 |
---|---|---|
塩水環境 | SUS316 | 塩水による腐食に強いモリブデンを含有。 |
酸性環境 | SUS316, SUS329J1 | 耐酸性に優れ、化学薬品にも対応可能。 |
高湿度環境 | SUS304, SUS316 | 酸化被膜により錆びにくく、湿気に強い。 |
高温環境 | SUS310S | 高温酸化耐性が高い。 |
海洋設備 | SUS316, SUS329J1 | 塩害に強く、長期的な耐久性を確保。 |
食品産業 | SUS304, SUS316 | 非毒性で衛生的。塩分や酸性食品に対応可能。 |
耐食性を左右する要素
要素 | 説明 |
---|---|
クロム含有量 | クロムの含有量が多いほど耐食性が向上。 |
モリブデン含有量 | 塩水や化学薬品への耐性を強化する重要な成分。 |
表面処理 | 酸洗いや電解研磨による表面仕上げが耐食性を向上させる。 |
溶接の品質 | 溶接部の品質が低いと局部的な腐食(粒界腐食)が発生しやすい。 |
環境条件 | 温度、湿度、塩分濃度などが腐食の進行速度に影響を与える。 |
詳細情報:環境に応じたSUS素材の選び方
- 耐塩水性が求められる場合
- 海洋環境や塩分の多い食品加工では、モリブデンを含むSUS316が最適。
- 二相系のSUS329J1は、さらに高い塩水耐性を提供。
- 化学薬品への曝露が多い場合
- 酸性・アルカリ性の薬品に接触する環境では、SUS316や二相系ステンレスが推奨される。
- 硫酸や塩酸環境では特定の合金が必要になる場合がある。
- コストと性能のバランス
- 一般的な耐食性が求められる用途では、SUS304がコストパフォーマンスに優れる選択肢。
- 長期間の耐久性を確保する場合は、多少のコストアップを考慮して耐食性グレードを選ぶ。
- 表面仕上げの重要性
- 鏡面仕上げや酸洗処理を行うことで、腐食リスクを大幅に軽減可能。
- 溶接後の処理が不十分な場合、溶接部での腐食が進行しやすい。
ステンレスの耐食性と腐食現象
耐食性のメカニズム
項目 | 説明 |
---|---|
耐食性の原理 | ステンレスは表面に形成される「不動態被膜(酸化被膜)」によって腐食を防ぐ性質を持つ。 |
クロムの役割 | 鉄に11%以上のクロムを含有することで、酸素と反応し酸化被膜を生成。腐食の進行を抑制。 |
不動態被膜の特性 | 薄く透明で硬い膜。自己修復能力を持ち、傷がついても酸素がある環境で再生可能。 |
- 不動態被膜の生成条件
- クロム含有量:11%以上が必要。
- 環境条件:酸素が十分に供給されること。
- 被膜の破壊原因
- 高塩分環境:塩素イオンが被膜を侵食。
- 酸性環境:硫酸や塩酸などが膜を劣化させる。
- 機械的損傷:摩擦や衝撃で膜が剥がれる。
腐食の種類とその発生条件
腐食の種類 | 説明 | 発生条件 |
---|---|---|
全面腐食 | 表面全体が均一に腐食する。 | 強酸やアルカリなどに長時間さらされる。 |
孔食 | 小さな穴が局所的に発生する腐食。 | 塩化物イオン(例:塩水環境)が存在する場合。 |
粒界腐食 | 結晶粒界で腐食が進行する現象。 | 溶接や熱処理による炭化物析出が原因。 |
応力腐食割れ(SCC) | 応力と腐食の複合作用による亀裂発生。 | 高温・高圧下で応力が加わり、塩素や硫黄成分に触れる環境。 |
隙間腐食 | ボルトやガスケットの隙間などで局所的に発生する腐食。 | 酸素供給が制限され、不動態被膜が再生されない状態。 |
- 孔食
- 主に塩素イオンが原因。
- 発生すると進行が早く、見た目以上に深刻なダメージを与える。
- 粒界腐食
- 特にSUS304などのオーステナイト系ステンレスに発生しやすい。
- 溶接部の適切な熱処理が予防に重要。
- 隙間腐食
- 酸素供給の不足が主因。
- 設計段階で隙間を減らすことが効果的。
腐食を防ぐための対策
対策内容 | 詳細 |
---|---|
適切な素材選定 | 使用環境に適した耐食性の高いグレード(例:SUS316、SUS329J1)を選ぶ。 |
表面処理の実施 | 酸洗いや電解研磨で不動態被膜を強化。 |
設計上の工夫 | 隙間や水溜まりを防ぐ設計を行い、腐食の発生リスクを低減。 |
環境の管理 | 塩分や酸性度を低減する。例:水質管理、塩害環境での保護塗装。 |
熱処理の適用 | 溶接後に適切な熱処理を施すことで、粒界腐食のリスクを軽減。 |
定期的な点検と保守 | 腐食の兆候を早期に発見し、適切に対処する。 |
- 素材選定のポイント
- 塩水環境:SUS316またはSUS329J1。
- 酸性環境:モリブデンを多く含む素材。
- 設計の工夫
- 隙間を作らないようなジョイント設計。
- 水はけが良い構造にすることで腐食リスクを低減。
- 保守管理
- 高湿度環境では、定期的に表面状態を点検。
- 表面の酸洗いを定期的に行うことで耐食性を向上。
金属加工とSUS素材
SUS加工の方法と特徴
加工方法 | 特徴 | 主な用途 |
---|---|---|
切削加工 | 高硬度で難削材だが、適切な工具と条件で高精度な仕上がりが可能。 | 精密部品や複雑な形状の加工。 |
研磨加工 | 表面を滑らかに仕上げることで耐食性と見た目を向上。 | 表面仕上げや装飾用途、耐食性を必要とする部品。 |
溶接加工 | SUS特有の熱膨張率に注意が必要だが、適切な条件で強固な接合が可能。 | 配管、タンク、フレームなどの大型構造物。 |
プレス加工 | 延性が高く、複雑な形状への加工が可能。 | 薄板の加工や自動車部品、家電部品。 |
レーザー加工 | 高精度で非接触加工が可能。特に薄板SUSに適する。 | 精密機器やデザイン性の高い製品。 |
- 切削加工のポイント
- 高硬度に対応した専用工具を使用する。
- 冷却剤を十分に供給して熱変形を防ぐ。
- 研磨加工の利点
- 表面の光沢と耐食性が向上する。
- 装飾的な仕上がりが求められる場面で有効。
- 溶接加工の注意点
- 溶接熱により粒界腐食が発生する可能性があるため、熱処理が推奨される。
- 適切なフィラー材を選定することで接合部の強度を確保。
加工時の注意点と対策
注意点 | 問題点 | 対策 |
---|---|---|
熱変形 | SUSは熱伝導率が低く、加工熱で変形しやすい。 | 冷却剤の十分な使用、加工速度の調整。 |
工具摩耗 | SUSの高硬度により工具の摩耗が早い。 | コーティング工具や耐摩耗性工具を使用。 |
加工硬化 | 加工中に硬化が進み、次工程が困難になる場合がある。 | 低速での加工と切削深さの調整。 |
バリの発生 | 切削や打ち抜き加工でバリが発生しやすい。 | バリ取り工程の追加や適切な刃物選択。 |
表面傷の発生 | 加工中に工具や素材が接触し表面に傷がつく可能性。 | 作業台や工具の清潔さを保ち、保護フィルムを活用。 |
- 熱変形の防止策
- 加工中に適切な冷却剤を使用して熱を抑制。
- クランプ位置を適切に設定し、応力を均等に分散。
- 工具摩耗への対応
- 耐摩耗性の高い工具(例:超硬合金、PCD)を選定。
- 工具寿命を定期的に点検し交換を実施。
- 加工硬化を抑える方法
- 一回の切削量を増やし、加工時間を短縮。
- 加工速度と送り速度を最適化して硬化を防止。