SUS303の高精度仕上げ加工方法を探る
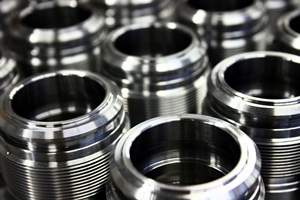
1. SUS303の特性と用途
1-1. SUS303とは何か
SUS303はオーステナイト系ステンレス鋼の一種で、JIS規格で規定されているSUS304を基に、被削性(切削加工性)を向上させるために硫黄(S)やセレン(Se)を添加した鋼材です。非磁性でありながら、機械加工性が高く、精密部品やネジなどの製造に適しています。
1-2. SUS303の利点と特性
- 優れた被削性:硫黄添加により切りくずが細かくなり、加工性が向上。
- 耐食性:SUS304と比較して若干劣るものの、日常使用には十分な耐腐食性能。
- 美しい仕上がり:高精度な仕上げ加工が可能で、光沢のある表面が得られやすい。
- 非磁性:磁性を帯びにくいため、電子機器などにも適用可能。
1-3. SUS303の用途
- 精密ネジ、ナット、ボルト
- 計測機器の小型部品
- 医療用機器の構成パーツ
- 自動車用部品、電気機器の取付部材
SUS303は大量生産に向いた素材であり、自動旋盤などを用いた連続加工に適しています。
1-4. 他のステンレス鋼との違い
SUS304と比較すると、SUS303は硫黄の添加により加工性が高い一方、耐食性はやや劣ります。SUS316と比べると、耐薬品性や耐海水性では劣るものの、コストと加工性の面で優れた選択肢となります。
2. SUS303の切削加工方法
2-1. 切削加工の種類
SUS303に適した主な切削加工は以下の通りです:
- 旋盤加工(Turning):円筒形状の加工に最適。
- フライス加工(Milling):溝加工や平面仕上げに有効。
- ボーリング・リーマ加工:高精度な穴仕上げ。
- タッピング・ネジ切り加工:機械部品製作に不可欠。
2-2. フライス加工の手法
SUS303のフライス加工では、硬度が比較的低いため工具への負荷が小さく、スムーズな切削が可能です。高速回転と適切な切り込み量を組み合わせることで、表面粗さと加工効率のバランスが取れます。超硬工具やコーティング済みエンドミルの使用が一般的です。
2-3. 旋盤加工の基本技術
旋盤加工では、SUS303の被削性の高さにより、切りくず処理がしやすく工具寿命も比較的長く保てます。高回転数と切削油の適正供給が、仕上がり精度と工具摩耗を左右します。刃物の突き出し量は最小限に抑え、ビビリの防止が重要です。
2-4. 切削工具の選定と管理
切削工具は被削材との相性が重要で、SUS303の場合は以下が推奨されます:
- 超硬合金工具:長寿命かつ高精度。
- TiAlNコート工具:耐熱性に優れ、摩耗を抑制。
- 工具の定期交換と研磨管理:精度維持と加工コストの最適化に貢献します。
3. SUS303の高精度仕上げ技術
3-1. 仕上げ加工の目的
仕上げ加工は寸法精度や表面粗さを向上させ、製品の信頼性や耐久性を確保するために行われます。SUS303は高精度仕上げがしやすい素材であり、精密機器部品に多用されます。
3-2. 仕上げ方法の種類
- 研削加工(Grinding):数ミクロン単位の精度調整。
- バフ研磨(Buffing):鏡面仕上げに最適。
- 電解研磨(Electropolishing):酸化皮膜を除去し、表面を均一に。
- ホーニング・ラッピング:内径や平面の極限仕上げに使用。
3-3. 精度向上のための工夫
- 振動抑制と剛性確保:加工機のセッティングが重要。
- 温度管理:熱変形を防ぐため、加工環境の温度安定化を図る。
- 寸法測定とフィードバック制御:インプロセス検査で品質保証。
3-4. 冷却と潤滑の重要性
SUS303の加工では切削熱の管理が重要です。適切な冷却剤や潤滑剤の使用により、工具寿命を延ばし、熱膨張による寸法誤差を抑制できます。特に微細加工や連続加工では、冷却液の循環性能と供給方法が製品精度に直結します。
4: 加工硬化とその対策
4-1: 加工硬化の原因
加工硬化は、SUS303のようなステンレス鋼を切削や曲げ加工する際に、金属の結晶構造が変形し硬くなる現象です。これにより材料の塑性変形能が低下し、脆くなることがあります。加工硬化は主に塑性変形による格子欠陥の蓄積が原因で、加工速度や工具の摩耗、加工方法によっても影響されます。
4-2: 加工硬化の影響と問題
加工硬化が進行すると、工具の摩耗が早まったり、加工割れや亀裂が発生しやすくなります。また、加工後の材料は硬くてもろいため、後工程での加工や組み立てが困難になる場合があります。製品の性能や寿命にも悪影響を与えかねないため、適切な管理が必要です。
4-3: 対策としての熱処理
加工硬化の対策には、焼なましなどの熱処理が有効です。熱処理を行うことで、加工によって生じた内部応力や格子欠陥を解消し、金属組織を再結晶化させることができます。これにより、材料の延性が回復し、加工硬化の悪影響を軽減可能です。
4-4: 硬度向上のための方法
一方で、硬度を向上させるためには、制御された熱処理や表面硬化処理(例:窒化処理、レーザー硬化)が用いられます。これにより、耐摩耗性や耐久性が向上し、特定の用途に適した性能を発揮します。適切な熱処理条件の選定が製品品質の鍵となります。
5: SUS303を用いた部品製作
5-1: 部品設計のポイント
SUS303は加工性に優れるため複雑形状の部品製作に適していますが、耐食性は若干劣るため使用環境を考慮した設計が必要です。特に切削時の加工硬化を考慮し、加工余裕を確保したり、応力集中部の設計に注意を払うことが重要です。
5-2: 製作所の選び方
SUS303の加工経験が豊富な製作所を選ぶことが品質確保のポイントです。特に切削加工や熱処理設備が充実しているか、加工硬化に対する知識や対応力があるかを確認すると良いでしょう。納期やコスト面でも信頼できるパートナー選定が必要です。
5-3: 加工時の注意点
加工時には工具の摩耗を防ぐため、適切な切削条件(速度・送り・切削液の選定)を守ることが求められます。また、加工硬化の影響を受けやすいため、加工段階ごとに品質チェックを行い、過度な応力や熱の発生を抑えることが大切です。
5-4: 検査と品質管理
完成した部品は寸法検査だけでなく、表面状態や硬度測定を含めた品質管理が必要です。加工硬化の影響や熱処理の適正を確認することで、製品の信頼性を高めることができます。トレーサビリティの確保も重要な管理項目です。
6: SUS303と関連する技術
6-1: 焼き入れの効果
SUS303は一般的に耐食性を優先し焼き入れ処理はあまり行いませんが、特定の用途では焼き入れによって硬度と耐摩耗性を向上させることがあります。焼き入れにより金属組織が変化し、表面硬度が上がることで耐久性が高まる一方、加工硬化や割れのリスクを考慮した管理が必要です。
6-2: コーティング技術の利点
SUS303の耐摩耗性や耐腐食性を補完するため、表面に各種コーティングを施す技術が発展しています。例えば、PVD(物理蒸着)コーティングや DLC(ダイヤモンドライクカーボン)コーティングは、耐摩耗性を飛躍的に向上させるだけでなく、摩擦低減や耐薬品性の改善にも寄与します。
6-3: 摩耗対策と持続性
機械部品として使用されるSUS303は摩耗が避けられない課題です。摩耗対策としては、熱処理、表面改質、適切な潤滑管理が重要です。これらにより部品寿命が延び、メンテナンス頻度の低減やコスト削減につながります。また、摩耗粉の発生を抑え環境負荷軽減にも貢献します。
6-4: 進化する加工技術
近年では高精度・高効率を追求するため、5軸マシニングやレーザー加工、ワイヤーカット放電加工など多様な加工技術がSUS303にも応用されています。これにより複雑形状の製作や加工時間の短縮、加工品質の向上が可能となり、製造の柔軟性が高まっています。
7: 環境とSUS303加工の関係
7-1: 環境に優しい加工技術
SUS303加工においても環境負荷の低減は重要なテーマです。切削液の使用量削減や水溶性切削液の導入、省資源・省エネルギーの加工手法の採用など、環境に配慮した加工技術が拡大しています。
7-2: エネルギー効率の追求
加工機械の省エネ設計や運用効率の向上は、SUS303製造現場でのエネルギー使用量削減に直結します。最新のインバータ制御やIoT技術を活用した稼働管理により、無駄な稼働時間の削減や最適な加工条件の設定が可能となっています。
7-3: 廃棄物管理とリサイクル
加工時に発生する切粉や廃材の適切な分別・リサイクルも環境負荷低減に不可欠です。SUS303はリサイクル性に優れており、金属リサイクル率が高いため、廃棄物の資源循環に寄与します。工場全体での廃棄物管理システムの構築も進んでいます。
7-4: 持続可能な製造プロセス
持続可能性を考慮した製造プロセスの導入は、環境保護と経済性の両立に繋がります。SUS303加工においても、材料の無駄削減、エネルギー効率化、環境負荷の低減に重点を置いた生産体制の確立が求められており、今後も技術革新が期待されます。