析出硬化処理とは?材料の強度を最大化する工業プロセスの解説
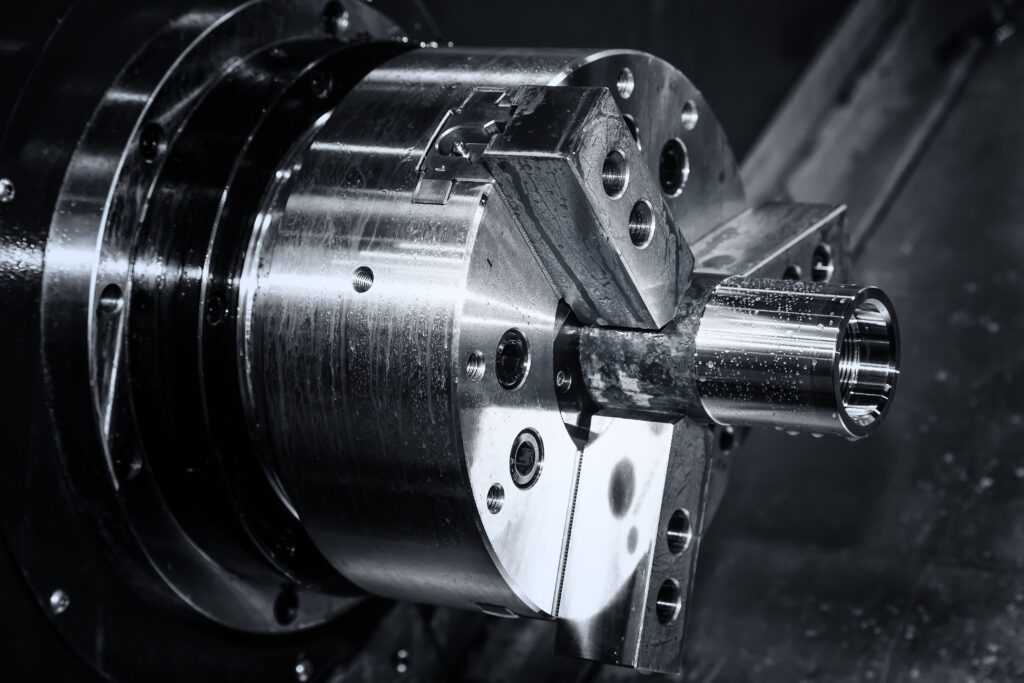
- 他の硬化処理(焼入れ・焼戻し、浸炭処理、窒化処理など)と異なり、析出硬化処理は主に非鉄金属に適用される点が特徴。
- 焼入れは鋼のマルテンサイト変態によって硬化するが、析出硬化は析出物による物理的な障害効果による。
- 浸炭や窒化は表面のみの硬化だが、析出硬化は材料全体に効果が及ぶ。
- 処理温度は比較的低温であるため、寸法変化が少なく、精密部品の加工後処理に適している。
- 軽量でありながら高強度が求められる構造部材に特に有効である。
Contents
析出硬化ステンレスのメカニズム
ステンレス鋼の種類と特性
- ステンレス鋼は主に以下の4種類に分類される:
- オーステナイト系:非磁性・加工性・耐食性に優れる。代表例:SUS304。
- フェライト系:磁性あり・熱伝導性良好。代表例:SUS430。
- マルテンサイト系:熱処理で硬化可能。代表例:SUS420。
- 析出硬化系:高強度・高耐食性を兼ね備える。代表例:SUS630(17-4PH)。
- 析出硬化ステンレスは、他の系に比べて強度と耐食性のバランスが非常に優れているため、航空機部品や精密機械部品などに用いられる。
析出硬化ステンレスの組成と構造
- 代表的な析出硬化ステンレス(SUS630=17-4PH)は、以下のような組成を持つ:
- Cr(クロム):耐食性向上
- Ni(ニッケル):オーステナイト安定化
- Cu(銅)・Al(アルミ):析出硬化元素として機能
- Nb(ニオブ)・Ti(チタン)など:炭化物形成に寄与し強度アップに貢献
- 構造は、マルテンサイト基に析出硬化相(CuやNiAl等)が微細に分散した構造となっている。
熱処理による強度と硬さの向上
- 溶体化処理:1050℃程度で急冷することで、単一なマルテンサイト組織を得る。
- 時効処理(析出処理):約480~620℃で数時間保持することで、析出物が生成され、硬度と強度が向上する。
- 析出物の効果:
- 析出物が転位の移動を妨げることで、金属組織の塑性変形を抑制。
- これにより、引張強さ・硬度・耐摩耗性が大幅に向上する。
- 同時に、寸法安定性にも優れた特性を発揮する。
- このメカニズムにより、加工性と高い機械的強度が両立可能となり、様々な産業分野で利用されている。
金属の時効と析出硬化処理
時効処理の定義と目的
- 時効処理とは:金属材料において、加熱または常温で一定時間保持することで、組織中に微細な析出物を生成させ、機械的性質(特に強度や硬さ)を向上させる処理のこと。
- 目的:
- 金属の引張強さ・硬度の向上
- 耐摩耗性・耐熱性の向上
- 微細構造を制御し、寸法安定性や靭性を確保する
時効処理と析出硬化処理の比較
- 共通点:
- どちらも微細な析出物の生成を利用し、金属の強化を目的とする。
- 材料の構造内部で析出反応を起こし、転位の動きを制御することで機械的特性を高める。
- 違い:
- 時効処理はより広義の概念であり、析出硬化もその一種に含まれる。
- 析出硬化処理は、特に溶体化処理 + 時効処理の2段階で行うことが多い。
- 析出硬化処理では、意図的に合金元素を設計し、特定の析出物(Ni3Al, Cu, Cr等)を得るようにする。
時効処理の工業的応用
- 時効処理は、以下のような合金や分野で広く応用されている:
- アルミニウム合金:
- 例:2024, 6061, 7075系など
- 航空機、精密機械部品、自動車構造部材に使用される
- チタン合金:
- 時効によって引張強さを高め、医療用インプラントや航空機部品に応用
- ニッケル基超合金:
- 耐熱性・強度の向上に寄与し、ジェットエンジンや発電用タービンに用いられる
- 析出硬化型ステンレス鋼(17-4PHなど):
- 高強度・高耐食性が求められる構造部品やシャフト類に活用されている
金属材料が変形するしくみ
金属の結晶構造と変形
- 金属は原子が規則正しく並んだ結晶構造をもつ。
- 主な結晶構造には以下がある:
- 体心立方構造(BCC)
- 面心立方構造(FCC)
- 六方最密構造(HCP)
- これらの構造は、金属の変形しやすさ(延性や塑性)に影響する。
- 変形は、転位(結晶内の欠陥)が移動することで生じる。
外力による金属の変形過程
- 金属に外力を加えると、最初は原子間の距離がわずかに変わることで応力に耐える。
- 応力が限界を超えると、転位が滑るように動き、結晶構造がずれて変形が始まる。
- このとき、金属全体が目に見える変形を起こすようになる。
- 一度転位が動き始めると、比較的少ない力でも連鎖的に変形が広がる。
塑性変形と弾性変形の違い
- 弾性変形:
- 外力を除くと、元の形に戻る変形。
- 原子間の距離が変わるが、結晶構造は保たれている。
- 弾性限界を超えない範囲でのみ発生。
- 塑性変形:
- 外力を除いても、元の形に戻らない永久変形。
- 結晶内の転位が移動し、構造自体がずれる。
- 加工や成形において最も重要な変形。
金属材料の強化方法
冷間加工による強化
- 金属を常温で圧延、引張、圧縮などの塑性変形を加えることで強度を高める方法。
- 転位密度が増加し、転位の移動が困難になることで硬化する。
- 一般的に「加工硬化」や「ひずみ硬化」とも呼ばれる。
- デメリットとして、加工が進むと延性が低下する。
合金化による強化
- 複数の金属元素を組み合わせて、金属の構造内に異種原子を導入する。
- 異種原子が格子ひずみを生じ、転位の移動を妨げる。
- 固溶強化(固溶体の形成)や析出強化(微細な粒子の析出)などの効果がある。
- 鉄に炭素を加える鋼や、アルミニウムに銅やマグネシウムを加える例が代表的。
熱処理による強化
- 加熱と急冷、あるいは特定の温度での保持によって、金属の組織を変化させる手法。
- 焼入れ、焼戻し、焼なまし、析出硬化などの手法がある。
- 強度だけでなく、硬さや耐摩耗性などの調整も可能。
表面処理による強化
- 金属表面に限定して処理を施し、表面の硬度や耐食性を高める方法。
- 代表的な方法には、浸炭、窒化、ショットピーニング、めっき、コーティングなどがある。
- 表面のみを強化するため、内部の靱性や延性を保ったまま高性能化できる。
析出硬化処理の工業的応用
航空宇宙産業での応用
- 目的と要求性能:
- 航空宇宙産業では、使用される材料に対して高い強度、軽量性、耐熱性、耐食性が求められます。
- 析出硬化処理を施した材料は、これらの要求に最適な特性を持ち、過酷な環境で使用されます。
- 適用例:
- 航空機部品: 航空機の機体やエンジン部品は高強度と軽量性を兼ね備えた素材が必要です。析出硬化型のアルミニウム合金(例:2024系、7075系アルミニウム合金)は、非常に高い強度を持ちつつ、軽量性も保持できるため、航空機の構造部品や翼、エンジン部品に使用されています。
- ロケット部品: ロケットのエンジン部品や推進装置には、極めて高い耐熱性と強度が求められます。析出硬化アルミニウムやチタン合金(Ti-6Al-4Vなど)は、ロケットの耐熱部品や構造部材に適用され、長期間の耐用性と安定性を提供します。
- 金属3Dプリンティング: 航空宇宙産業では、金属3Dプリンティング技術が活用され、析出硬化型合金がプリントされることで、従来の製造方法よりも軽量で強度のある部品が製造されています。
自動車産業での応用
- 目的と要求性能:
- 自動車産業では、燃費効率と安全性を両立させるために、軽量化と強度の向上が非常に重要です。また、耐摩耗性や耐久性も必須要素です。
- 適用例:
- 車体構造材: 自動車の車体やシャーシには軽量で高強度な材料が求められます。析出硬化型アルミニウム合金(例:6000系、7000系)は、優れた強度と軽量性を持ち、車両構造材や衝突エネルギー吸収部品に使用されます。
- サスペンション部品: 自動車のサスペンション部品には高い強度と靱性が必要です。析出硬化処理されたアルミニウム合金や鋼合金は、サスペンション部品やアクスル、シャフトなどに使われ、長期間の使用に耐えることができます。
- エンジン部品: 自動車エンジンの重要な部品(ギア、シャフト、バルブ、ピストンなど)は、高い耐摩耗性と耐熱性を持つ材料が使用されます。析出硬化した鋼やアルミニウム合金はこれらの部品に適用され、エンジンの性能向上に寄与しています。
- 電動車部品: 電気自動車(EV)のバッテリーパックやモーターにおいても、析出硬化処理された軽量な合金が採用され、電動車のパフォーマンス向上とバッテリー効率の向上に貢献しています。
医療器具への応用
- 目的と要求性能:
- 医療機器においては、生体適合性、強度、耐食性、耐久性が特に重要です。特にインプラントや手術器具などは、安全性と信頼性が求められます。
- 適用例:
- 手術器具: 高精度な手術器具や医療用工具には、優れた耐食性と強度が必要です。析出硬化型ステンレス(例:17-4PHステンレス鋼)は、手術用メス、鉗子、ペンチ、ドリルビットなどの器具に使用され、高い耐摩耗性と耐腐食性を発揮します。
- インプラント部品: 生体内で使用されるインプラント(人工関節、歯科インプラントなど)にも析出硬化型ステンレスやチタン合金が使用されます。これにより、インプラント部品の強度や耐久性が向上し、体内での長期間の使用が可能となります。
- 歯科用工具: 歯科用の治療器具(スケーラー、カッター、ドリルなど)にも析出硬化ステンレスが使用され、鋭さと耐久性を確保しています。これにより、高精度の治療が可能となり、患者に対する安全性が向上します。
その他の工業分野での応用
- 金型産業: 金型は製品の精度と耐久性を決定づける重要な部分です。析出硬化型鋼(例:P20、H13など)は金型の製作に使用され、長寿命と優れた耐摩耗性を提供します。
- 電子機器: 析出硬化型材料は、携帯電話やコンピュータ部品などの電子機器においても使用され、信号の伝達精度や機器内部の熱管理に寄与しています。
- 鉄道産業: 鉄道車両の車輪、シャフト、ギアなどに使用される材料にも析出硬化型合金が使用され、高強度と耐摩耗性を確保しています。
まとめ
析出硬化処理は、材料の強度を最大化する工業プロセスです。この処理は、金属合金を熱処理して、微細な析出物を生成し、材料の硬度や強度を向上させることを目的としています。このプロセスは、材料の特性を向上させるために広く使用されており、様々な工業製品の製造において重要な役割を果たしています。析出硬化処理とは、材料の強度を最大化する工業プロセスの一つです。この処理方法は、材料を加熱して固溶体を形成し、その後急冷することで固溶体内に微小な析出物を生成させることで硬度を向上させます。 この記事では、析出硬化処理の基本的な仕組みやその効果、どのように行われるか、そしてなぜ材料の強度を最大化するのに適しているのかについて詳しく解説していきます。 材料の性能や信頼性を高めるためには、析出硬化処理が欠かせない工程となります。その重要性やメカニズムについて正しく理解することで、製品の品質向上や耐久性向上につながることでしょう。さらに、今後の工業プロセスにおいても、析出硬化処理の活用はますます重要性を増していくでしょう。析出硬化処理とは
析出硬化処理の基本概念
- 析出硬化処理とは、金属の内部に微細な析出物を生成させることで、強度や硬度を向上させる熱処理法。
- この処理は、「溶体化処理 → 急冷 → 時効処理」の3段階を経て、析出物が材料内部で転位の動きを妨げることにより硬化効果が得られる。
- 主にアルミニウム合金、ニッケル合金、銅合金、析出硬化系ステンレス鋼などが対象となる。
析出硬化処理の歴史的背景
- 析出硬化処理の原理は、1906年にドイツのヴィルムがアルミニウム合金の自然時効硬化を発見したことに端を発する。
- 1920年代には工業的に利用され始め、特に航空機用アルミ材料として需要が急増。
- 現代では、航空・宇宙・自動車・電子機器・医療機器などの分野で幅広く応用されている。
析出硬化処理と他の硬化処理との違い
- 他の硬化処理(焼入れ・焼戻し、浸炭処理、窒化処理など)と異なり、析出硬化処理は主に非鉄金属に適用される点が特徴。
- 焼入れは鋼のマルテンサイト変態によって硬化するが、析出硬化は析出物による物理的な障害効果による。
- 浸炭や窒化は表面のみの硬化だが、析出硬化は材料全体に効果が及ぶ。
- 処理温度は比較的低温であるため、寸法変化が少なく、精密部品の加工後処理に適している。
- 軽量でありながら高強度が求められる構造部材に特に有効である。
析出硬化ステンレスのメカニズム
ステンレス鋼の種類と特性
- ステンレス鋼は主に以下の4種類に分類される:
- オーステナイト系:非磁性・加工性・耐食性に優れる。代表例:SUS304。
- フェライト系:磁性あり・熱伝導性良好。代表例:SUS430。
- マルテンサイト系:熱処理で硬化可能。代表例:SUS420。
- 析出硬化系:高強度・高耐食性を兼ね備える。代表例:SUS630(17-4PH)。
- 析出硬化ステンレスは、他の系に比べて強度と耐食性のバランスが非常に優れているため、航空機部品や精密機械部品などに用いられる。
析出硬化ステンレスの組成と構造
- 代表的な析出硬化ステンレス(SUS630=17-4PH)は、以下のような組成を持つ:
- Cr(クロム):耐食性向上
- Ni(ニッケル):オーステナイト安定化
- Cu(銅)・Al(アルミ):析出硬化元素として機能
- Nb(ニオブ)・Ti(チタン)など:炭化物形成に寄与し強度アップに貢献
- 構造は、マルテンサイト基に析出硬化相(CuやNiAl等)が微細に分散した構造となっている。
熱処理による強度と硬さの向上
- 溶体化処理:1050℃程度で急冷することで、単一なマルテンサイト組織を得る。
- 時効処理(析出処理):約480~620℃で数時間保持することで、析出物が生成され、硬度と強度が向上する。
- 析出物の効果:
- 析出物が転位の移動を妨げることで、金属組織の塑性変形を抑制。
- これにより、引張強さ・硬度・耐摩耗性が大幅に向上する。
- 同時に、寸法安定性にも優れた特性を発揮する。
- このメカニズムにより、加工性と高い機械的強度が両立可能となり、様々な産業分野で利用されている。
金属の時効と析出硬化処理
時効処理の定義と目的
- 時効処理とは:金属材料において、加熱または常温で一定時間保持することで、組織中に微細な析出物を生成させ、機械的性質(特に強度や硬さ)を向上させる処理のこと。
- 目的:
- 金属の引張強さ・硬度の向上
- 耐摩耗性・耐熱性の向上
- 微細構造を制御し、寸法安定性や靭性を確保する
時効処理と析出硬化処理の比較
- 共通点:
- どちらも微細な析出物の生成を利用し、金属の強化を目的とする。
- 材料の構造内部で析出反応を起こし、転位の動きを制御することで機械的特性を高める。
- 違い:
- 時効処理はより広義の概念であり、析出硬化もその一種に含まれる。
- 析出硬化処理は、特に溶体化処理 + 時効処理の2段階で行うことが多い。
- 析出硬化処理では、意図的に合金元素を設計し、特定の析出物(Ni3Al, Cu, Cr等)を得るようにする。
時効処理の工業的応用
- 時効処理は、以下のような合金や分野で広く応用されている:
- アルミニウム合金:
- 例:2024, 6061, 7075系など
- 航空機、精密機械部品、自動車構造部材に使用される
- チタン合金:
- 時効によって引張強さを高め、医療用インプラントや航空機部品に応用
- ニッケル基超合金:
- 耐熱性・強度の向上に寄与し、ジェットエンジンや発電用タービンに用いられる
- 析出硬化型ステンレス鋼(17-4PHなど):
- 高強度・高耐食性が求められる構造部品やシャフト類に活用されている
金属材料が変形するしくみ
金属の結晶構造と変形
- 金属は原子が規則正しく並んだ結晶構造をもつ。
- 主な結晶構造には以下がある:
- 体心立方構造(BCC)
- 面心立方構造(FCC)
- 六方最密構造(HCP)
- これらの構造は、金属の変形しやすさ(延性や塑性)に影響する。
- 変形は、転位(結晶内の欠陥)が移動することで生じる。
外力による金属の変形過程
- 金属に外力を加えると、最初は原子間の距離がわずかに変わることで応力に耐える。
- 応力が限界を超えると、転位が滑るように動き、結晶構造がずれて変形が始まる。
- このとき、金属全体が目に見える変形を起こすようになる。
- 一度転位が動き始めると、比較的少ない力でも連鎖的に変形が広がる。
塑性変形と弾性変形の違い
- 弾性変形:
- 外力を除くと、元の形に戻る変形。
- 原子間の距離が変わるが、結晶構造は保たれている。
- 弾性限界を超えない範囲でのみ発生。
- 塑性変形:
- 外力を除いても、元の形に戻らない永久変形。
- 結晶内の転位が移動し、構造自体がずれる。
- 加工や成形において最も重要な変形。
金属材料の強化方法
冷間加工による強化
- 金属を常温で圧延、引張、圧縮などの塑性変形を加えることで強度を高める方法。
- 転位密度が増加し、転位の移動が困難になることで硬化する。
- 一般的に「加工硬化」や「ひずみ硬化」とも呼ばれる。
- デメリットとして、加工が進むと延性が低下する。
合金化による強化
- 複数の金属元素を組み合わせて、金属の構造内に異種原子を導入する。
- 異種原子が格子ひずみを生じ、転位の移動を妨げる。
- 固溶強化(固溶体の形成)や析出強化(微細な粒子の析出)などの効果がある。
- 鉄に炭素を加える鋼や、アルミニウムに銅やマグネシウムを加える例が代表的。
熱処理による強化
- 加熱と急冷、あるいは特定の温度での保持によって、金属の組織を変化させる手法。
- 焼入れ、焼戻し、焼なまし、析出硬化などの手法がある。
- 強度だけでなく、硬さや耐摩耗性などの調整も可能。
表面処理による強化
- 金属表面に限定して処理を施し、表面の硬度や耐食性を高める方法。
- 代表的な方法には、浸炭、窒化、ショットピーニング、めっき、コーティングなどがある。
- 表面のみを強化するため、内部の靱性や延性を保ったまま高性能化できる。
析出硬化処理の工業的応用
航空宇宙産業での応用
- 目的と要求性能:
- 航空宇宙産業では、使用される材料に対して高い強度、軽量性、耐熱性、耐食性が求められます。
- 析出硬化処理を施した材料は、これらの要求に最適な特性を持ち、過酷な環境で使用されます。
- 適用例:
- 航空機部品: 航空機の機体やエンジン部品は高強度と軽量性を兼ね備えた素材が必要です。析出硬化型のアルミニウム合金(例:2024系、7075系アルミニウム合金)は、非常に高い強度を持ちつつ、軽量性も保持できるため、航空機の構造部品や翼、エンジン部品に使用されています。
- ロケット部品: ロケットのエンジン部品や推進装置には、極めて高い耐熱性と強度が求められます。析出硬化アルミニウムやチタン合金(Ti-6Al-4Vなど)は、ロケットの耐熱部品や構造部材に適用され、長期間の耐用性と安定性を提供します。
- 金属3Dプリンティング: 航空宇宙産業では、金属3Dプリンティング技術が活用され、析出硬化型合金がプリントされることで、従来の製造方法よりも軽量で強度のある部品が製造されています。
自動車産業での応用
- 目的と要求性能:
- 自動車産業では、燃費効率と安全性を両立させるために、軽量化と強度の向上が非常に重要です。また、耐摩耗性や耐久性も必須要素です。
- 適用例:
- 車体構造材: 自動車の車体やシャーシには軽量で高強度な材料が求められます。析出硬化型アルミニウム合金(例:6000系、7000系)は、優れた強度と軽量性を持ち、車両構造材や衝突エネルギー吸収部品に使用されます。
- サスペンション部品: 自動車のサスペンション部品には高い強度と靱性が必要です。析出硬化処理されたアルミニウム合金や鋼合金は、サスペンション部品やアクスル、シャフトなどに使われ、長期間の使用に耐えることができます。
- エンジン部品: 自動車エンジンの重要な部品(ギア、シャフト、バルブ、ピストンなど)は、高い耐摩耗性と耐熱性を持つ材料が使用されます。析出硬化した鋼やアルミニウム合金はこれらの部品に適用され、エンジンの性能向上に寄与しています。
- 電動車部品: 電気自動車(EV)のバッテリーパックやモーターにおいても、析出硬化処理された軽量な合金が採用され、電動車のパフォーマンス向上とバッテリー効率の向上に貢献しています。
医療器具への応用
- 目的と要求性能:
- 医療機器においては、生体適合性、強度、耐食性、耐久性が特に重要です。特にインプラントや手術器具などは、安全性と信頼性が求められます。
- 適用例:
- 手術器具: 高精度な手術器具や医療用工具には、優れた耐食性と強度が必要です。析出硬化型ステンレス(例:17-4PHステンレス鋼)は、手術用メス、鉗子、ペンチ、ドリルビットなどの器具に使用され、高い耐摩耗性と耐腐食性を発揮します。
- インプラント部品: 生体内で使用されるインプラント(人工関節、歯科インプラントなど)にも析出硬化型ステンレスやチタン合金が使用されます。これにより、インプラント部品の強度や耐久性が向上し、体内での長期間の使用が可能となります。
- 歯科用工具: 歯科用の治療器具(スケーラー、カッター、ドリルなど)にも析出硬化ステンレスが使用され、鋭さと耐久性を確保しています。これにより、高精度の治療が可能となり、患者に対する安全性が向上します。
その他の工業分野での応用
- 金型産業: 金型は製品の精度と耐久性を決定づける重要な部分です。析出硬化型鋼(例:P20、H13など)は金型の製作に使用され、長寿命と優れた耐摩耗性を提供します。
- 電子機器: 析出硬化型材料は、携帯電話やコンピュータ部品などの電子機器においても使用され、信号の伝達精度や機器内部の熱管理に寄与しています。
- 鉄道産業: 鉄道車両の車輪、シャフト、ギアなどに使用される材料にも析出硬化型合金が使用され、高強度と耐摩耗性を確保しています。