SUS316の高品質加工法:溶接性と加工性の向上テクニック
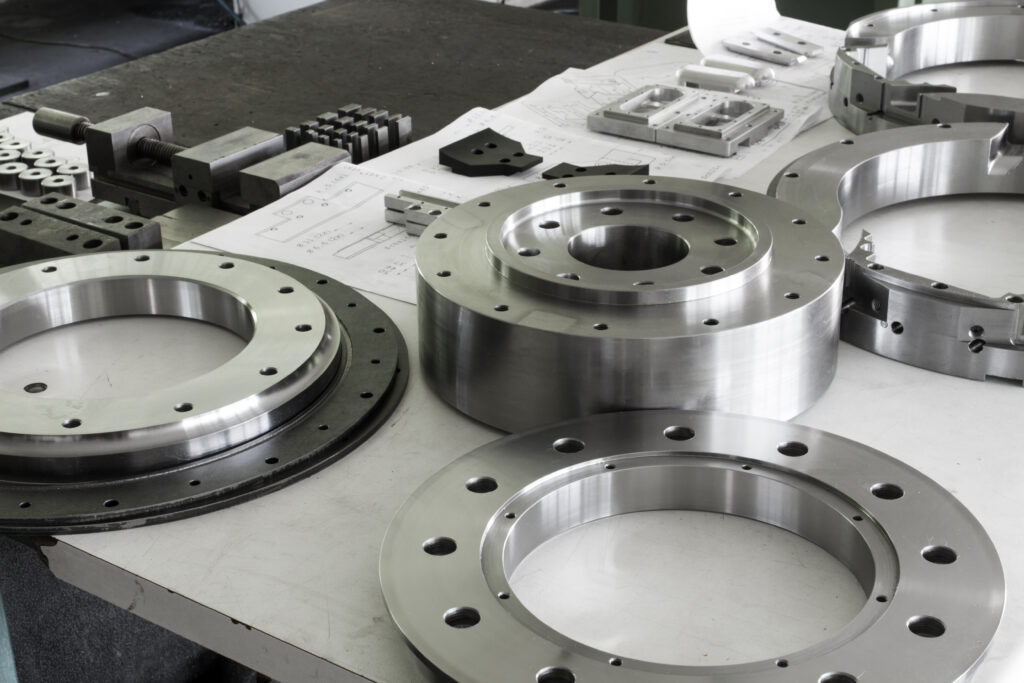
SUS316は、その高い耐食性や強度などの特徴から、様々な産業分野で広く使用されています。しかし、その加工においては、溶接性や加工性の向上が課題となることもあります。本記事では、SUS316の高品質加工法に焦点を当てて、その溶接性と加工性を向上させるテクニックについて詳しく解説します。切削性や焼き入れなどの要素も含め、SUS316を効果的に加工するための情報をお届けします。加工技術の向上を目指す方々にとって、この記事は貴重な参考になることでしょう。
SUS316をはじめとするステンレス鋼の加工は、確かに難易度の高い作業ですが、加工性に関する知識とノウハウの蓄積、設備の最適化によって十分に克服可能です。現場の課題と向き合い、試行錯誤を繰り返す中で、より高精度・高品質な製品製造が実現できます。
SUS316の基本とその加工性
SUS316とは:ステンレス鋼の特徴
SUS316は、オーステナイト系ステンレス鋼に分類される高耐食性材料であり、特にモリブデン(Mo)を約2〜3%含有する点が特徴です。このモリブデンの添加により、塩素イオンを含む腐食環境(例:海水、化学薬品)に対して強い耐性を発揮します。以下のような特性を持ち、幅広い用途に使用されています。- 優れた耐食性(特にSUS304よりも塩素耐性に優れる)
- 高温環境でも安定な性能(酸化スケールの生成を抑制)
- 非磁性で衛生的な材質(食品・医療分野でも活用)
- 溶接性や成形性にも良好
加工性に影響を与えるSUS316の物理的特性
SUS316の加工性、特に切削や成形において重要となる物理的・機械的特性は以下のとおりです。- 引張強さ:約540〜750 MPa(高強度)
- 伸び率:約40%以上(延性が高く成形性良好)
- 硬さ(HB):160〜190(SUS304と同等またはやや高い)
- 熱伝導率:約16.3 W/m·K(熱がこもりやすく切削中に熱集中しやすい)
- 比重:約8.0
- ヤング率:193 GPa(変形に対する剛性を示す)
切削性とは:基本的な概念の解説
切削性(machinability)とは、金属材料が「どれだけ加工しやすいか」を表す性能指標です。具体的には以下の観点で評価されます:- 切削抵抗の小ささ
- 工具寿命の長さ
- 加工面の仕上がり(粗さ)
- 切りくずの処理のしやすさ
- 冷却・潤滑の効きやすさ
- 超硬工具やコーティング工具の使用
- 適切な切削条件(低速・高送り)
- 切削油の積極的使用(ミストや高圧クーラント)
SUS316の切削加工方法とその注意点
SUS316は、耐食性に優れたオーステナイト系ステンレス鋼であり、医療機器や化学プラント、海洋部品など幅広い分野で使用されています。しかしその一方で、切削加工においては難削材とされており、適切な加工方法と注意点を理解しておくことが重要です。切削加工の基礎知識
切削加工とは、工具を用いて金属を削り、目的の形状に仕上げる加工方法です。切削時には素材の硬さや靭性、熱伝導性などが加工性に大きく影響します。SUS316は高い強度と粘りを持つため、一般的な鋼材よりも切削工具に負荷がかかりやすく、加工熱の蓄積にも注意が必要です。具体的な切削加工手順
- 材料の固定 ワークの固定は振動を防ぐために強固に行います。不安定な固定は加工精度の低下や工具破損の原因となります。
- 適切な工具の選定 SUS316に適した超硬工具やコーティング工具(TiAlN、TiCNなど)を使用することで、摩耗を抑え、工具寿命を延ばすことができます。
- 切削条件の設定 低速・高送りが基本です。回転数を抑えつつ、適切な切込みと送り速度を設定します。高回転は加工熱を増やし、バリや焼き付きの原因になります。
- 切削油の使用 冷却と潤滑のために切削油を十分に供給します。ミストやエマルジョンタイプの切削油が効果的です。
- 断続加工の回避 工具への衝撃を避けるため、連続加工が望ましく、断続切削は可能な限り避ける設計と加工順序を心がけます。
切削加工における問題点と対策
- 工具摩耗の早さ SUS316は硬く粘りがあるため、切削時に工具が摩耗しやすくなります。これを防ぐには、工具材質やコーティングの選定が重要です。また、定期的な工具交換を前提とした工程管理も必要です。
- バリの発生 加工時に生じるバリは、エッジの品質や寸法精度に影響を及ぼします。切削条件の最適化や後処理工程(バリ取り)の導入により対処します。
- 加工熱の蓄積 SUS316は熱伝導率が低いため、加工中に発生した熱が工具や加工面にこもりやすくなります。切削油による冷却や、インターバルを設けた加工が有効です。
切削性向上のための焼き入れ処理
一般的にSUS316は焼き入れにより硬化する材質ではありませんが、冷間加工により加工硬化を生じる性質を持っています。逆に、この加工硬化が切削性をさらに悪化させる場合があるため、必要以上の予備加工や曲げ加工は避けるべきです。熱処理によって切削性を向上させるというよりも、素材の状態を安定させるための焼鈍処理(アニール)が有効です。アニール処理によって内部応力が除去され、より均質で加工しやすい状態になります。 以上のように、SUS316の切削加工には材料特性を理解したうえで、適切な工具選定と加工条件、そして冷却手段の導入が不可欠です。SUS316の旋盤加工の基礎
SUS316は耐食性・耐熱性に優れたオーステナイト系ステンレス鋼であり、医療機器や化学設備、食品機械など幅広い分野で用いられます。旋盤加工はそのようなSUS316を精密に加工するための代表的な手段の一つですが、SUS316の特性を踏まえた適切な加工知識が必要です。旋盤加工とは:基本操作と適用範囲
旋盤加工は、円筒状の材料を回転させ、バイトと呼ばれる切削工具を用いて外径・内径・端面などを加工する方法です。円柱形状の加工に適しており、寸法精度や表面粗さが求められる機械部品の製作に多く用いられます。基本的な操作は以下の通りです:- ワークの芯出しとチャッキング(固定)
- 主軸回転によるワークの回転
- 切削工具の移動による除去加工
- 工具交換・送り速度調整・切削深さ調整
SUS316の旋盤加工法
SUS316は粘りがあり、加工中に発生する熱が工具に蓄積しやすいため、旋盤加工では以下のような工法が推奨されます。- 低速回転・高送りの設定:熱の蓄積を防ぎ、バリの発生を抑えるため、低回転で高送り条件に設定する。
- 超硬工具やコーティングバイトの使用:TiAlNやTiCNコーティングなど、高硬度・高耐熱の工具が効果的。
- 切削油の多用:冷却・潤滑・切りくず排出のため、ミストまたはエマルジョン系切削油を連続的に供給する。
- 中切削〜仕上げ切削に工程を分ける:一度に多く削るのではなく、粗削りと仕上げ削りを分け、工具寿命と精度を両立させる。
旋盤加工時の注意点と品質管理
SUS316を旋盤加工する際の主な注意点と、それに対する品質管理の要点は以下の通りです。- 切削熱による工具摩耗 熱がこもることで工具寿命が著しく短くなるため、冷却の徹底と工具状態の定期点検が重要です。
- 加工硬化による精度低下 SUS316は加工硬化性が高く、何度も同じ箇所を削ると硬化が進んで仕上げ精度に悪影響が出ます。必要最小限の加工パスで完結する工程設計が求められます。
- 切りくず排出の不良 長い切りくずが工具に巻き付くと表面粗さが低下し、工具破損の原因にもなります。切りくず除去装置やチップブレーカーの活用が効果的です。
- 仕上げ精度と寸法管理 バイトの磨耗状況やワークの熱膨張を加味した寸法調整が必要です。定期的なノギス・マイクロメータによる測定で品質を維持します。
SUS316の溶接性と溶接技術
SUS316は耐食性や耐熱性に優れ、化学設備や医療機器、食品関連分野などで広く使用されているオーステナイト系ステンレス鋼です。これらの分野では高品質な接合が求められるため、SUS316の溶接性とその最適化技術を理解することが極めて重要です。溶接性の基本
溶接性とは、金属材料が溶接によって接合されやすい性質を指します。良好な溶接性とは、割れや歪み、欠陥の発生が少なく、接合部の強度や耐食性が母材と同等、またはそれに近いレベルで確保されることを意味します。ステンレス鋼の場合は、熱の影響による組織変化や応力、酸化の管理が溶接性を左右する要因です。 SUS316は比較的溶接性の高い鋼種とされていますが、溶接時には注意点も多く存在します。SUS316の溶接方法と最適化
SUS316の溶接には、以下のような溶接法が主に使用されます。- TIG溶接(アルゴン溶接) 精密な溶接が可能で、酸化やスパッタが少なく、美しいビードが得られます。薄板から中厚板まで対応でき、医療・食品分野でも多用されます。
- MIG溶接(CO₂/MAG溶接) 生産性が高く、大量生産や自動化に適していますが、酸化スケールが出やすいため、後処理が必要な場合があります。
- レーザー溶接やプラズマ溶接 高精度な加工が可能で、歪みが少なく、熱影響部が最小限に抑えられるため、高機能製品で活用されます。
最適化のポイント
- 適切な溶加材の選定 SUS316には、モリブデンを含んだ溶加材(例:ER316L)が推奨されます。これにより、溶接部の耐食性が母材に近づきます。
- 低炭素材(Lグレード)の使用 SUS316Lを使用することで、溶接時の炭化物析出による耐食性の低下(結晶粒界腐食)を防止できます。
- シールドガスの活用 溶接中および溶接後の酸化を防ぐため、アルゴンやヘリウムなどのシールドガスの流量とカバー範囲を適切に制御する必要があります。
溶接時の問題点と解決策
SUS316の溶接では、以下のような問題が発生する可能性があり、それぞれに対応策が求められます。- 結晶粒界腐食 高温時にクロム炭化物が粒界に析出し、耐食性が低下する現象。 → 対策:SUS316Lの使用、適切な熱管理、短時間での溶接完了。
- 溶接歪みと反り オーステナイト系ステンレスは熱膨張係数が大きく、歪みが発生しやすい。 → 対策:対称的な溶接手順、予熱・後熱の調整、溶接治具の使用。
- ピット腐食の発生 モリブデンが不足した場合、局部的な腐食が起こりやすい。 → 対策:適切なモリブデン含有溶加材の選定、溶接後の酸洗いやパッシベーション処理。
- 酸化スケールや変色 高温にさらされることで酸化皮膜が生成され、外観不良や腐食の原因となる。 → 対策:アルゴンパージの徹底、溶接後の化学洗浄。
ステンレス加工の難しさとその克服
ステンレス鋼は耐食性や耐熱性、強度に優れることから、食品、医療、化学、建築など多岐にわたる分野で使用されています。しかしその優れた特性が、加工においては一転して「扱いにくさ」として現れることもあります。ここでは、ステンレス加工における一般的な課題、SUS316特有の難しさ、そして現場で培われた克服の工夫について解説します。ステンレス加工の一般的な課題
1. 加工硬化の問題
ステンレス鋼は加工硬化性が高く、曲げや切削などの機械的加工を行うと、加工部が急激に硬化します。この硬化層が工具の摩耗を早め、切削性を著しく低下させます。2. 熱伝導性の低さ
ステンレスは熱伝導率が低いため、切削や溶接時に熱が局所に集中しやすく、熱による歪みや変色、焼き付きのリスクが高まります。3. 高い延性と弾性
塑性加工の際にばね戻りが発生しやすく、精度の高い加工には工夫が必要です。特に曲げ加工やプレス成形では、寸法誤差の原因になります。4. 工具の摩耗と焼き付き
高い粘性により工具に材料が付着しやすく、切削工具の刃先に焼き付きが発生することがあります。これにより、仕上がり面の粗れや工具寿命の低下が起こります。SUS316加工の特有の難しさ
SUS316はモリブデンを含有しているため、SUS304よりも耐食性に優れる一方で、以下のような加工上の課題があります。・さらに高い加工硬化性
SUS316はSUS304と比べてさらに加工硬化しやすく、同様の加工条件では工具への負荷が大きくなります。・工具摩耗の進行が早い
高強度に加え、粘性も高いため、ドリルやエンドミルなどの切削工具が摩耗しやすく、加工コストや工数の増加につながります。・熱ひずみや変色
熱が集中しやすく、特に溶接や高速切削の現場では、母材の色変化や熱によるゆがみ対策が必要になります。・表面仕上げの難易度
加工後に鏡面やヘアラインなどの高品位仕上げを求められることが多いため、研磨や酸洗などの後工程にも工夫が求められます。成功事例から学ぶ:加工のコツと工夫
■ 工具材質とコーティングの最適化
超硬工具やセラミック工具に加え、TiAlNやCrNなどの耐熱性・耐摩耗性に優れたコーティングを施すことで、工具寿命を延ばしつつ焼き付きを防ぎます。■ 適切な切削条件の設定
低速・高送りを基本とし、切削速度やクーラント供給を適切に制御します。特にエマルジョンクーラントの使用が、焼き付きや熱変形の抑制に有効です。■ 切りくずの排出性向上
切りくずが詰まると加工面に傷がつき、工具破損の原因になります。チップブレーカ付き工具や高圧クーラントの併用が効果的です。■ 加工後の表面処理の徹底
溶接や切削後には、酸洗や電解研磨、パッシベーション処理を行い、表面の酸化スケールや鉄粉汚染を除去して耐食性を回復させます。■ 曲げ加工時のばね戻り対策
試作段階でばね戻り量を把握し、型の角度を調整することで、狙い通りの形状が得られるようになります。押し込み量やR部の設計も調整が重要です。■ 熟練者の技術と現場ノウハウ
SUS316のような難加工材の加工では、CAD/CAMによるシミュレーションと、現場での経験的な知見の融合が成果に直結します。SUS316をはじめとするステンレス鋼の加工は、確かに難易度の高い作業ですが、加工性に関する知識とノウハウの蓄積、設備の最適化によって十分に克服可能です。現場の課題と向き合い、試行錯誤を繰り返す中で、より高精度・高品質な製品製造が実現できます。